Verification of sieves is a critical process to ensure the accuracy and reliability of sieves used in particle size analysis. It involves a series of checks and tests to confirm that the sieve meets specified standards, ensuring consistent and precise results. This process is essential for both new and used sieves, as it helps maintain quality control and ensures compliance with industry standards. Verification includes visual inspection, performance testing, and documentation to confirm the sieve's integrity and functionality.
Key Points Explained:
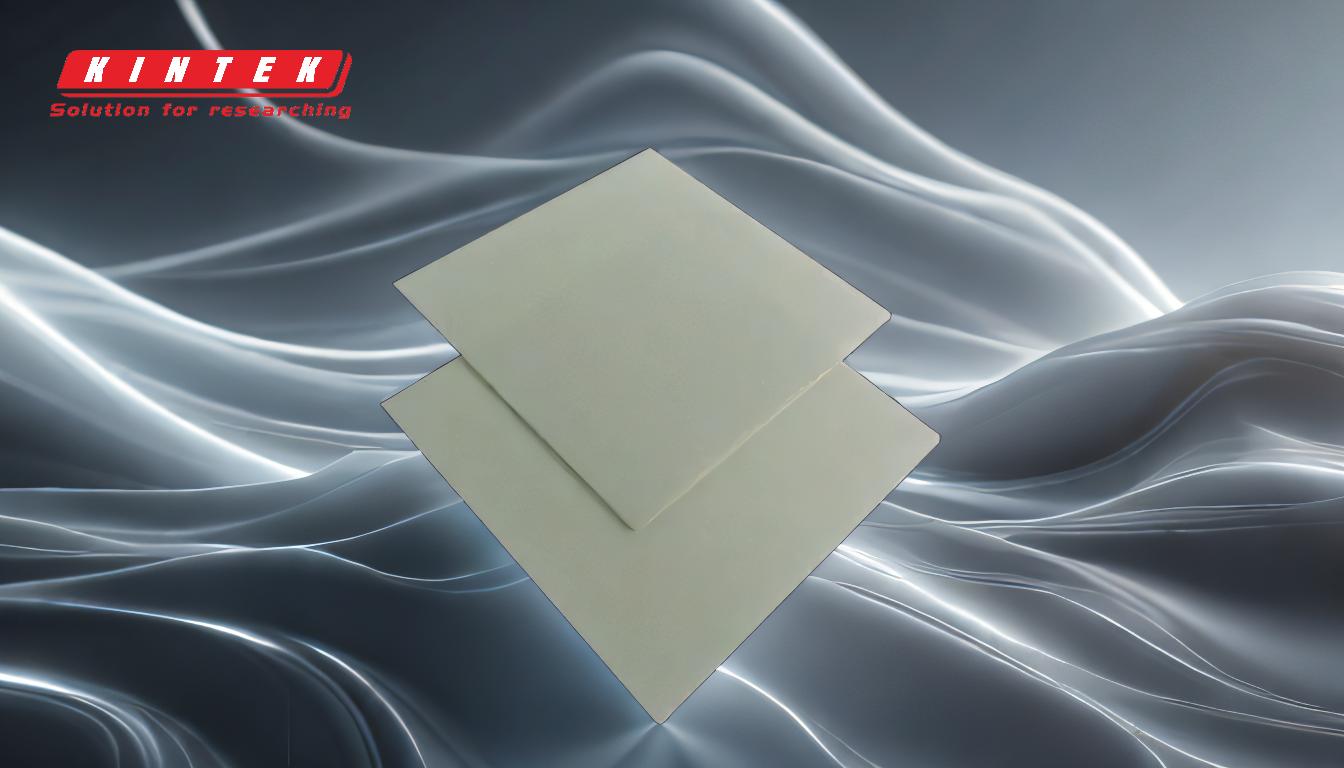
-
Purpose of Verification:
- Verification ensures that sieves perform accurately and consistently.
- It is crucial for maintaining quality control in particle size analysis.
- Both new and used sieves undergo verification to confirm their compliance with standards.
-
Visual Inspection:
- The first step in verification involves a thorough visual examination of the sieve.
- Inspectors look for physical defects such as tears in the mesh, wavy mesh, or cracks in the epoxy.
- Any damage found during this inspection can affect the sieve's performance and must be addressed before further testing.
-
Performance Testing:
- After visual inspection, the sieve undergoes performance testing to ensure it meets specified standards.
- This involves passing a known sample through the sieve and comparing the results to expected outcomes.
- Performance testing helps identify any deviations in the sieve's ability to accurately separate particles by size.
-
Re-verification:
- Re-verification is the process of checking the performance of used sieves.
- It is similar to the verification process for new sieves and is often part of an internal quality control/quality assurance program.
- Regular re-verification helps ensure that sieves continue to perform accurately over time, even after repeated use.
-
Documentation:
- Proper documentation is essential during the verification process.
- Records of visual inspections, performance tests, and any corrective actions taken are maintained.
- This documentation provides a traceable history of the sieve's performance and compliance with standards.
-
Importance in Quality Assurance:
- Verification and re-verification are integral parts of a quality assurance program.
- They help ensure that the results of particle size analysis are reliable and reproducible.
- Regular verification processes help identify and correct any issues early, preventing potential errors in analysis.
By following a structured verification process, organizations can ensure that their sieves are in optimal condition, providing accurate and consistent results in particle size analysis. This not only enhances the reliability of the data but also supports compliance with industry standards and regulations.
Summary Table:
Aspect | Details |
---|---|
Purpose | Ensures accurate and consistent sieve performance. |
Visual Inspection | Checks for physical defects like tears, wavy mesh, or cracks. |
Performance Testing | Compares sieve results with expected outcomes to identify deviations. |
Re-verification | Ensures used sieves continue to meet standards over time. |
Documentation | Maintains records of inspections, tests, and corrective actions. |
Quality Assurance | Supports reliable, reproducible results and compliance with industry standards. |
Ensure your sieves meet industry standards—contact us today for expert verification services!