Zirconia sintering is a critical thermal process used to transform zirconia powder into a dense, solid material with enhanced mechanical properties. It involves heating zirconia at high temperatures below its melting point, which reduces porosity, increases density, and improves strength and structural integrity. The process typically includes steps such as composition, compression, and controlled heating, resulting in significant shrinkage and the formation of a low-porosity, high-strength ceramic material. Sintering is essential for applications requiring durable and precise zirconia components, such as dental crowns, industrial tools, and biomedical implants.
Key Points Explained:
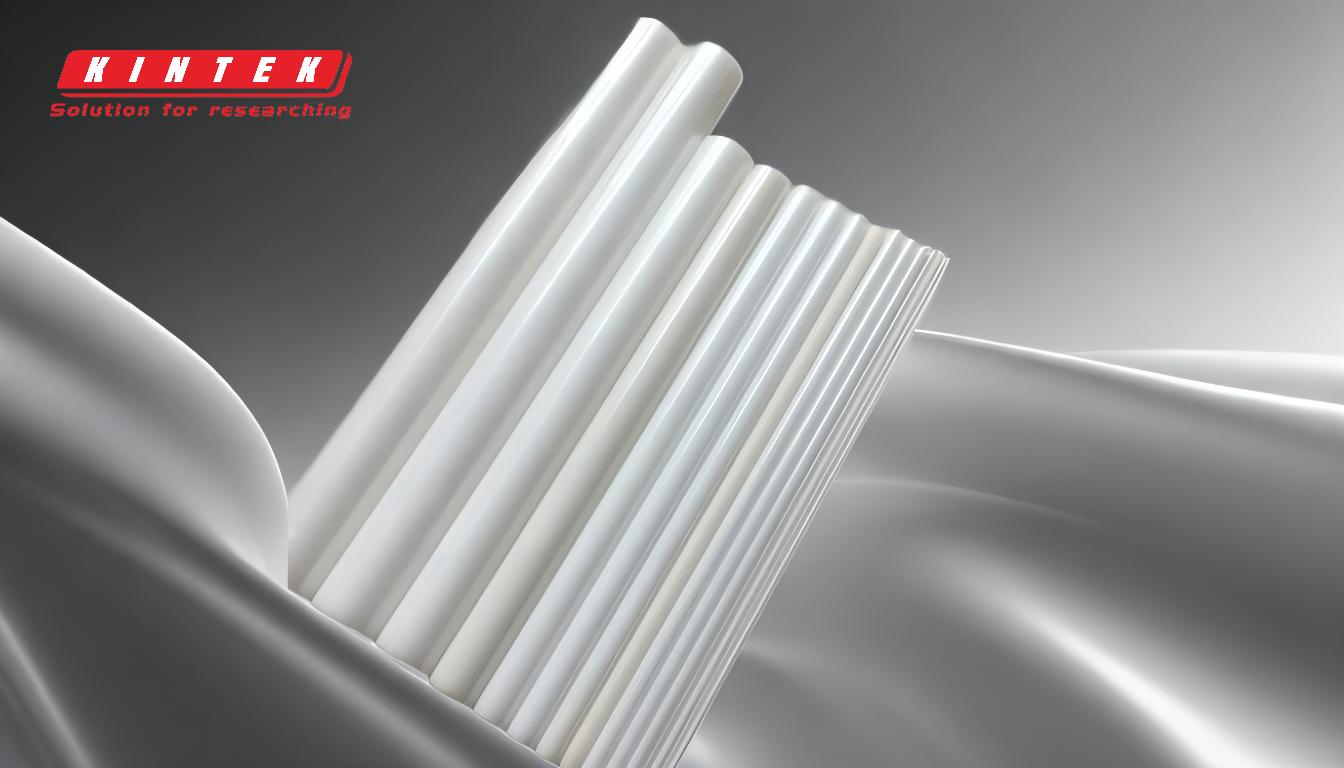
-
Definition of Zirconia Sintering
- Zirconia sintering is a thermal process where zirconia powder is heated to high temperatures below its melting point.
- The goal is to fuse particles together into a solid mass without liquefying the material, enhancing its mechanical properties.
-
Purpose and Importance
- The primary purpose of sintering is to reduce porosity and increase the density of zirconia, resulting in a stronger and more durable material.
- This process is crucial for achieving the final hardness, structural integrity, and mechanical strength required for high-performance applications.
-
Key Steps in the Sintering Process
- Composition: Mixing primary zirconia materials with coupling agents to prepare the powder.
- Compression: Pressing the powder into the desired shape using molds or dies.
- Heating: Subjecting the shaped zirconia to controlled high temperatures to remove coupling agents and fuse particles into a dense, low-porosity structure.
-
Effects of Sintering on Zirconia
- Shrinkage: Zirconia undergoes significant shrinkage during sintering, which must be accounted for in the design and manufacturing process.
- Density and Porosity: Sintering reduces porosity and increases density, improving the material's strength and durability.
- Mechanical Properties: The process enhances hardness, wear resistance, and structural integrity, making zirconia suitable for demanding applications.
-
Applications of Sintered Zirconia
- Sintered zirconia is widely used in dental restorations (e.g., crowns and bridges) due to its biocompatibility and strength.
- It is also utilized in industrial tools, cutting instruments, and biomedical implants, where durability and precision are critical.
-
Advantages of Sintering
- Produces high-strength, low-porosity materials with excellent mechanical properties.
- Enables precise control over the final shape and dimensions of zirconia components.
- Suitable for mass production of complex and high-performance ceramic parts.
By understanding the principles and steps involved in zirconia sintering, manufacturers and purchasers can ensure the production of high-quality zirconia components tailored to specific applications.
Summary Table:
Aspect | Details |
---|---|
Definition | A thermal process heating zirconia powder below its melting point. |
Purpose | Reduces porosity, increases density, and enhances mechanical properties. |
Key Steps | Composition, compression, and controlled heating. |
Effects | Shrinkage, increased density, and improved hardness and wear resistance. |
Applications | Dental crowns, industrial tools, and biomedical implants. |
Advantages | High strength, low porosity, and precise control over final dimensions. |
Discover how zirconia sintering can elevate your product quality—contact our experts today!