Furnace insulation materials are critical for maintaining high temperatures, ensuring energy efficiency, and extending the lifespan of the equipment. Common materials used include high-purity microcrystalline alumina fiber, ceramic fibers, and lightweight refractory bricks. These materials are chosen based on their ability to withstand high temperatures, thermal conductivity, and durability. For instance, microcrystalline alumina fiber is ideal for high-temperature applications, while ceramic fibers and refractory bricks provide excellent insulation and heat retention. The selection of insulation material depends on the furnace's operating temperature, with materials often rated to withstand temperatures higher than the furnace's maximum operating temperature to ensure safety and longevity.
Key Points Explained:
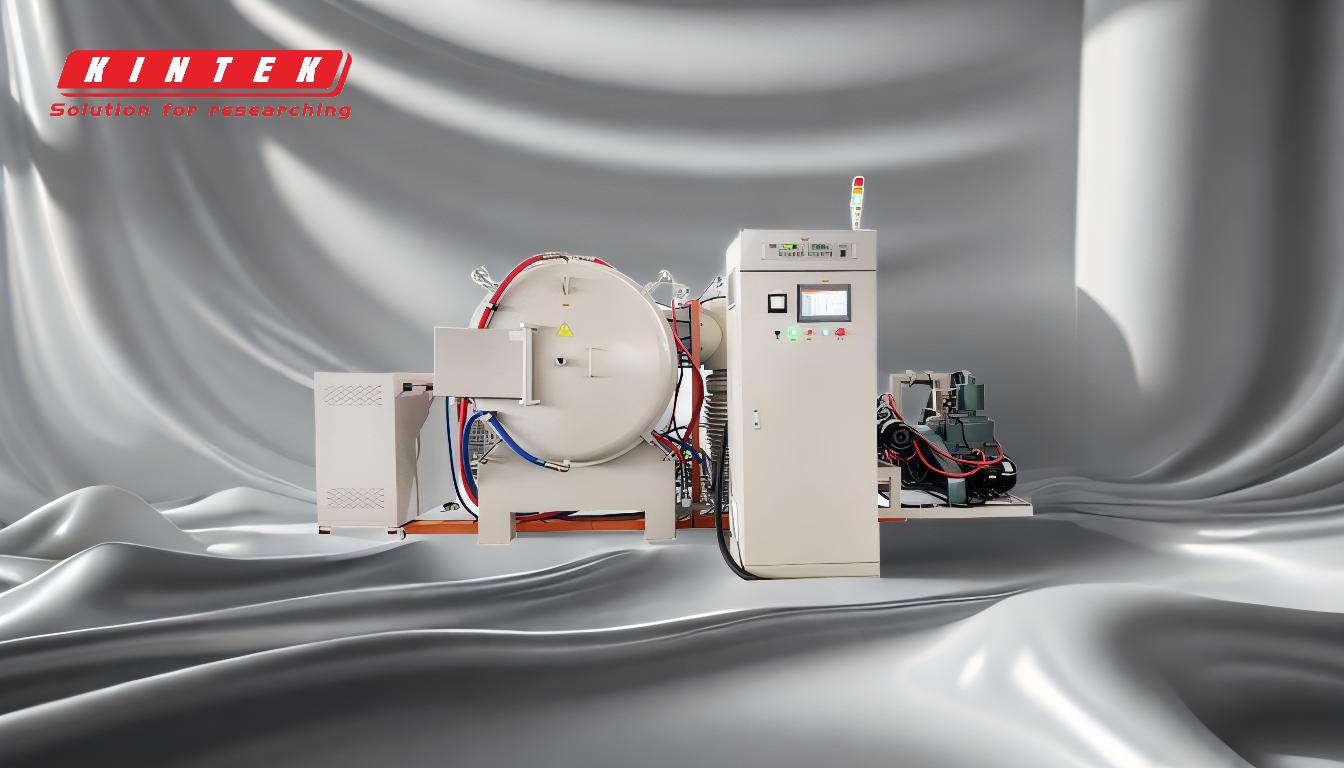
-
High-Purity Microcrystalline Alumina Fiber:
- This material is specifically mentioned for its heat insulation and preservation properties.
- It is suitable for high-temperature applications due to its high thermal stability and low thermal conductivity.
- Microcrystalline alumina fiber is often used in furnaces where temperatures exceed 1000℃, as it can withstand temperatures up to 1200℃ or higher.
- Its lightweight nature and excellent insulation properties make it a preferred choice for modern high-temperature furnaces.
-
Ceramic Fibers:
- Ceramic fibers are another common insulation material used in muffle furnaces.
- They are lightweight, have low thermal conductivity, and can withstand high temperatures, making them ideal for insulation.
- Ceramic fibers are often used in combination with other materials, such as refractory bricks, to enhance insulation performance.
- They are flexible and can be shaped to fit the furnace lining, providing uniform insulation.
-
Lightweight Refractory Bricks:
- Refractory bricks are traditional insulation materials known for their durability and ability to withstand extreme temperatures.
- Lightweight refractory bricks are preferred for their improved insulation properties compared to standard bricks.
- They are often used in multi-layered insulation systems to enhance heat retention and reduce energy loss.
- These bricks are commonly lined inside the furnace to provide structural support and insulation.
-
Multi-Layered Insulation:
- Furnaces often use multi-layered insulation systems to improve performance.
- This approach combines different materials, such as ceramic fibers and refractory bricks, to maximize heat retention and minimize energy loss.
- Multi-layered insulation ensures that the furnace can maintain high temperatures efficiently while protecting the outer structure from excessive heat.
-
Temperature Considerations:
- The choice of insulation material depends on the furnace's operating temperature.
- For example, if the furnace operates at 1000℃, the insulation material should be rated to withstand 1100℃ to 1200℃ to ensure safety and longevity.
- Over-specifying the temperature rating of the insulation material helps prevent damage and extends the furnace's lifespan.
-
Energy Efficiency and Heat Loss Prevention:
- High-quality insulation materials, such as ceramic fibers and refractory bricks, help conserve energy by reducing heat loss.
- Effective insulation ensures that the furnace maintains consistent temperatures, reducing the need for frequent reheating and lowering energy consumption.
- Proper insulation also prevents heat from escaping into the surrounding environment, improving overall efficiency.
-
Durability and Longevity:
- Insulation materials must be durable to withstand the harsh conditions inside a furnace.
- High-purity microcrystalline alumina fiber, ceramic fibers, and refractory bricks are chosen for their ability to resist thermal degradation and mechanical stress.
- Using materials with higher temperature ratings than the furnace's operating temperature ensures that the insulation remains effective over time.
In conclusion, the selection of furnace insulation materials depends on the specific requirements of the furnace, including operating temperature, energy efficiency, and durability. High-purity microcrystalline alumina fiber, ceramic fibers, and lightweight refractory bricks are commonly used due to their excellent thermal properties and ability to withstand high temperatures. Multi-layered insulation systems further enhance performance by combining these materials to achieve optimal heat retention and energy efficiency.
Summary Table:
Material | Key Properties | Applications |
---|---|---|
High-Purity Microcrystalline Alumina Fiber | High thermal stability, low thermal conductivity, lightweight | High-temperature furnaces (above 1000℃) |
Ceramic Fibers | Lightweight, low thermal conductivity, flexible | Muffle furnaces, multi-layered insulation systems |
Lightweight Refractory Bricks | Durable, excellent heat retention, structural support | Multi-layered insulation, structural furnace lining |
Multi-Layered Insulation Systems | Combines materials for maximum heat retention and energy efficiency | High-performance furnaces |
Need help selecting the right insulation material for your furnace? Contact our experts today for personalized advice!