PVD (Physical Vapor Deposition) coating is a versatile and advanced surface treatment technique that involves depositing thin layers of materials atom by atom onto a substrate. The materials used for PVD coatings are diverse and tailored to specific applications, offering enhanced properties such as hardness, wear resistance, corrosion resistance, and aesthetic appeal. Common materials include metals like titanium, zirconium, and chromium, as well as ceramics such as titanium nitride (TiN), chromium nitride (CrN), and diamond-like carbon (DLC). These materials are chosen based on the desired performance characteristics and the type of substrate being coated. PVD coatings are widely used in industries ranging from automotive and aerospace to medical and tooling, providing durability and longevity to products.
Key Points Explained:
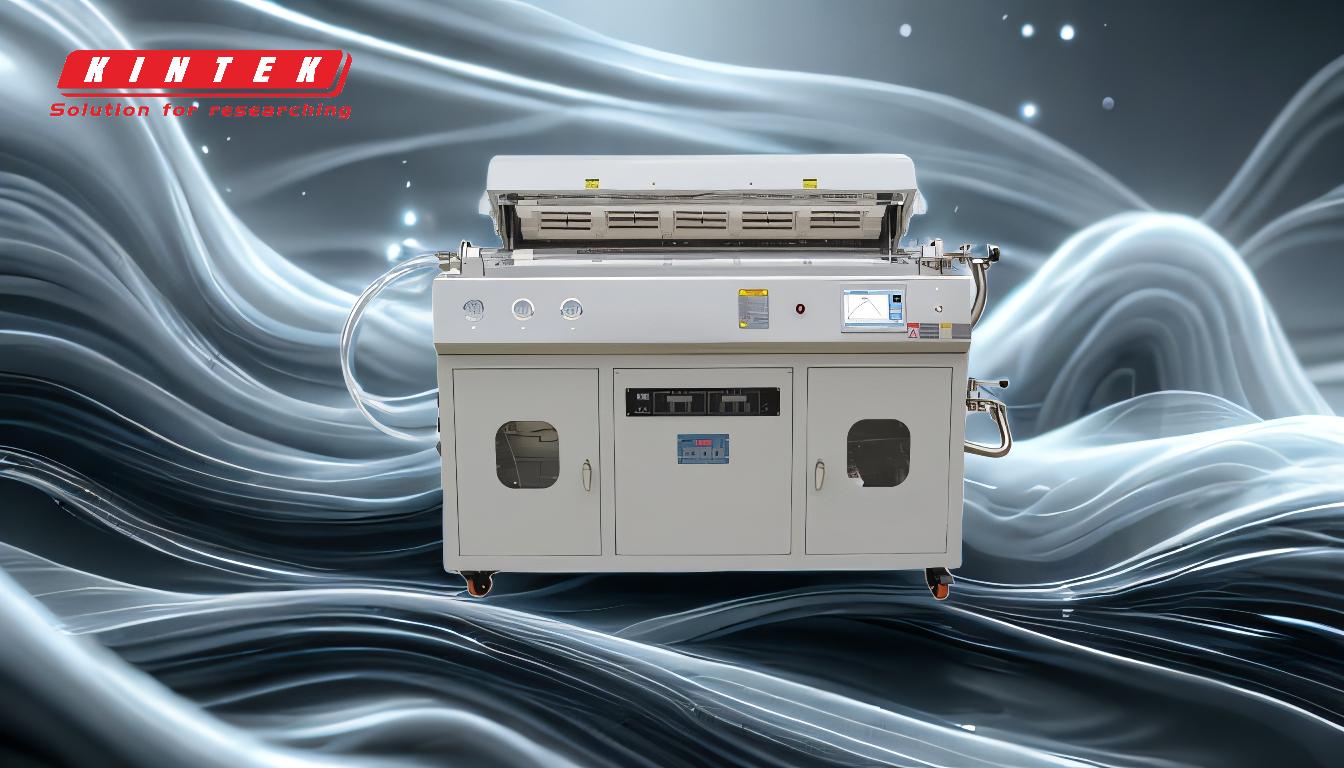
-
Materials Used in PVD Coating:
- PVD coatings utilize a variety of materials, including metals, ceramics, and specialized compounds. Common examples include:
- Titanium Nitride (TiN): Known for its gold-like appearance, high hardness, and excellent wear resistance, TiN is widely used in cutting tools, molds, and decorative applications.
- Chromium Nitride (CrN): Offers superior corrosion resistance and is often used in plastic molding dies and medical instruments.
- Zirconium Nitride (ZrN): Provides a golden color and is used for decorative purposes and wear-resistant coatings.
- Diamond-like Carbon (DLC): Known for its exceptional hardness and low friction, DLC is used in automotive components and high-performance tools.
- PVD coatings utilize a variety of materials, including metals, ceramics, and specialized compounds. Common examples include:
-
Substrates Suitable for PVD Coating:
- PVD coatings can be applied to a wide range of substrates, including:
- Steel Families: High-alloy steels like high-speed steels and stainless steels are commonly coated due to their compatibility with PVD processes.
- Non-Ferrous Metals: Materials such as copper, aluminum, and their alloys can also be coated, enhancing their durability and performance.
- Chrome or Nickel-Plated Metals: These materials are suitable for PVD coating, but brass without galvanization or galvanized materials are not recommended due to their incompatibility with vacuum processes.
- PVD coatings can be applied to a wide range of substrates, including:
-
Applications of PVD Coatings:
- PVD coatings are used in various industries to improve the performance and lifespan of products. Key applications include:
- Automotive: Coating car parts like wheels and pistons to enhance durability and resistance to wear and corrosion.
- Medical: Coating surgical tools to improve their longevity and resistance to sterilization processes.
- Tooling: Coating drill bits and molds to increase their hardness and wear resistance.
- Aerospace: Using specialized coatings like graphite and titanium for high-performance components.
- PVD coatings are used in various industries to improve the performance and lifespan of products. Key applications include:
-
Advantages of PVD Coatings:
- PVD coatings offer several benefits over traditional plating methods:
- Enhanced Durability: Products coated with PVD can last up to ten times longer than uncoated ones, with some lasting more than 25 years.
- Environmental Friendliness: PVD is a greener alternative to chrome plating, as it does not produce toxic substances.
- Versatility: The wide range of materials and substrates makes PVD suitable for diverse applications.
- PVD coatings offer several benefits over traditional plating methods:
-
PVD Coating Techniques:
- The two primary techniques used in PVD coating are:
- Evaporation: The coating material is vaporized and then deposited onto the substrate.
- Sputtering: High-speed ions are used to release atoms from the source material, which are then deposited onto the substrate.
- The two primary techniques used in PVD coating are:
-
Specialized PVD Coatings:
- For specific applications, unique coatings such as carbides, nitrides, silicides, and borides are used. These coatings are tailored to meet the demanding requirements of industries like aerospace and automotive.
By understanding the materials and techniques involved in PVD coating, purchasers can make informed decisions about the best coatings for their specific needs, ensuring enhanced performance and longevity of their products.
Summary Table:
Material | Properties | Applications |
---|---|---|
Titanium Nitride (TiN) | High hardness, wear resistance, gold-like appearance | Cutting tools, molds, decorative applications |
Chromium Nitride (CrN) | Superior corrosion resistance | Plastic molding dies, medical instruments |
Zirconium Nitride (ZrN) | Golden color, wear resistance | Decorative purposes, wear-resistant coatings |
Diamond-like Carbon (DLC) | Exceptional hardness, low friction | Automotive components, high-performance tools |
Metals (Titanium, Zirconium, Chromium) | Enhanced durability, corrosion resistance | Automotive, aerospace, medical, and tooling industries |
Need the perfect PVD coating for your application? Contact our experts today to find the best solution!