Crucibles are essential tools used in various industries and laboratories for melting, heating, or altering materials at high temperatures. The material used to make a crucible depends on its intended application, the temperature it needs to withstand, and the type of material being processed. Common materials include fused quartz, silicon carbide, boron nitride, platinum, zirconium, and clay. Each material has unique properties that make it suitable for specific uses, such as resistance to thermal shock, durability, thermal insulation, or inertness to prevent contamination.
Key Points Explained:
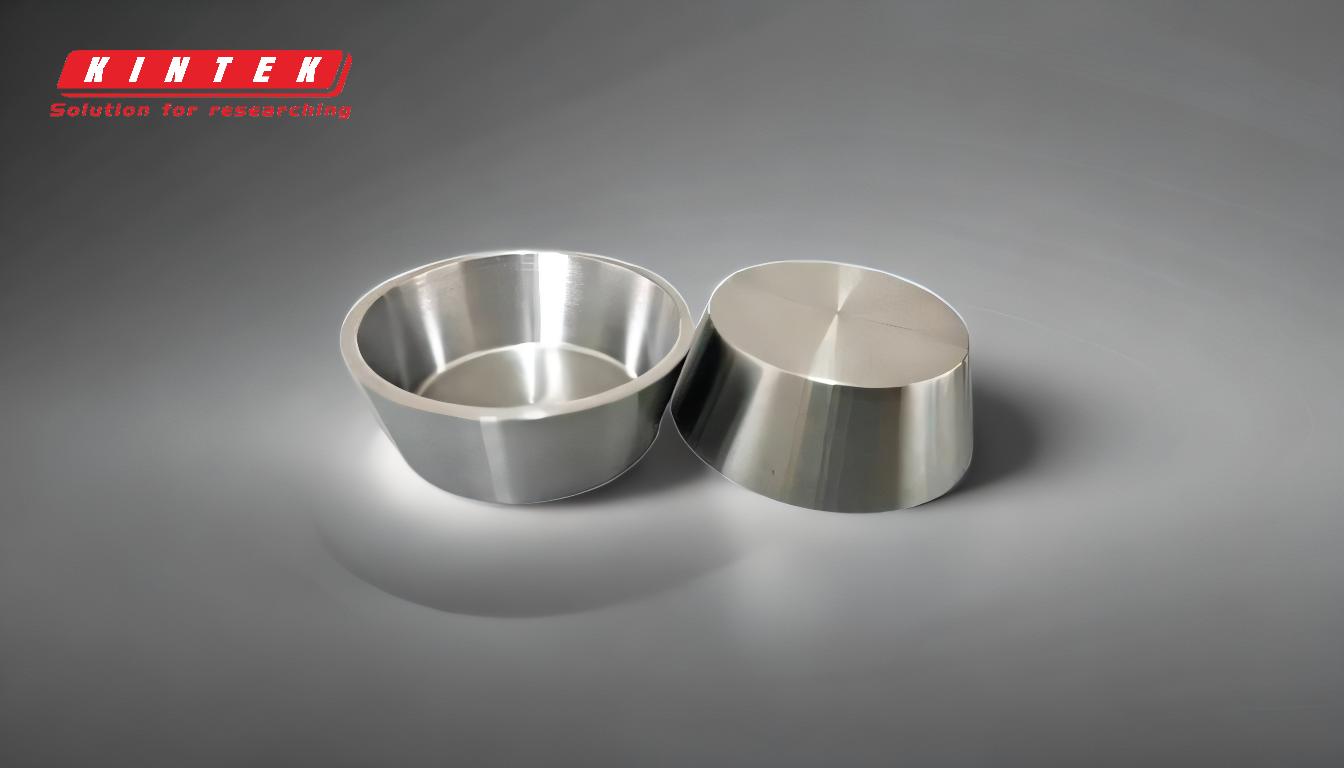
-
Fused Quartz:
- Properties: Fused quartz is highly resistant to thermal shock, meaning it can withstand rapid temperature changes without cracking or breaking. It also has excellent chemical purity and transparency to ultraviolet light.
- Applications: Ideal for melting metals and other high-temperature processes where thermal stability is crucial. It is often used in laboratories and industrial settings for processes like metal casting or glass manufacturing.
-
Silicon Carbide:
- Properties: Silicon carbide is extremely durable, with high thermal conductivity and resistance to wear and corrosion. It can withstand very high temperatures and harsh chemical environments.
- Applications: Commonly used in semiconductor production, where durability and thermal management are critical. It is also used in foundries for melting metals and in high-temperature industrial applications.
-
Boron Nitride:
- Properties: Boron nitride is an excellent thermal insulator with high thermal stability and low thermal expansion. It is also chemically inert and has good lubricating properties.
- Applications: Often used in high-temperature vacuum furnaces and other environments where thermal insulation and chemical inertness are required. It is also used in the production of advanced ceramics and composites.
-
Platinum and Zirconium:
- Properties: Platinum and zirconium are inert materials that resist chemical reactions, making them ideal for use in analytical chemistry. They can withstand high temperatures and are resistant to corrosion.
- Applications: Typically used in laboratory crucibles for sample preparation and analytical chemistry, where contamination must be minimized. These materials ensure the accuracy and reliability of chemical analyses.
-
Clay:
- Properties: Clay is a traditional material that is inexpensive and readily available. It has good thermal resistance and can be shaped easily.
- Applications: Historically used for making crucibles, especially in early metallurgy and pottery. While less common today, clay crucibles are still used in some traditional or low-cost applications.
-
Selection Criteria:
- Temperature Resistance: The material must withstand the specific temperatures required for the application.
- Chemical Compatibility: The crucible material should not react with the substances being processed.
- Thermal Shock Resistance: Important for applications involving rapid temperature changes.
- Durability and Longevity: The material should be durable enough to withstand repeated use without degradation.
- Cost and Availability: The material should be cost-effective and readily available for the intended use.
By understanding these key points, a purchaser can make an informed decision about which crucible material is best suited for their specific needs, whether in a laboratory, industrial, or traditional setting.
Summary Table:
Material | Key Properties | Common Applications |
---|---|---|
Fused Quartz | Thermal shock resistance, chemical purity | Metal casting, glass manufacturing |
Silicon Carbide | High durability, thermal conductivity | Semiconductor production, foundries |
Boron Nitride | Thermal insulation, chemical inertness | High-temperature vacuum furnaces, ceramics |
Platinum/Zirconium | Inert, corrosion-resistant | Analytical chemistry, sample preparation |
Clay | Inexpensive, thermal resistance | Traditional metallurgy, pottery |
Need help choosing the right crucible material? Contact our experts today for personalized advice!