Sintered steel is a versatile material created through the sintering process, which involves compacting metal powders and heating them to bond the particles. The primary materials used in sintered steel include iron and carbon steels, iron-copper and copper steels, and iron-nickel and nickel steels. These materials are chosen for their ability to enhance mechanical properties such as strength, wear resistance, and durability. Sintered steel is widely used in industries like automotive, aerospace, electrical, and biomedical due to its ability to produce complex, high-performance components. The sintering process involves compacting powdered metal into a desired shape and then heating it in a furnace to achieve the final product.
Key Points Explained:
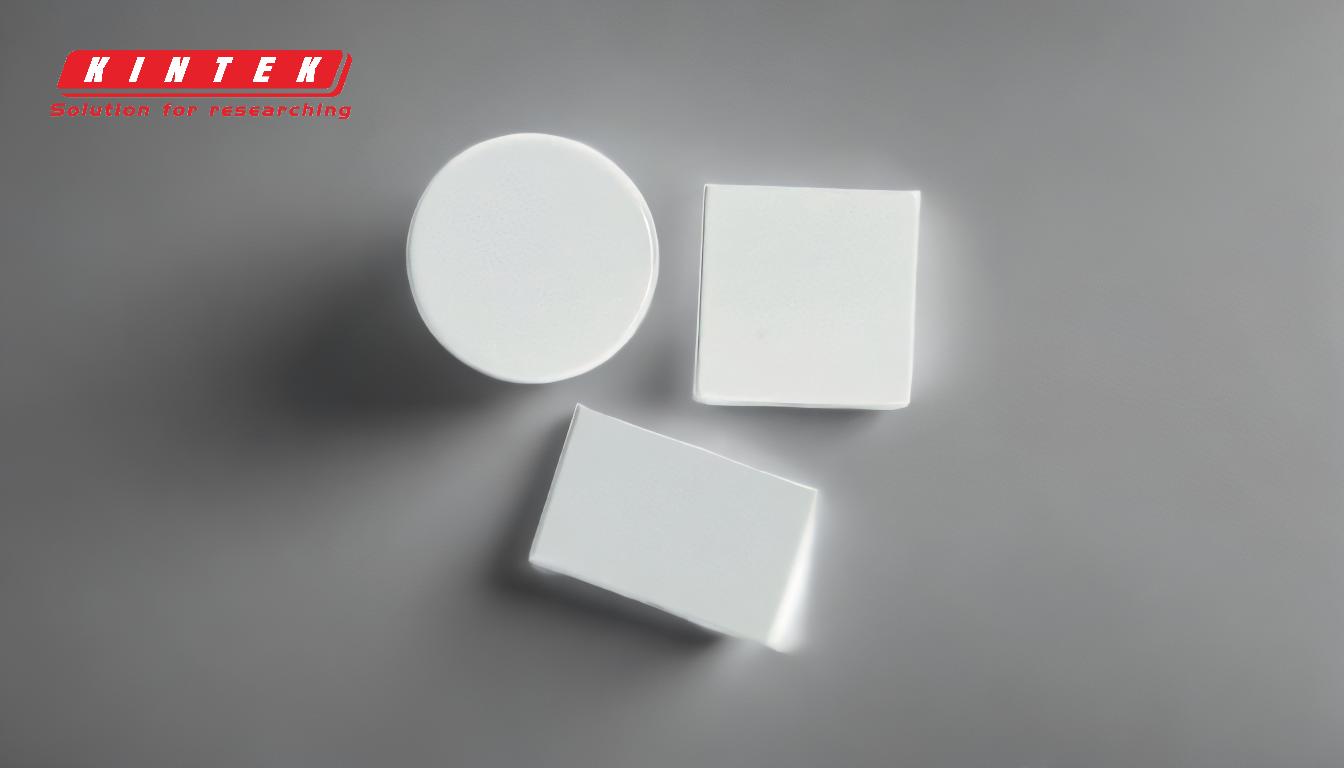
-
Materials Used in Sintered Steel:
- Iron and Carbon Steels: These are the most common materials used in sintering. The addition of carbon improves hardness and strength, making them ideal for high-stress applications.
- Iron-Copper and Copper Steels: Copper is added to improve thermal and electrical conductivity, as well as corrosion resistance. These materials are often used in electrical components and automotive parts.
- Iron-Nickel and Nickel Steels: Nickel enhances toughness and resistance to wear and corrosion, making these steels suitable for aerospace and biomedical applications.
-
Applications of Sintered Steel:
- Automotive Parts: Sintered steel is used to manufacture gears, actuators, and other components that require high strength and durability.
- Electrical Components: Switchgear and other electrical parts benefit from the material's conductivity and precision.
- Cutting Tools: Tools like milling cutters, drills, and reamers are made from sintered steel due to its hardness and wear resistance.
- Aerospace Components: Fuel valve components, actuators, and turbine blades are often made from sintered steel because of its lightweight and high-temperature performance.
- Biomedical Implants: Prosthetic joints and other implants are created using sintered steel for its biocompatibility and strength.
-
Sintering Process:
- Powder Preparation: Metal powders, such as stainless steel, aluminum, nickel, copper, and titanium alloy, are prepared and mixed to achieve the desired properties.
- Compaction: The powder is compacted into a mold or die at high pressure to form the desired shape.
- Sintering: The compacted part is heated in a furnace to a specific temperature, causing the particles to bond and form a solid structure. This step also accounts for slight shrinkage in the final product.
- Post-Processing: Additional treatments, such as machining or coating, may be applied to achieve the final specifications.
-
Advantages of Sintered Steel:
- Complex Shapes: The sintering process allows for the production of intricate shapes that are difficult to achieve with traditional manufacturing methods.
- Material Efficiency: Sintering minimizes material waste, as the powder can be reused or recycled.
- Enhanced Properties: The process improves mechanical properties like strength, wear resistance, and durability, making sintered steel suitable for demanding applications.
-
Future Trends:
- Additive Manufacturing: Advances in sintering technologies are making it compatible with additive manufacturing, enabling the production of complex, custom parts with high precision.
- Material Innovation: Ongoing research is focused on developing new alloys and improving existing materials to expand the applications of sintered steel.
By understanding the materials, processes, and applications of sintered steel, manufacturers and purchasers can make informed decisions about its use in various industries.
Summary Table:
Material Type | Key Properties | Common Applications |
---|---|---|
Iron and Carbon Steels | High hardness, strength, wear resistance | Automotive parts, cutting tools, high-stress components |
Iron-Copper Steels | Improved thermal/electrical conductivity, corrosion resistance | Electrical components, automotive parts |
Iron-Nickel Steels | Enhanced toughness, wear resistance, and corrosion resistance | Aerospace components, biomedical implants |
Interested in learning more about sintered steel materials? Contact our experts today for tailored solutions!