Chemical Vapor Deposition (CVD) is a versatile technique used to deposit thin films of various materials onto substrates. The materials used in CVD include a wide range of precursors such as halides, hydrides, metal alkoxides, metal dialkylamides, metal diketonates, metal carbonyls, and organometallics. These precursors are chosen based on the desired film properties and the specific application. CVD can deposit metal films, non-metal films, multi-component alloy films, and ceramic or compound layers. The process is carried out at normal pressure or low vacuum, allowing for good diffraction properties and even coating of complex shapes. Despite its advantages, CVD faces challenges such as high reaction temperatures and the use of toxic chemicals, which require careful handling and disposal.
Key Points Explained:
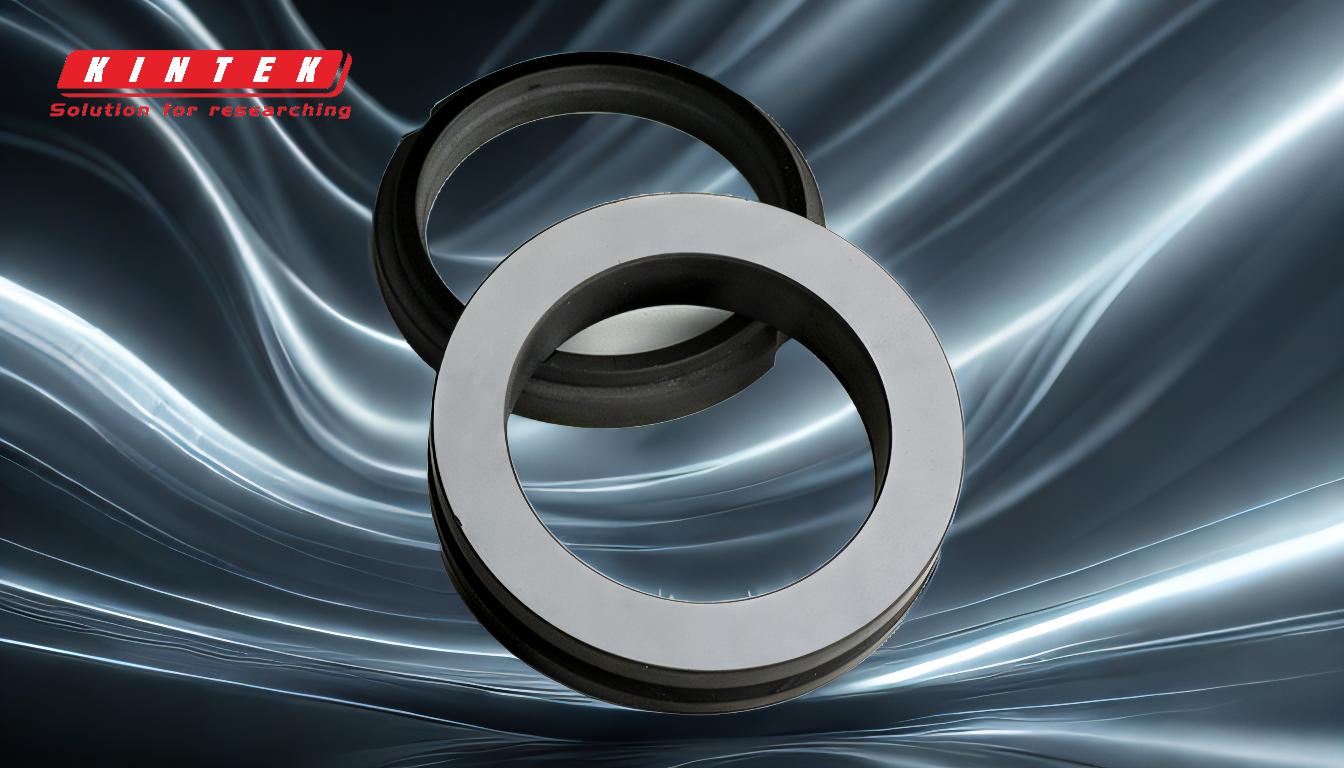
-
Types of Precursors Used in CVD:
- Halides: Examples include HSiCl3, SiCl2, TiCl4, and WF6. These compounds are often used due to their high reactivity and ability to form stable films.
- Hydrides: Examples include AlH(NMe3)3, SiH4, GeH4, and NH3. Hydrides are commonly used for depositing films of elements like silicon and germanium.
- Metal Alkoxides: Examples include TEOS (Tetraethyl Orthosilicate) and TDMAT (Tetrakis(dimethylamido)titanium). These precursors are used for depositing oxide films.
- Metal Dialkylamides: An example is Ti(NMe2), which is used for depositing titanium-based films.
- Metal Diketonates: An example is Cu(acac) (Copper(II) acetylacetonate), used for depositing copper films.
- Metal Carbonyls: An example is Ni(CO) (Nickel tetracarbonyl), used for depositing nickel films.
- Organometallics: Examples include AlMe3 (Trimethylaluminum) and Ti(CH2tBu) (Titanium tert-butyl). These are used for depositing films of metals like aluminum and titanium.
- Oxygen: Often used as a reactant gas to form oxide films.
-
Materials Deposited by CVD:
- Metal Films: CVD can deposit films of metals such as aluminum, titanium, and nickel.
- Non-Metal Films: Films of non-metals like silicon and germanium can also be deposited.
- Multi-Component Alloy Films: CVD is capable of depositing complex alloys with precise control over composition.
- Ceramic or Compound Layers: CVD can deposit ceramic materials like silicon carbide (SiC) and compound layers such as silicon nitride (Si3N4).
-
Process Characteristics:
- Reaction Conditions: CVD reactions are typically carried out at normal pressure or low vacuum, which allows for good diffraction properties and even coating of complex shapes.
- Film Properties: CVD can produce thin film coatings with high purity, good density, small residual stress, and good crystallization.
- Temperature Control: The film growth temperature is much lower than the melting point of the film material, which is crucial for depositing semiconductor film layers.
- Control Over Film Properties: The chemical composition, morphology, crystal structure, and grain size of the coating can be controlled by adjusting deposition parameters.
-
Challenges and Considerations:
- High Reaction Temperatures: CVD typically requires high temperatures (850-1100°C), which can be a limitation for some substrates. Techniques like plasma or laser-assisted CVD can mitigate this issue.
- Use of Toxic Chemicals: Many CVD precursors are toxic, requiring safe handling and disposal methods to protect workers and the environment.
- Post-Coating Finishing: CVD coatings often require post-coating finishing processes, such as heat treating for steel or additional surface treatments to achieve the desired properties.
-
Applications and Advantages:
- Versatility: CVD can coat virtually any surface, making it suitable for a wide range of applications, from semiconductor manufacturing to protective coatings.
- Chemical and Metallurgical Bond: The coatings formed by CVD create a strong chemical and metallurgical bond with the substrate.
- Thickness Control: CVD coatings typically have an average thickness between .0002 and .0005 inches, providing precise control over the film thickness.
In summary, CVD is a highly versatile deposition technique that uses a variety of precursors to deposit thin films of metals, non-metals, alloys, and ceramics. The process offers excellent control over film properties but requires careful handling of toxic chemicals and high-temperature conditions.
Summary Table:
Category | Examples |
---|---|
Halides | HSiCl3, SiCl2, TiCl4, WF6 |
Hydrides | AlH(NMe3)3, SiH4, GeH4, NH3 |
Metal Alkoxides | TEOS, TDMAT |
Metal Dialkylamides | Ti(NMe2) |
Metal Diketonates | Cu(acac) |
Metal Carbonyls | Ni(CO) |
Organometallics | AlMe3, Ti(CH2tBu) |
Reactant Gases | Oxygen |
Materials Deposited | Metal films, non-metal films, multi-component alloys, ceramics, compounds |
Learn more about CVD materials and applications—contact our experts today!