Chemical Vapor Deposition (CVD) is a versatile and widely used technique for creating high-quality coatings and materials. It is employed across various industries, including electronics, optoelectronics, catalysis, and energy applications. The materials used in CVD coatings depend on the specific application and desired properties. Common materials include titanium nitride (TiN), titanium carbon nitride (TiCN), and chromium nitride (CrN), which are often used for tooling protection due to their hardness and low friction. Additionally, CVD is used to produce synthetic diamonds, graphene, and other advanced materials by depositing carbon or other elements onto a substrate. The process involves the decomposition of precursors to form the desired material, making it suitable for a wide range of applications.
Key Points Explained:
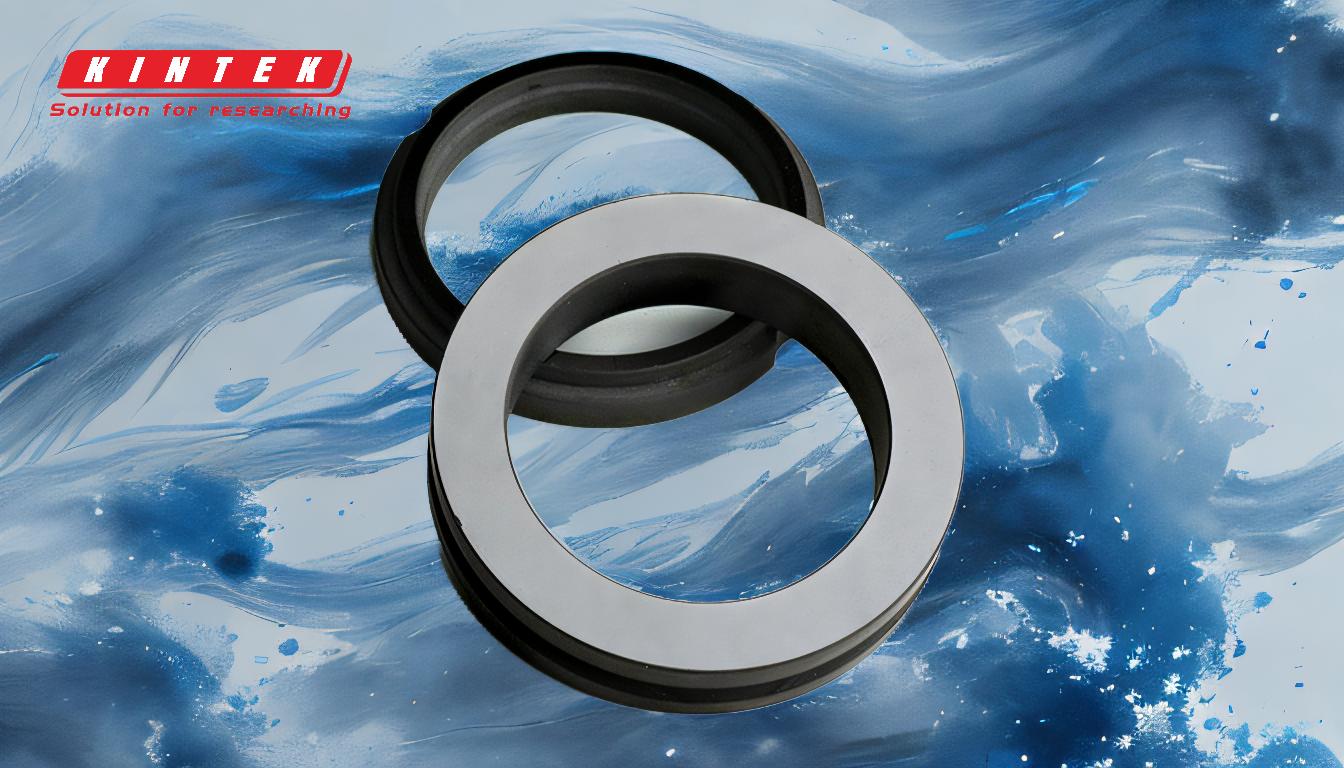
-
Applications of CVD Coatings:
- CVD is widely used in industries such as electronics, optoelectronics, catalysis, and energy. For example, it is essential in semiconductor manufacturing, silicon wafer preparation, and the production of printable solar cells.
- It is also used in machine tools, medical devices, and automotive tools, where protective coatings are required to enhance durability and performance.
-
Common Materials Used in CVD Coatings:
- Titanium Nitride (TiN): Known for its hardness and golden color, TiN is commonly used for tooling protection and decorative purposes.
- Titanium Carbon Nitride (TiCN): Offers a combination of hardness and low friction, making it suitable for cutting tools and wear-resistant coatings.
- Chromium Nitride (CrN): Provides excellent corrosion resistance and is often used in applications requiring high wear resistance.
- Other Transition Metal Carbon Nitrides: Materials like hafnium or vanadium carbon nitrides are also used, offering unique combinations of hardness and low friction.
-
CVD for Advanced Materials:
- Synthetic Diamonds: CVD is used to produce synthetic diamonds by depositing carbon atoms onto a substrate, creating a diamond layer. This is particularly useful in industrial applications where diamond's hardness and thermal conductivity are required.
- Graphene: CVD is a key method for growing graphene, where carbon precursors decompose on a catalyst surface to form graphene layers. This material is crucial in electronics and energy storage applications.
-
CVD Process and Precursors:
- The CVD process involves the adsorption of precursors (e.g., carbon-containing gases) onto a substrate or catalyst surface. These precursors decompose to form the desired material, such as carbon for graphene or diamond growth.
- The choice of precursor and substrate depends on the material being deposited and the specific application. For example, methane (CH₄) is commonly used as a carbon precursor for graphene growth.
-
Advantages of CVD Coatings:
- CVD coatings provide high-quality, uniform layers with excellent adhesion to the substrate.
- They can be tailored to achieve specific properties, such as hardness, wear resistance, or electrical conductivity, making them suitable for a wide range of applications.
In summary, CVD coatings utilize a variety of materials, including TiN, TiCN, CrN, and synthetic diamonds, to meet the demands of different industries. The process's versatility and ability to produce high-performance materials make it a cornerstone of modern manufacturing and technology.
Summary Table:
Material | Properties | Applications |
---|---|---|
Titanium Nitride (TiN) | Hardness, golden color | Tooling protection, decorative purposes |
Titanium Carbon Nitride (TiCN) | Hardness, low friction | Cutting tools, wear-resistant coatings |
Chromium Nitride (CrN) | Corrosion resistance, wear resistance | High wear resistance applications |
Synthetic Diamonds | Hardness, thermal conductivity | Industrial applications |
Graphene | Electrical conductivity, energy storage | Electronics, energy storage |
Want to explore how CVD coatings can enhance your applications? Contact us today for expert guidance!