Sintering is a versatile manufacturing process that involves the bonding of particles through heat and pressure, without reaching the melting point of the material. This technique is widely used across various industries to produce components with enhanced mechanical properties, precise shapes, and consistent quality. The materials suitable for sintering include metals, ceramics, and polymers, each selected based on their specific properties and intended applications. Metal sintering often involves materials like stainless steel, aluminum, nickel, copper, titanium alloy, brass, bronze, and iron-based alloys. Ceramic sintering utilizes materials such as aluminum oxide, zirconium oxide, silicon dioxide, and iron oxide, often requiring organic additives for processing. Polymers are also sintered for applications like rapid prototyping and filter manufacturing. The sintering process involves key steps such as powder preparation, compaction, controlled heating, and cooling, ensuring the final product achieves the desired density and structural integrity.
Key Points Explained:
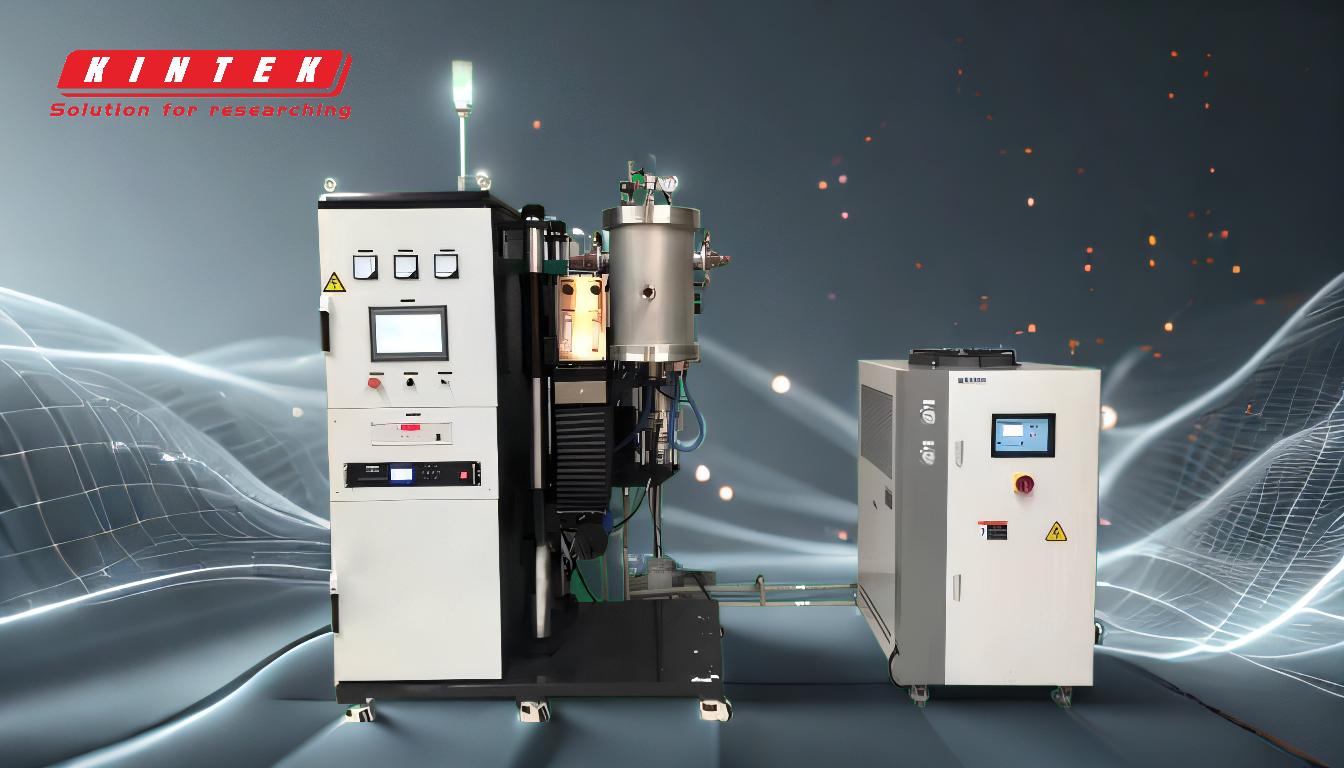
-
Materials Used in Sintering:
- Metals: Commonly sintered metals include stainless steel, aluminum, nickel, copper, titanium alloy, brass, bronze, and iron-based alloys like iron-copper, iron-nickel, and carbon steels. These materials are chosen for their strength, durability, and suitability for additive manufacturing.
- Ceramics: Ceramic materials such as aluminum oxide, zirconium oxide, silicon dioxide, magnesium oxide, lime, beryllium oxide, and iron oxide are used in sintering. These materials are ideal for high-temperature applications and often require organic additives during the pre-sintering stage to improve processing.
- Polymers: Polymers are sintered for applications like rapid prototyping and filter manufacturing. They offer flexibility and ease of shaping, making them suitable for specialized industrial uses.
-
Sintering Process Steps:
- Composition: The raw material, usually in powder form, is mixed with coupling agents or additives to ensure uniformity and improve bonding during sintering.
- Compaction: The powder is compressed under high pressure to form the desired shape, eliminating voids and ensuring structural integrity.
- Heating: The compacted material is heated in a sintering furnace to a specific temperature, below its melting point, to facilitate particle bonding through diffusion and neck formation.
- Cooling: After heating, the sintered product is cooled to solidify into a rigid and cohesive structure, accounting for slight shrinkage during the process.
-
Applications of Sintered Materials:
- Metals: Used for manufacturing small components like gears, pulleys, and other precision parts in industries such as automotive, aerospace, and machinery.
- Ceramics: Ideal for high-temperature components like gears, bearings, and insulating materials in industries requiring thermal and chemical resistance.
- Polymers: Employed in rapid prototyping, filter manufacturing, and other applications where lightweight and customizable materials are needed.
-
Advantages of Sintering:
- Precision and Consistency: Sintering allows for greater control over the manufacturing process, resulting in products with consistent dimensions and properties.
- Material Efficiency: The process minimizes material waste, as powders can be reused or recycled.
- Enhanced Properties: Sintered materials often exhibit improved mechanical properties, such as increased strength, wear resistance, and thermal stability.
By understanding the materials and processes involved in sintering, manufacturers can select the appropriate materials and techniques to achieve the desired product characteristics, ensuring optimal performance and cost-effectiveness.
Summary Table:
Material Type | Common Materials | Key Properties | Applications |
---|---|---|---|
Metals | Stainless steel, aluminum, nickel, copper, titanium alloy, brass, bronze, iron-based alloys | Strength, durability, additive manufacturing suitability | Gears, pulleys, precision parts in automotive, aerospace, and machinery |
Ceramics | Aluminum oxide, zirconium oxide, silicon dioxide, magnesium oxide, lime, beryllium oxide, iron oxide | High-temperature resistance, thermal and chemical stability | Gears, bearings, insulating materials |
Polymers | Various polymers | Flexibility, ease of shaping, lightweight | Rapid prototyping, filter manufacturing |
Learn how sintering can transform your manufacturing process—contact our experts today for tailored solutions!