Sintering is a versatile manufacturing process used across various materials, including metals, ceramics, and polymers. For metals, sintering is particularly valuable for producing small, complex components like gears and pulleys. Commonly sintered metals include stainless steel, aluminum, nickel, copper, titanium alloy, brass, and bronze. These materials are chosen for their ability to bond under heat and pressure, resulting in strong, durable products. The sintering process involves compacting powdered metal into a desired shape and then heating it in a furnace, such as a zirconia sintering furnace, to bond the particles without melting them. This method ensures precise control over the final product's properties, making it ideal for applications requiring high mechanical strength and consistency.
Key Points Explained:
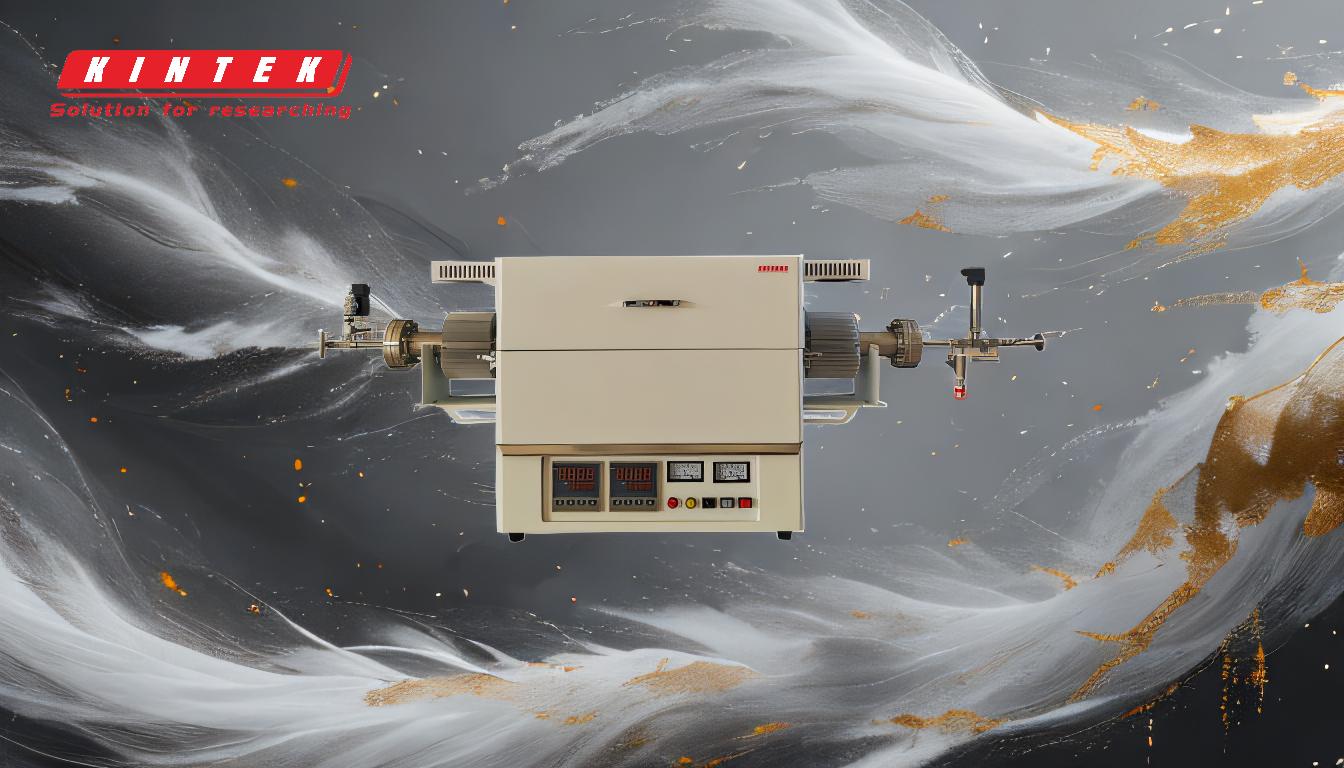
-
Metals Commonly Used in Sintering:
- Stainless Steel: Known for its corrosion resistance and strength, stainless steel is widely used in sintering for components requiring durability.
- Aluminum: Lightweight and versatile, aluminum is sintered for applications in aerospace and automotive industries.
- Nickel: Valued for its high-temperature resistance and magnetic properties, nickel is used in sintering for specialized industrial applications.
- Copper: Excellent electrical conductivity makes copper a preferred choice for sintered electrical components.
- Titanium Alloy: With its high strength-to-weight ratio and biocompatibility, titanium alloy is sintered for medical implants and aerospace parts.
- Brass and Bronze: These alloys are sintered for decorative and functional components due to their aesthetic appeal and mechanical properties.
-
Sintering Process for Metals:
- Powder Preparation: Metal powders are carefully selected and prepared to ensure uniformity and consistency.
- Compaction: The powder is compacted into a mold under high pressure to form the desired shape.
- Sintering: The compacted metal is heated in a furnace, such as a zirconia sintering furnace, to a temperature below its melting point, allowing the particles to bond and form a solid mass.
- Post-Processing: The sintered part may undergo additional treatments, such as machining or coating, to achieve the final specifications.
-
Advantages of Metal Sintering:
- Precision and Consistency: Sintering allows for the production of complex shapes with high dimensional accuracy.
- Material Efficiency: The process minimizes material waste, making it cost-effective.
- Enhanced Properties: Sintered metals exhibit improved mechanical strength, wear resistance, and thermal stability.
-
Applications of Sintered Metals:
- Automotive Industry: Sintered components like gears, bearings, and pulleys are widely used in vehicles.
- Aerospace: Lightweight and strong sintered parts are essential for aircraft and spacecraft.
- Medical Devices: Biocompatible sintered metals, such as titanium alloy, are used for implants and surgical instruments.
- Electronics: Sintered copper components are integral to electrical circuits and connectors.
By understanding the metals used in sintering and the process involved, manufacturers can leverage this technique to produce high-quality, reliable components for a wide range of industries.
Summary Table:
Metal | Key Properties | Applications |
---|---|---|
Stainless Steel | Corrosion resistance, strength | Durable components (gears, bearings) |
Aluminum | Lightweight, versatile | Aerospace, automotive parts |
Nickel | High-temperature resistance, magnetic properties | Industrial applications |
Copper | Excellent electrical conductivity | Electrical components (circuits, connectors) |
Titanium Alloy | High strength-to-weight ratio, biocompatibility | Medical implants, aerospace parts |
Brass and Bronze | Aesthetic appeal, mechanical properties | Decorative and functional components |
Want to learn more about sintering metals for your industry? Contact our experts today!