Extrusion pellets, particularly those used in processes like FTIR (Fourier Transform Infrared Spectroscopy), are typically designed to meet specific size requirements to ensure compatibility with the equipment and optimal performance. The size of these pellets generally falls within a range of 3 mm to 13 mm in diameter, though the exact size can vary depending on the manufacturer and the specific application. This size range ensures that the pellets can be easily handled, processed, and analyzed without causing blockages or inconsistencies in the results.
Key Points Explained:
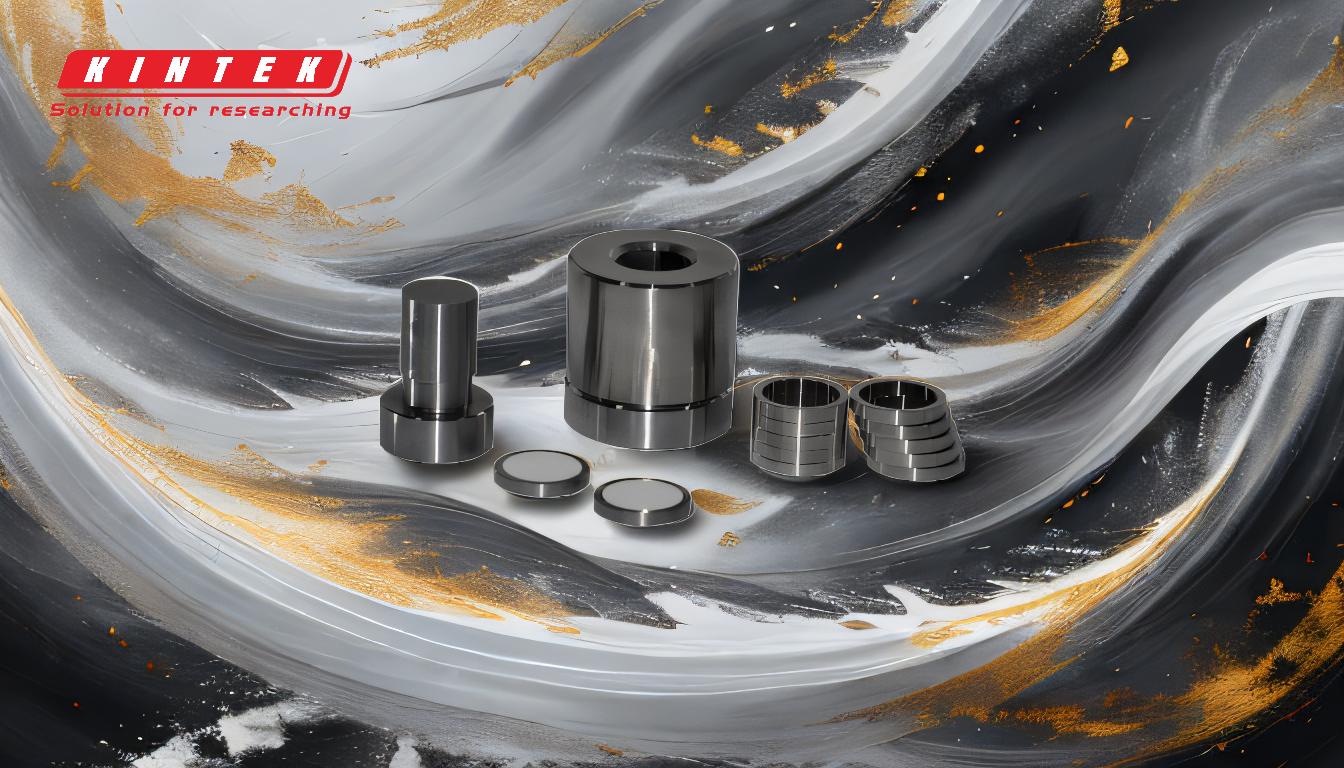
-
Typical Diameter Range of Extrusion Pellets:
- Extrusion pellets, especially those used in FTIR applications, are usually designed to have a diameter ranging from 3 mm to 13 mm. This range is chosen to balance ease of handling and processing with the need for consistent and reliable results in analytical applications.
-
Variability Based on Manufacturer Specifications:
- The exact size of extrusion pellets can vary depending on the manufacturer of the equipment. Different FTIR machines may have specific requirements for pellet size to ensure proper fit and function within the instrument. It is important to consult the equipment manual or manufacturer guidelines to determine the appropriate pellet size for a particular device.
-
Importance of Pellet Size in Analytical Applications:
- The size of extrusion pellets is crucial in analytical applications like FTIR spectroscopy. Pellets that are too large may not fit properly in the sample holder, while those that are too small may not provide a sufficient sample surface for accurate analysis. The 3 mm to 13 mm range is generally considered optimal for ensuring that the pellets are compatible with most FTIR equipment and provide reliable results.
-
Handling and Processing Considerations:
- The size of extrusion pellets also affects their handling and processing. Pellets within the 3 mm to 13 mm range are typically easy to handle, reducing the risk of spillage or loss during sample preparation. Additionally, this size range allows for efficient processing, as the pellets can be easily loaded into the equipment without causing blockages or other issues.
-
Customization for Specific Applications:
- While the 3 mm to 13 mm range is standard, some applications may require customized pellet sizes. For instance, specialized FTIR equipment or unique analytical requirements may necessitate pellets that fall outside this range. In such cases, it is essential to work closely with the equipment manufacturer or a specialized supplier to obtain pellets that meet the specific needs of the application.
In summary, extrusion pellets used in applications like FTIR spectroscopy typically have a diameter range of 3 mm to 13 mm. This size range is chosen to ensure compatibility with most equipment, ease of handling, and reliable analytical results. However, the exact size may vary based on manufacturer specifications and specific application requirements, making it important to consult relevant guidelines or work with specialized suppliers when necessary.
Summary Table:
Key Aspect | Details |
---|---|
Typical Diameter Range | 3 mm to 13 mm |
Variability | Depends on manufacturer and application requirements |
Importance in FTIR | Ensures proper fit, sufficient sample surface, and reliable results |
Handling & Processing | Easy to handle, reduces spillage, and prevents blockages |
Customization | Specialized applications may require pellets outside the standard range |
Need extrusion pellets tailored to your FTIR equipment? Contact us today for expert guidance!