Cold isostatic pressing (CIP) is a powder compaction process performed at ambient (room) temperature, typically ranging between 20°C to 25°C. Unlike hot isostatic pressing (HIP), which involves high temperatures, CIP relies solely on uniform hydraulic pressure applied through a liquid medium to compact powders encased in elastomeric molds. The process leverages Pascal’s law to ensure uniform pressure distribution, resulting in dense and uniform green compacts. These compacts often require subsequent sintering or machining to achieve final product specifications. The temperature during CIP remains constant at ambient levels, making it distinct from other isostatic pressing methods that involve elevated temperatures.
Key Points Explained:
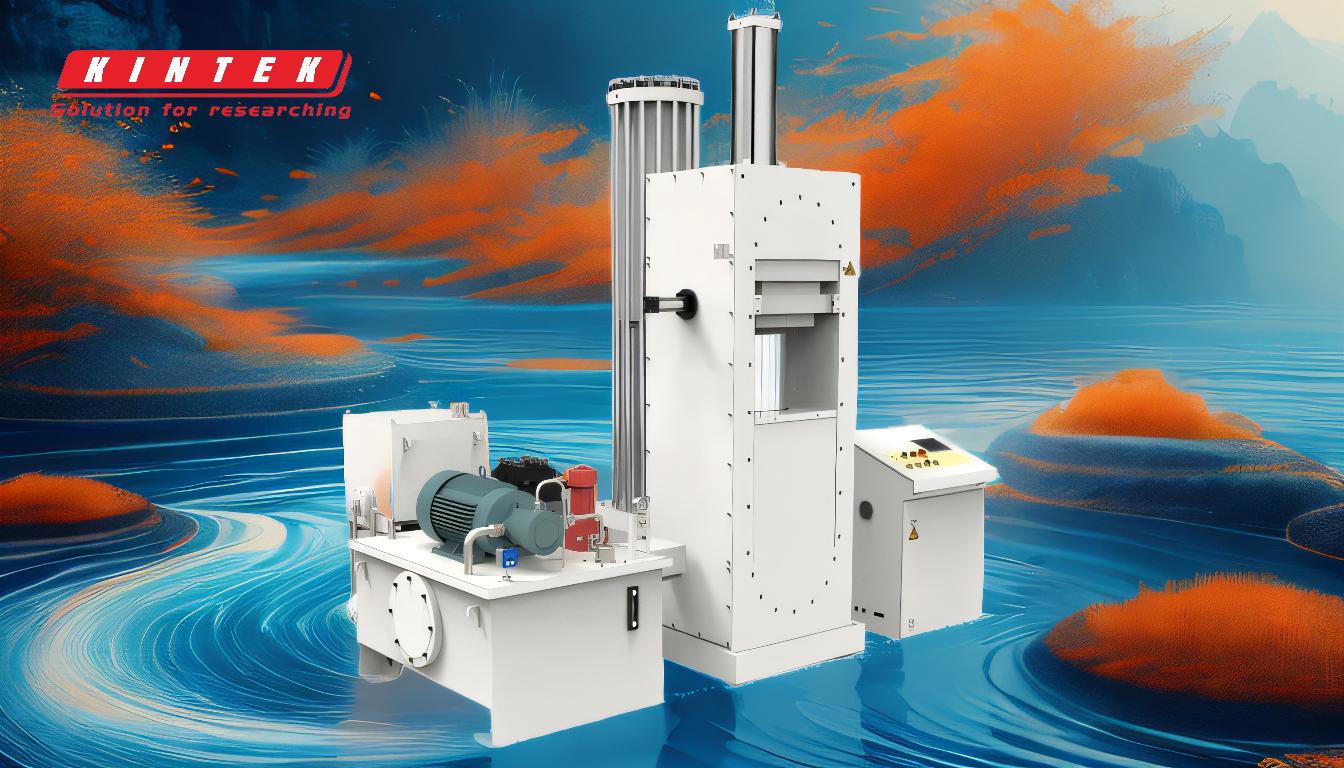
-
Temperature Range in Cold Isostatic Pressing (CIP):
- CIP is performed at ambient (room) temperature, typically between 20°C to 25°C.
- Unlike hot isostatic pressing (HIP), which operates at high temperatures, CIP does not involve any heating of the powder or mold.
- The process relies solely on hydraulic pressure to compact the powder, ensuring the temperature remains stable throughout the process.
-
Pressure Requirements in CIP:
- The pressure applied during CIP ranges from 20 MPa to 400 MPa (approximately 2,900 psi to 58,000 psi).
- Some processes may require pressures as high as 690 MPa (100,000 psi), depending on the material and desired compaction density.
- The pressure is applied uniformly from all directions, ensuring consistent density and mechanical bonding of the powder particles.
-
Process Mechanics and Equipment:
- CIP involves placing a powder-filled elastomeric mold into a pressure chamber filled with a room-temperature liquid, typically water with a corrosion inhibitor.
- Hydraulic pressure is applied uniformly using an external pump, compacting the powder into a solid green body.
- The elastomeric mold allows the liquid pressure to act uniformly on the powder, ensuring isotropic compaction.
-
Advantages of CIP:
- Produces uniform green density, even for complex geometries or large height-to-diameter ratios.
- Suitable for a wide range of materials, including metals, ceramics, and composites.
- Does not require high temperatures, reducing energy consumption and thermal stress on materials.
-
Post-Processing Requirements:
- After CIP, the green compact often requires sintering to achieve final density and mechanical properties.
- Machining may also be necessary to achieve precise dimensions and surface finishes.
-
Comparison with Hot Isostatic Pressing (HIP):
- HIP involves both high pressure and high temperature, typically above 1,000°C, enabling simultaneous compaction and sintering.
- CIP is limited to compaction at ambient temperature, making it a two-step process (compaction followed by sintering).
- CIP is preferred for materials sensitive to high temperatures or those requiring uniform density without thermal distortion.
-
Applications of CIP:
- Widely used in industries such as aerospace, automotive, and medical devices for producing high-performance components.
- Ideal for manufacturing parts with complex shapes, such as turbine blades, prosthetics, and ceramic insulators.
-
Limitations of CIP:
- Requires additional sintering or machining, increasing production time and cost.
- Limited to materials that can be compacted effectively at room temperature.
- Elastomeric molds may wear out over time, requiring replacement and increasing operational costs.
By understanding these key points, equipment and consumable purchasers can make informed decisions about whether CIP is suitable for their specific manufacturing needs, considering factors such as material properties, part geometry, and production requirements.
Summary Table:
Aspect | Details |
---|---|
Temperature Range | 20°C to 25°C (ambient temperature) |
Pressure Range | 20 MPa to 400 MPa (up to 690 MPa for specific materials) |
Process Mechanics | Uniform hydraulic pressure via liquid medium in elastomeric molds |
Advantages | Uniform density, suitable for complex shapes, energy-efficient |
Post-Processing | Sintering and machining often required |
Applications | Aerospace, automotive, medical devices, complex-shaped components |
Limitations | Additional sintering/machining, material limitations, mold wear over time |
Discover how cold isostatic pressing can optimize your manufacturing process—contact us today for expert guidance!