Calcination is a thermal treatment process that requires high temperatures, typically ranging from 800°C to 1300°C, depending on the specific material being processed and the desired outcome. The process is often carried out in specialized reactors called calciners or furnaces, which are designed to withstand and maintain these extreme temperatures. The exact temperature required for calcination can vary based on the material's properties, the chemical reactions involved, and the intended application. Below, we explore the key factors influencing the temperature requirements for calcination and how they apply to different scenarios.
Key Points Explained:
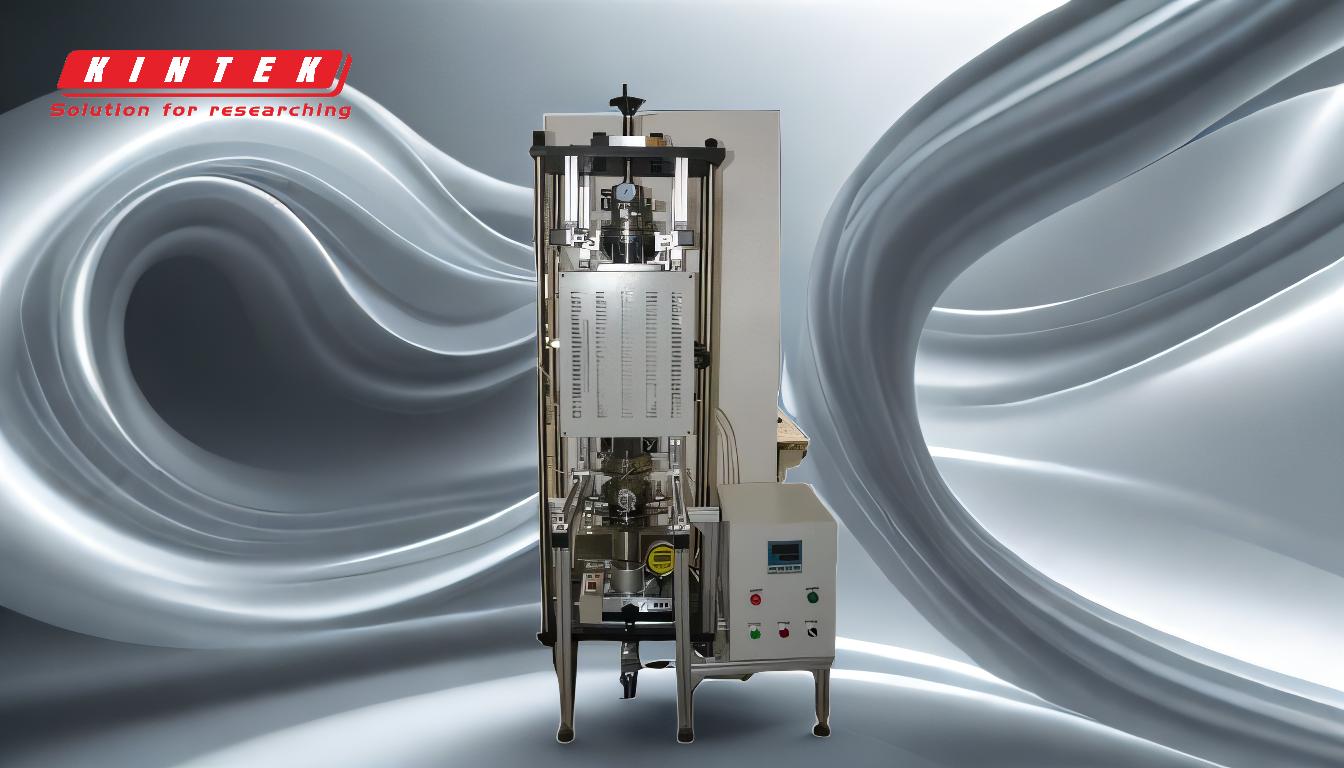
-
Temperature Range for Calcination
- Calcination typically occurs at temperatures between 800°C and 1300°C.
- This range is necessary to drive off volatile components, such as carbon dioxide, water, or other gases, from the material being processed.
- For example, limestone (calcium carbonate) calcines at around 900°C to produce lime (calcium oxide) and carbon dioxide.
-
Dependence on Material Properties
- The specific temperature required depends on the material's chemical composition and thermal stability.
- Limestone: ~900°C
- Gypsum: ~120°C to 180°C (lower than typical calcination, but still considered a calcination process)
- Alumina (Al2O3): ~1200°C
- Materials with higher decomposition temperatures require higher calcination temperatures.
- The specific temperature required depends on the material's chemical composition and thermal stability.
-
Role of the Calciner or Furnace
- Calcination is often performed in a calciner, a cylindrical reactor designed to handle high temperatures and controlled atmospheres.
- Alternatively, furnaces are used when even higher temperatures or specific heating profiles are required.
- These reactors ensure uniform heating and controlled release of gases, which is critical for achieving the desired chemical transformation.
-
Factors Influencing Temperature Selection
- Chemical Reaction Requirements: The temperature must be sufficient to break down the material's chemical bonds without causing unwanted side reactions.
- Energy Efficiency: Higher temperatures increase energy consumption, so the process is optimized to balance efficiency and effectiveness.
- End Product Quality: The temperature must be carefully controlled to ensure the final product meets the required specifications, such as purity or particle size.
-
Applications and Examples
- Cement Production: Limestone calcination at ~900°C is a key step in cement manufacturing.
- Ceramics and Refractories: Calcination of clay or alumina at ~1200°C produces materials with high thermal stability.
- Metal Oxide Production: Calcination is used to produce metal oxides like zinc oxide or titanium dioxide at temperatures up to 1300°C.
-
Environmental Considerations
- Calcination releases carbon dioxide and other gases, which can have environmental impacts.
- Modern calciners and furnaces are designed to capture and manage these emissions, ensuring compliance with environmental regulations.
In summary, the temperature required for calcination varies widely depending on the material and application, but it generally falls within the range of 800°C to 1300°C. Understanding the specific requirements of the material and the process is essential for optimizing calcination and achieving the desired results.
Summary Table:
Key Factor | Details |
---|---|
Temperature Range | 800°C to 1300°C, depending on material and application. |
Material Examples | Limestone: ~900°C, Gypsum: ~120°C–180°C, Alumina: ~1200°C. |
Equipment | Calciners or furnaces designed for high temperatures and controlled atmospheres. |
Applications | Cement production, ceramics, metal oxide production. |
Environmental Considerations | Emissions managed through modern reactor designs. |
Need help optimizing your calcination process? Contact our experts today for tailored solutions!