In the Physical Vapor Deposition (PVD) method, the type of gas required to create plasma depends on the specific application and the desired coating properties. Generally, inert gases like argon are used to generate plasma due to their stability and lack of chemical reactivity with the target material. However, reactive gases such as oxygen, nitrogen, and methane are also used when the goal is to form compound coatings like oxides, nitrides, or carbides. The choice of gas is critical as it influences the plasma generation, the sputtering process, and the final properties of the deposited thin film.
Key Points Explained:
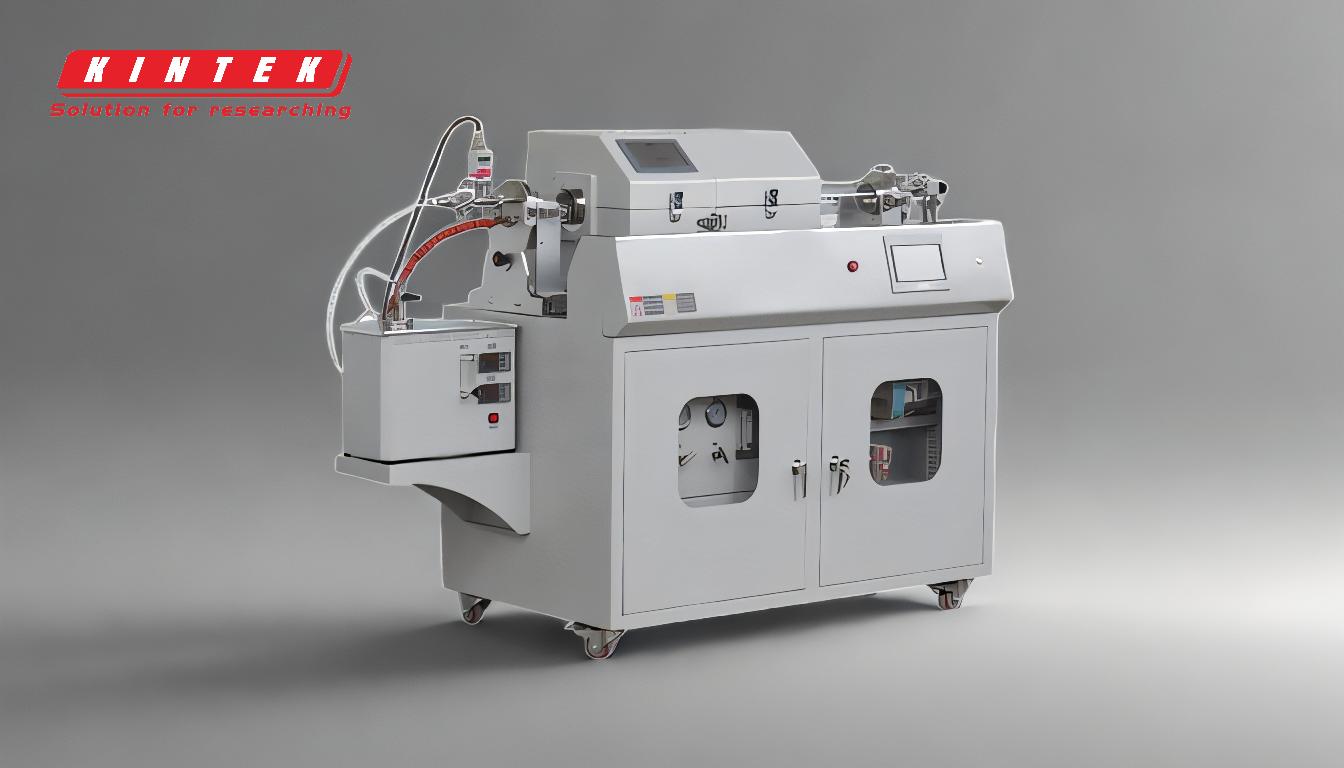
-
Inert Gases in PVD (Argon and Xenon):
- Role in Plasma Generation: Inert gases like argon are commonly used in PVD processes, particularly in sputtering, because they are chemically inert and do not react with the target material. This ensures that the plasma generated is stable and primarily used to dislodge atoms from the target material.
- Why Argon is Preferred: Argon is the most widely used inert gas in PVD due to its atomic weight, which is sufficient to effectively sputter atoms from the target material. It is also cost-effective and readily available.
- Xenon as an Alternative: Xenon, another noble gas, can also be used but is less common due to its higher cost. It is sometimes chosen for specific applications where its heavier atomic weight is advantageous.
-
Reactive Gases in PVD (Oxygen, Nitrogen, Methane):
- Role in Reactive Sputtering: Reactive gases like oxygen, nitrogen, and methane are introduced into the PVD process when the goal is to create compound coatings (e.g., oxides, nitrides, carbides). These gases react with the sputtered metal atoms during the transportation stage, forming the desired compounds on the substrate.
- Oxygen for Oxide Coatings: Oxygen is used to form metal oxide coatings, which are often used for their hardness, wear resistance, and optical properties.
- Nitrogen for Nitride Coatings: Nitrogen is used to create metal nitride coatings, which are known for their high hardness, thermal stability, and corrosion resistance.
- Methane for Carbide Coatings: Methane is used to form metal carbide coatings, which are valued for their extreme hardness and wear resistance.
-
Gas Mixtures and Process Control:
- Combining Inert and Reactive Gases: In some PVD processes, a mixture of inert and reactive gases is used. For example, argon might be used as the primary sputtering gas, while oxygen or nitrogen is introduced in controlled amounts to create specific compound coatings.
- Precision in Gas Flow: The flow rates of these gases are carefully controlled to ensure the desired chemical reactions occur without overwhelming the sputtering process. This precision is crucial for achieving consistent coating properties.
-
Gas Selection Based on Application:
- Optical and Wear-Resistant Coatings: For applications requiring optical coatings or wear-resistant surfaces, oxygen and nitrogen are often used to create oxide and nitride films.
- Hard Coatings for Tools: In the production of hard coatings for cutting tools, methane might be used to form carbide layers that enhance tool life.
- Decorative Coatings: For decorative applications, a combination of gases might be used to achieve specific colors and finishes.
-
Safety and Handling of Gases:
- Safety Considerations: The gases used in PVD, especially reactive gases like methane and oxygen, require careful handling due to their flammability and reactivity. Proper gas storage, delivery systems, and safety protocols are essential.
- Gas Purity: High-purity gases are typically used to avoid contamination of the coatings and to ensure consistent process performance.
In summary, the type of gas required to create plasma in the PVD method depends on the specific application and the desired coating properties. Inert gases like argon are used for their stability and effectiveness in sputtering, while reactive gases like oxygen, nitrogen, and methane are used to form compound coatings. The choice of gas, along with precise control of gas flow and process parameters, is critical to achieving the desired thin film properties.
Summary Table:
Gas Type | Role in PVD | Common Applications |
---|---|---|
Inert Gases | Generate stable plasma, sputter target material without chemical reactions. | General sputtering processes, metal coatings. |
Reactive Gases | Form compound coatings (oxides, nitrides, carbides) during reactive sputtering. | Optical coatings, wear-resistant surfaces, hard coatings for tools, decorative finishes. |
Need help selecting the right gases for your PVD process? Contact our experts today for tailored solutions!