Pyrolysis is a process that breaks down plastic waste into smaller molecules through thermal decomposition in the absence of oxygen. The types of plastics used in pyrolysis are critical to ensure efficiency, safety, and environmental compliance. Commonly used plastics include HDPE, LDPE, PP, and PS, which are found in items like woven bags, packaging, and disposable cups. However, not all plastics are suitable; PVC and PET, for instance, release toxic gases during pyrolysis and should be avoided. The process is versatile and can handle mixed plastic waste, but careful selection is necessary to avoid harmful byproducts and ensure optimal output.
Key Points Explained:
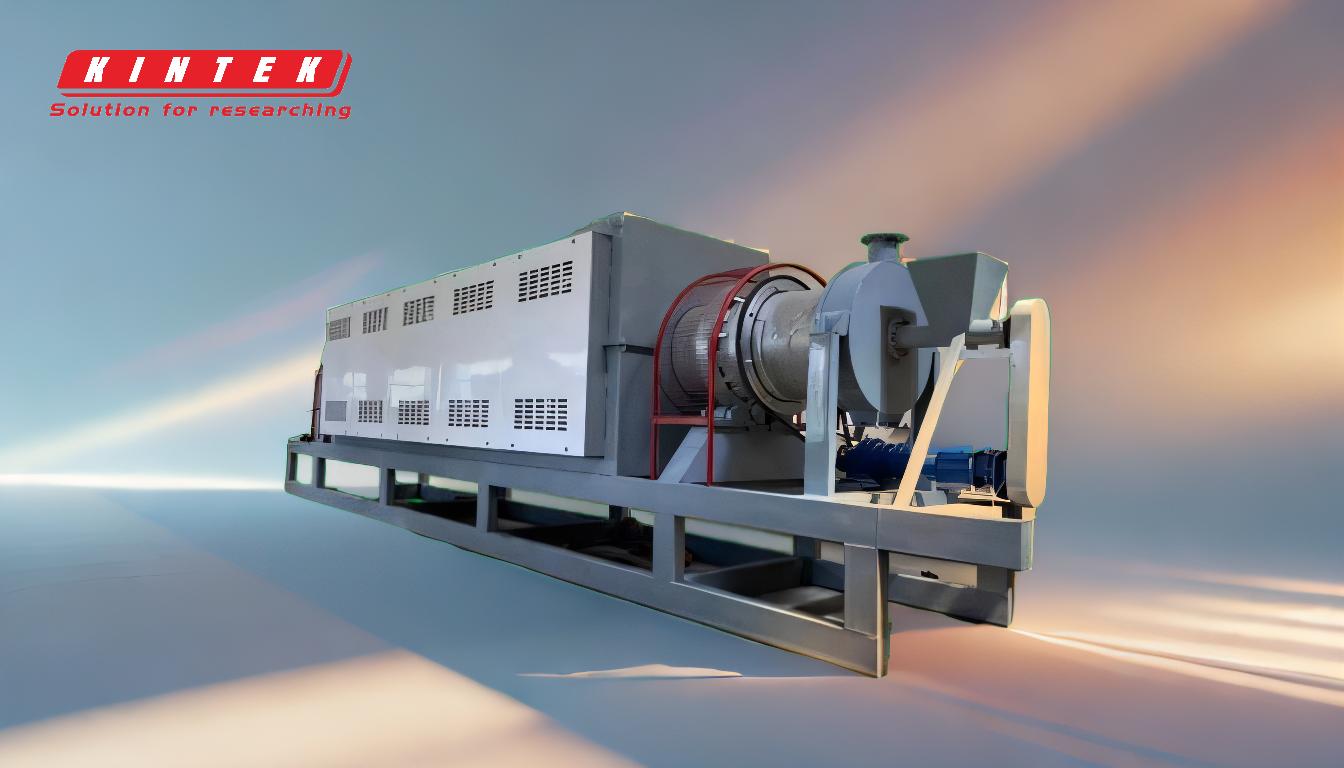
-
Types of Plastics Suitable for Pyrolysis:
- HDPE (High-Density Polyethylene): Commonly found in woven bags, freezer food bags, and packaging. It is a preferred material due to its high yield of useful hydrocarbons during pyrolysis.
- LDPE (Low-Density Polyethylene): Used in items like packaging bags and disposable cups. It is also suitable for pyrolysis, producing valuable oils and gases.
- PP (Polypropylene): Found in items such as cotton swabs and certain packaging materials. It is another plastic that works well in pyrolysis, yielding high-quality outputs.
- PS (Polystyrene): Used in disposable cups and packaging. It can be processed through pyrolysis but requires careful handling due to its lower thermal stability compared to HDPE and LDPE.
-
Plastics Unsuitable for Pyrolysis:
- PVC (Polyvinyl Chloride): Releases toxic chlorine gas and hydrochloric acid during pyrolysis, making it hazardous and unsuitable for the process.
- PET (Polyethylene Terephthalate): Produces harmful byproducts like acetaldehyde and other toxic gases, rendering it inappropriate for pyrolysis.
-
Sources of Plastic Waste for Pyrolysis:
- Post-Consumer Plastics: These are plastics that have been used and discarded by consumers, such as packaging and disposable items.
- Municipal Solid Waste Segregated Plastics: Plastics separated from general waste streams in municipal collection systems.
- Rejects of Mechanical Recycling: Plastics that cannot be processed through traditional mechanical recycling methods due to contamination or mixed compositions.
- Multi-Layer Packaging: Complex packaging materials that are difficult to recycle mechanically but can be broken down through pyrolysis.
- Mixed PET/PVC Contaminated Plastics: While PET and PVC are generally unsuitable, mixed plastics containing these materials can sometimes be processed, though with caution due to the risks of toxic emissions.
-
Material Considerations for Pyrolysis Reactors:
- Reactor Construction: Pyrolysis reactors are typically made from robust materials like Q245R and Q345R boiler plates or 304 and 306 stainless steel to withstand high temperatures and pressures.
- Reactor Thickness: A thickness of 16mm is standard to ensure durability and safety during the pyrolysis process.
-
Versatility of Pyrolysis Beyond Plastics:
- Agricultural and Forestry Waste: Materials like burned trees and high lignin content agricultural by-products can also be processed through pyrolysis, offering a sustainable way to manage waste.
- Co-Feeding Mixed Plastic and Animal Wastes: There is growing interest in combining plastic waste with organic materials like animal waste to enhance the pyrolysis process and produce valuable outputs.
In summary, while pyrolysis is a promising method for recycling certain types of plastics, careful selection of materials is essential to avoid harmful byproducts and ensure the process is both efficient and environmentally friendly.
Summary Table:
Category | Details |
---|---|
Suitable Plastics | HDPE, LDPE, PP, PS |
Unsuitable Plastics | PVC, PET |
Waste Sources | Post-consumer plastics, municipal waste, mechanical recycling rejects, etc. |
Reactor Materials | Q245R, Q345R, 304/306 stainless steel |
Reactor Thickness | 16mm |
Versatility | Handles agricultural, forestry, and mixed plastic waste |
Ready to optimize your pyrolysis process? Contact our experts today for tailored solutions!