Sieve analysis is a widely used method for determining the particle size distribution of granular materials, but it is not without its limitations and potential sources of error. These errors can arise from environmental factors, equipment limitations, material properties, and procedural inconsistencies. Understanding these sources of error is crucial for ensuring accurate and reliable results. Key factors include the impact of ambient conditions like humidity, the limitations of sieve shakers, the resolution of particle size distribution, and the challenges posed by material properties such as static electricity and agglomeration.
Key Points Explained:
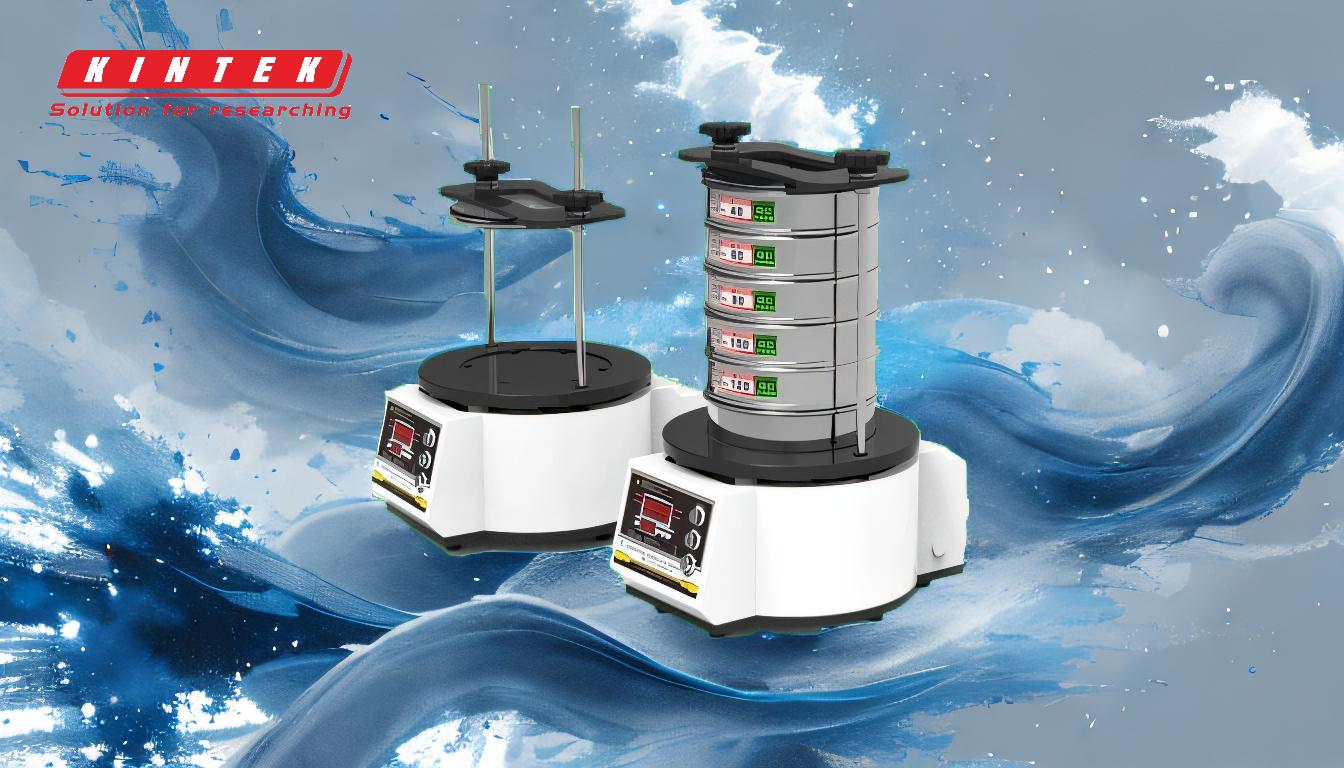
-
Ambient Conditions and Humidity:
- Impact on Accuracy: The reaction of the material to ambient conditions, particularly relative humidity, can significantly affect the accuracy of sieve analysis. Extremely dry conditions can cause fine powders to adhere to the sieve components and each other due to strong electrostatic charges. This adhesion can lead to inaccurate particle size distribution results.
- Mitigation: To minimize this error, it is essential to control the environmental conditions during testing. Maintaining a stable humidity level can help reduce electrostatic charges and prevent particles from clumping together.
-
Limitations of Sieve Shakers:
- Material Characteristics: The effectiveness of a sieve shaker is influenced by the characteristics of the material being tested. Factors such as the minimum size to be separated, resistance to agglomeration, and static electric factors can impact the performance of the sieve shaker.
- Mitigation: Selecting the appropriate sieve shaker for the specific material and ensuring that the shaker operates within its optimal parameters can help mitigate these limitations.
-
Resolution of Particle Size Distribution:
- Limited Number of Sieves: Sieve analysis provides a limited number of size fractions, typically up to 8 sieves. This restriction limits the resolution of the particle size distribution, making it difficult to detect fine gradations in particle size.
- Mitigation: To improve resolution, additional sieves can be used, or alternative methods such as laser diffraction can be employed for more detailed particle size analysis.
-
Minimum Measurement Limit:
- 50 µm Threshold: Sieve analysis has a minimum measurement limit of 50 µm. Particles smaller than this threshold cannot be accurately measured using standard sieves.
- Mitigation: For materials with particles smaller than 50 µm, alternative methods such as sedimentation or laser diffraction should be considered.
-
Time-Consuming Nature:
- Duration of Analysis: Sieve analysis can be time-consuming, especially when dealing with fine powders or materials that require prolonged shaking to achieve accurate separation.
- Mitigation: Optimizing the shaking time and using automated sieve shakers can help reduce the time required for analysis while maintaining accuracy.
-
Static Electricity and Agglomeration:
- Adhesion and Clumping: Fine powders are particularly susceptible to static electricity, which can cause particles to adhere to the sieve components and each other. This adhesion can lead to inaccurate results and clogging of the sieves.
- Mitigation: Using anti-static agents or conducting the analysis in a controlled environment can help reduce the impact of static electricity and prevent particle agglomeration.
-
Dry Particles Requirement:
- Ineffectiveness with Wet Particles: Sieve analysis is only effective with dry particles. Wet or moist particles can clog the sieves and lead to inaccurate results.
- Mitigation: Ensuring that the material is thoroughly dried before analysis is crucial. If the material is inherently wet, alternative methods such as wet sieving or sedimentation should be considered.
By understanding and addressing these potential sources of error, the accuracy and reliability of sieve analysis can be significantly improved. Proper control of environmental conditions, selection of appropriate equipment, and adherence to standardized procedures are essential for obtaining precise particle size distribution data.
Summary Table:
Error Source | Impact | Mitigation |
---|---|---|
Ambient Conditions & Humidity | Affects accuracy due to electrostatic charges and particle clumping. | Control humidity levels to reduce static electricity. |
Limitations of Sieve Shakers | Influenced by material characteristics like agglomeration and static. | Use appropriate sieve shakers and optimize operational parameters. |
Resolution of Particle Size | Limited by the number of sieves (up to 8). | Add more sieves or use laser diffraction for finer resolution. |
Minimum Measurement Limit | Cannot measure particles smaller than 50 µm. | Use sedimentation or laser diffraction for sub-50 µm particles. |
Time-Consuming Nature | Prolonged shaking required for fine powders. | Optimize shaking time or use automated sieve shakers. |
Static Electricity & Agglomeration | Particles adhere to sieves, causing inaccuracies. | Use anti-static agents or conduct tests in controlled environments. |
Dry Particles Requirement | Wet particles clog sieves, leading to inaccurate results. | Dry materials thoroughly or use wet sieving/sedimentation for wet samples. |
Improve your sieve analysis accuracy—contact our experts today for tailored solutions!