Sputtering, as a phenomenon, was first discovered in 1852 by a scientist named Grove (sometimes referred to as Groe). He observed the deposition of metal films using electrical discharges in a cold cathode setup. This marked the initial recognition of the sputtering process, which later evolved into a significant thin-film deposition technique. Over the years, advancements such as the introduction of radio frequency (RF) sputtering and improved vacuum technology expanded its applications, particularly for depositing refractory metals and dielectric materials. The process saw commercial use by the 1930s and regained prominence in the late 1950s and early 1960s due to technological advancements.
Key Points Explained:
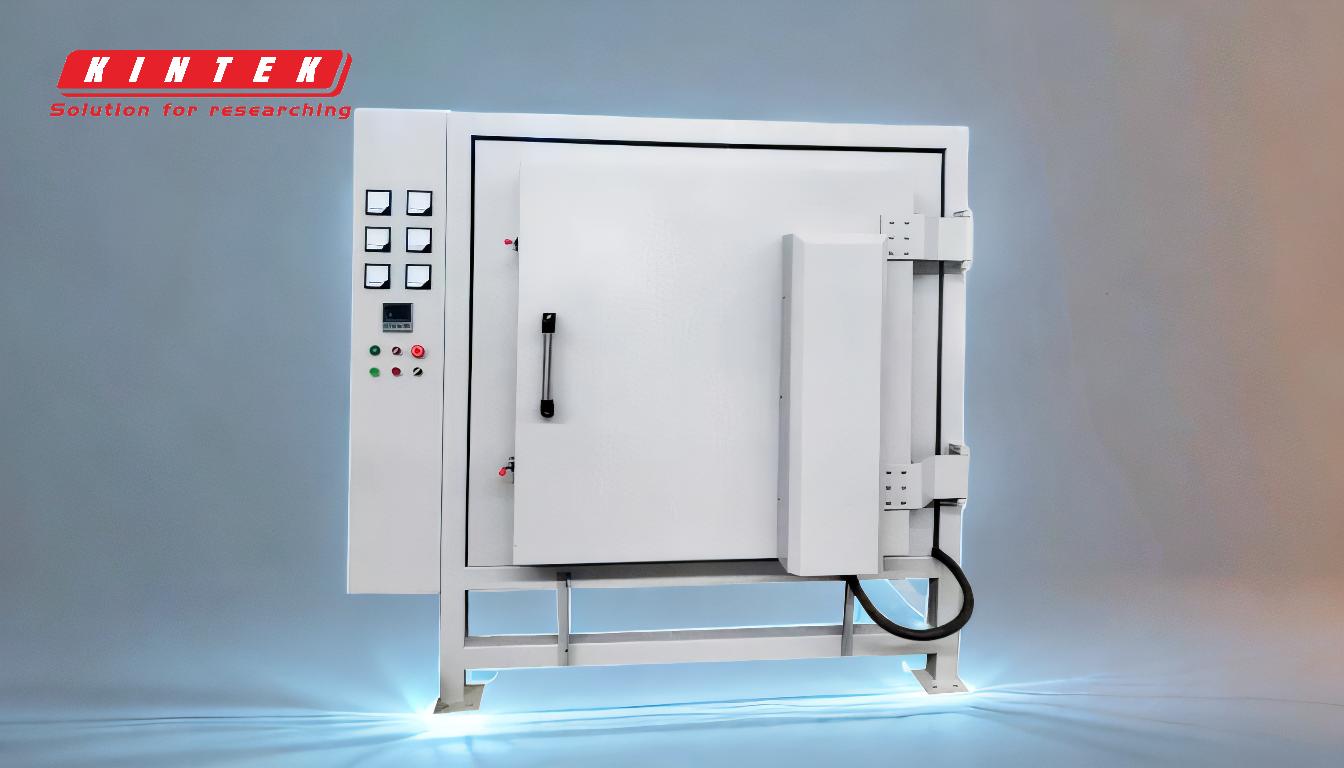
-
Discovery of Sputtering (1852):
- Sputtering was first discovered in 1852 by Grove (or Groe), who used electrical discharges to deposit metal films on a cold cathode.
- This early observation involved the use of direct current glow discharges, which led to the deposition of thin metal films.
- The discovery was significant because it introduced a method to deposit refractory metals, which were difficult to deposit using traditional thermal evaporation techniques.
-
Development as a Thin-Film Deposition Technique (1920):
- The sputtering mechanism was further developed into a practical thin-film deposition technique by Irving Langmuir in 1920.
- Langmuir's work laid the foundation for understanding and optimizing the sputtering process, making it more applicable for industrial and scientific purposes.
- This development marked a transition from a mere scientific observation to a usable technology.
-
Commercial Applications (1930s):
- By the 1930s, sputtering found its first commercial applications.
- The ability to deposit thin films of various materials, including refractory metals, made it valuable for industries requiring precise and durable coatings.
- However, during the 1950s, sputtering was largely replaced by thermal evaporation due to the latter's simplicity and efficiency.
-
Resurgence in the Late 1950s and Early 1960s:
- Sputtering regained interest in the late 1950s and early 1960s due to advancements in vacuum technology.
- Improved vacuum systems allowed for better control over the sputtering environment, enhancing the quality and consistency of deposited films.
- The introduction of DC sputtering enabled the deposition of a wide range of conductive materials, while RF sputtering expanded the technique to include dielectric materials.
-
Introduction of RF Sputtering:
- RF sputtering, which uses radio frequency waves, was a significant advancement that allowed for the deposition of dielectric films.
- This innovation addressed a key limitation of earlier sputtering techniques, which were primarily suited for conductive materials.
- RF sputtering broadened the scope of sputtering applications, making it a versatile tool in materials science and engineering.
-
Modern Sputtering Devices (1970):
- In 1970, Peter J. Clarke introduced the first sputtering device that utilized electron and ion collisions to deposit atom-scale coatings on target surfaces.
- This development represented a leap forward in the precision and control of the sputtering process, enabling the deposition of ultra-thin and highly uniform films.
- Clarke's work contributed to the widespread adoption of sputtering in various high-tech industries, including semiconductors and optics.
-
Historical Context and Evolution:
- Sputtering has undergone significant evolution since its discovery in 1852.
- From its initial use in depositing refractory metals to its modern applications in depositing a wide range of materials, sputtering has proven to be a versatile and valuable technique.
- The process's resurgence in the mid-20th century and subsequent advancements highlight its adaptability and importance in materials science.
By understanding the history and evolution of sputtering, one can appreciate its significance as a thin-film deposition technique and its continued relevance in modern technology.
Summary Table:
Milestone | Year | Key Development |
---|---|---|
Discovery of Sputtering | 1852 | Grove observed metal film deposition using electrical discharges in a cold cathode. |
Development as a Thin-Film Method | 1920 | Irving Langmuir optimized sputtering for industrial and scientific applications. |
Commercial Applications | 1930s | Sputtering used for precise coatings in industries requiring durable materials. |
Resurgence with Vacuum Advances | 1950s-60s | Improved vacuum systems and RF sputtering expanded material compatibility. |
RF Sputtering Introduction | 1960s | Enabled deposition of dielectric films, broadening sputtering applications. |
Modern Sputtering Devices | 1970 | Peter J. Clarke introduced devices for ultra-thin, uniform film deposition. |
Discover how sputtering can enhance your material science projects—contact our experts today!