Rotary kilns are versatile industrial equipment used across a wide range of industries for high-temperature processing of materials. Their ability to achieve uniform temperature distribution, mix particles effectively, and reach extreme temperatures (up to 2273 K) makes them indispensable in industries such as cement, steel, and chemical processing. They are employed for processes like calcination, sintering, reduction, waste incineration, and material recovery. From traditional applications like cement and lime production to specialized uses such as catalyst activation, waste recycling, and soil remediation, rotary kilns play a critical role in modern industrial processes.
Key Points Explained:
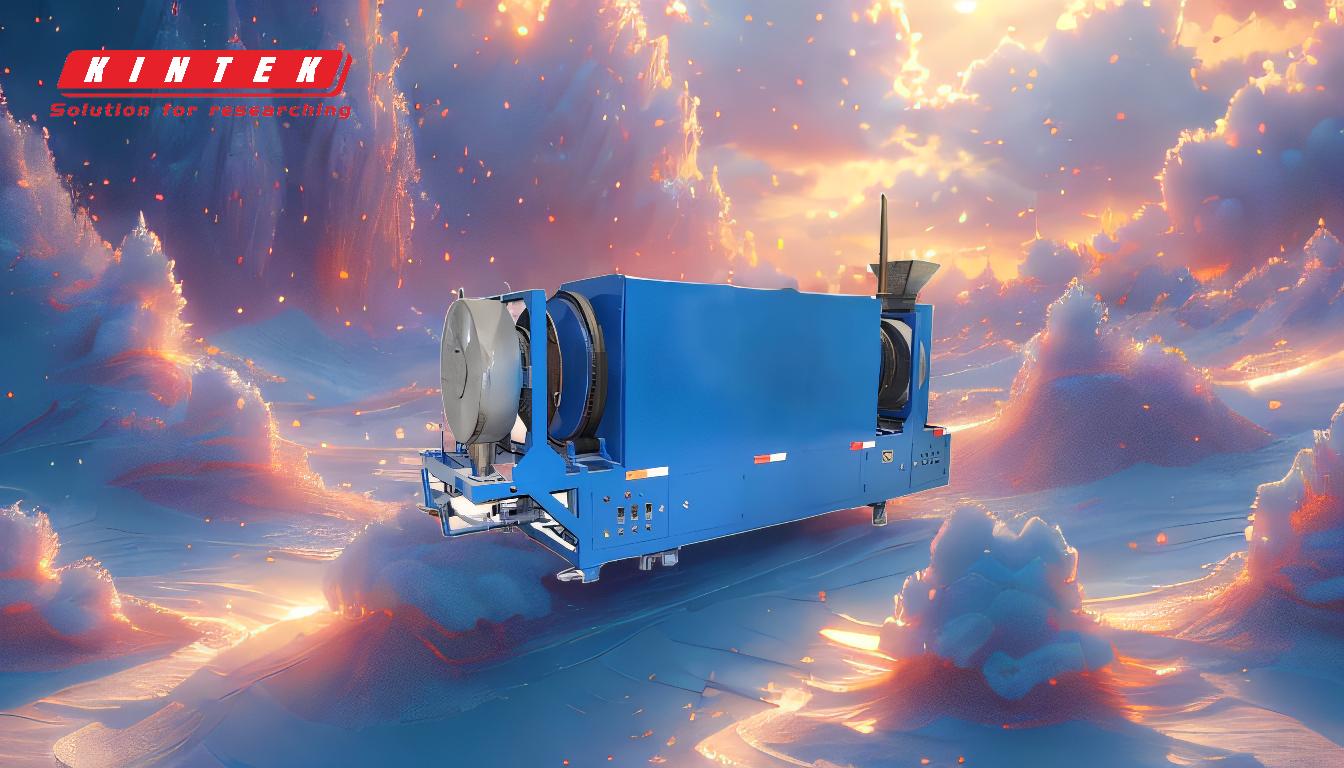
-
Cement and Lime Production:
- Rotary kilns are foundational in the cement industry, where they are used for calcining limestone to produce clinker, a key ingredient in cement.
- They are also used in lime production, where limestone is heated to produce quicklime (calcium oxide).
-
Steel and Iron Industries:
- In the steel industry, rotary kilns are used for reducing iron ore to produce sponge iron, a critical step in steelmaking.
- They are also employed for calcining iron ore pellets, which improves their metallurgical properties for use in blast furnaces.
-
Chemical Processing:
- Rotary kilns are used in the production of TiO2 pigment, mercury, and other chemicals through processes like oxidation, reduction, and volatilization.
- They are also used for processing gypsum into sulphuric acid and cement.
-
Mineral Roasting and Sintering:
- Rotary kilns are used to roast ores, such as ilmenite, to extract valuable metals.
- Sintering processes, such as those for dolomite and magnesite, are also carried out in rotary kilns to produce dense, high-strength materials.
-
Waste Management and Recycling:
- Rotary kilns are widely used for incinerating waste materials, including sewage sludge, scrap tires, and waste wood.
- They are also employed in soil remediation, where they desorb contaminants from soil.
-
Material Recovery and Upgrading:
- Rotary kilns are used to recover waste lime and upgrade phosphate ores.
- They are also used in the regeneration of activated carbon and coal, making them reusable.
-
Specialized Applications:
- Rotary kilns are used in catalyst activation, plastics and ceramics processing, and degasifying lignite.
- They are also employed in the volatilization of metals like zinc, lead, and copper from electric furnace dust.
-
Versatility Across Industries:
- Originally developed for the cement industry, rotary kilns have expanded into diverse applications, becoming essential in both traditional and modern industrial processes.
- Their ability to handle a wide range of materials and processes makes them a backbone of industrial operations.
In summary, rotary kilns are used in industries ranging from cement and steel to waste management and chemical processing. Their ability to achieve high temperatures, ensure uniform heating, and handle diverse materials makes them indispensable for a wide array of industrial applications.
Summary Table:
Industry | Applications |
---|---|
Cement and Lime | Calcining limestone for clinker, producing quicklime |
Steel and Iron | Reducing iron ore to sponge iron, calcining iron ore pellets |
Chemical Processing | Producing TiO2 pigment, mercury, sulphuric acid, and cement |
Mineral Roasting | Roasting ores (e.g., ilmenite), sintering dolomite and magnesite |
Waste Management | Incinerating sewage sludge, scrap tires, waste wood, and soil remediation |
Material Recovery | Recovering waste lime, upgrading phosphate ores, regenerating activated carbon |
Specialized Applications | Catalyst activation, plastics/ceramics processing, volatilizing metals |
Discover how rotary kilns can optimize your industrial processes—contact our experts today!