Muffle furnaces rely on effective insulation materials to maintain high temperatures and minimize heat loss. The primary insulators used in muffle furnaces are ordinary refractory bricks and ceramic fibers (or ceramic wool). These materials are chosen for their excellent thermal insulation properties, durability, and ability to withstand extreme temperatures. Refractory bricks provide structural stability, while ceramic fibers enhance thermal efficiency by reducing heat loss. Additionally, some muffle furnaces may incorporate mineral wool alongside ceramic wool for improved insulation performance. The combination of these materials ensures optimal furnace performance, energy efficiency, and longevity.
Key Points Explained:
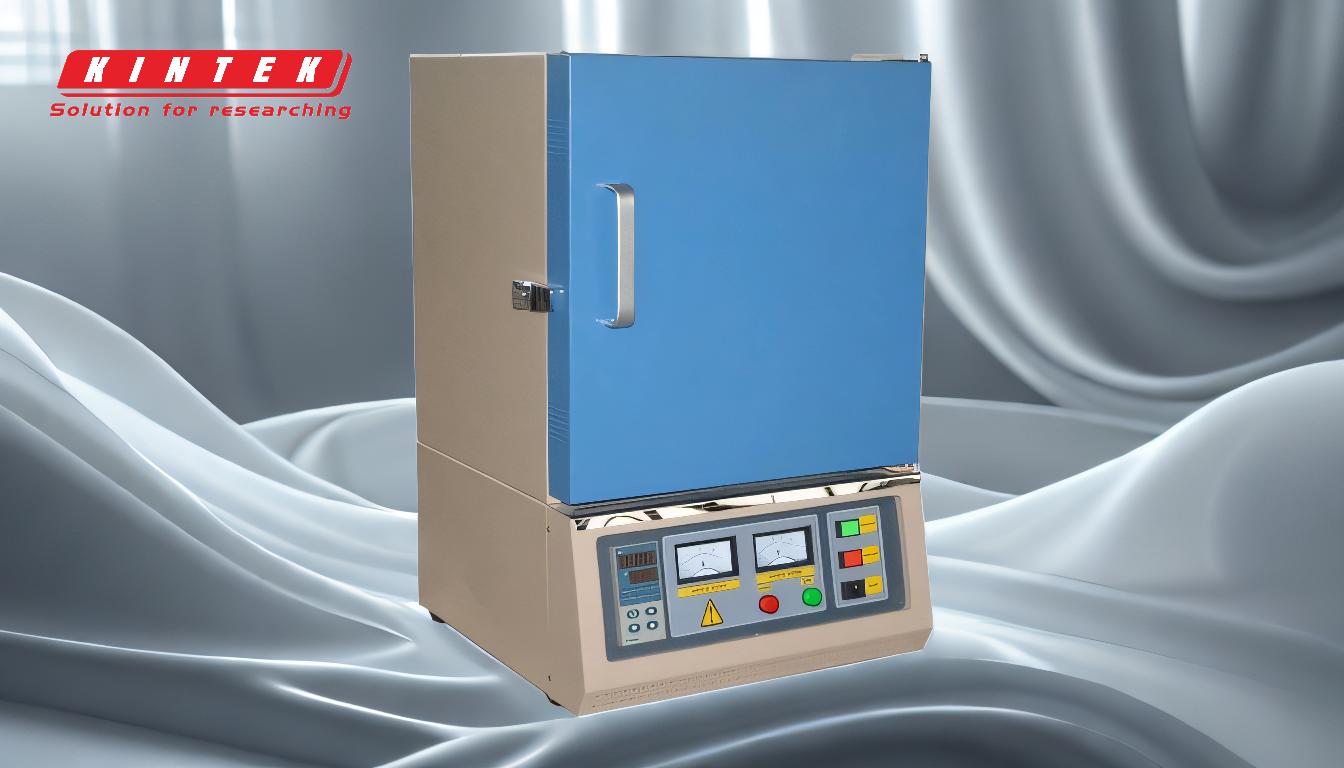
-
Primary Insulation Materials in Muffle Furnaces:
-
Ordinary Refractory Bricks: These are dense, durable materials made from heat-resistant compounds like alumina, silica, and fireclay. They are used to line the interior of the furnace, providing structural support and thermal insulation.
- Advantages: High thermal stability, resistance to thermal shock, and mechanical strength.
- Applications: Ideal for high-temperature environments where structural integrity is critical.
-
Ceramic Fibers (Ceramic Wool): These are lightweight, flexible materials composed of alumina-silica fibers. They are used as additional insulation layers to reduce heat loss and improve energy efficiency.
- Advantages: Excellent thermal insulation, low thermal mass, and ease of installation.
- Applications: Commonly used in modern muffle furnaces to enhance thermal performance.
-
Ordinary Refractory Bricks: These are dense, durable materials made from heat-resistant compounds like alumina, silica, and fireclay. They are used to line the interior of the furnace, providing structural support and thermal insulation.
-
Combination of Insulation Materials:
- Some muffle furnaces use a combination of ceramic wool and mineral wool for improved insulation. Mineral wool, made from molten rock or slag, complements ceramic fibers by providing additional thermal resistance and reducing heat loss.
- Advantages: Enhanced thermal insulation, cost-effectiveness, and versatility.
- Applications: Suitable for furnaces requiring higher energy efficiency and lower operating costs.
- Some muffle furnaces use a combination of ceramic wool and mineral wool for improved insulation. Mineral wool, made from molten rock or slag, complements ceramic fibers by providing additional thermal resistance and reducing heat loss.
-
Why These Materials Are Chosen:
- Thermal Efficiency: Both refractory bricks and ceramic fibers have low thermal conductivity, which minimizes heat transfer and ensures the furnace retains heat effectively.
- Durability: These materials can withstand extreme temperatures (up to 1700°C or higher) without degrading, ensuring long-term reliability.
- Energy Savings: By reducing heat loss, these insulators contribute to lower energy consumption and operational costs.
-
Considerations for Purchasers:
- When selecting a muffle furnace, it is essential to evaluate the type and quality of insulation materials used. High-quality refractory bricks and ceramic fibers ensure better performance and longevity.
- For applications requiring frequent temperature changes, ceramic fibers are preferable due to their low thermal mass, which allows for faster heating and cooling cycles.
- For heavy-duty applications, refractory bricks provide the necessary structural support and thermal stability.
-
Comparison of Insulation Materials:
-
Refractory Bricks:
- Pros: High durability, excellent thermal stability, and mechanical strength.
- Cons: Heavier and bulkier, which may increase the overall weight of the furnace.
-
Ceramic Fibers:
- Pros: Lightweight, superior thermal insulation, and flexibility.
- Cons: Less structural support compared to refractory bricks.
-
Refractory Bricks:
By understanding these key points, purchasers can make informed decisions when selecting a muffle furnace, ensuring it meets their specific thermal and operational requirements.
Summary Table:
Material | Advantages | Applications |
---|---|---|
Refractory Bricks | High thermal stability, resistance to thermal shock, mechanical strength | High-temperature environments requiring structural integrity |
Ceramic Fibers | Lightweight, excellent thermal insulation, low thermal mass, easy installation | Modern muffle furnaces for enhanced thermal performance |
Mineral Wool | Enhanced insulation, cost-effectiveness, versatility | Furnaces requiring higher energy efficiency and lower operating costs |
Need help choosing the right insulation materials for your muffle furnace? Contact our experts today for personalized advice!