Pyrolysis and gasification are both thermal conversion processes used to transform organic materials into useful products, but they differ significantly in their operating conditions, chemical reactions, and end products. Pyrolysis occurs in the absence of oxygen, producing bio-oil, bio-char, and syngas, while gasification involves partial oxidation with limited oxygen, primarily yielding syngas. The choice between the two depends on the desired end products, energy efficiency, environmental impact, and specific applications. Pyrolysis is better suited for producing liquid fuels and soil amendments, whereas gasification is more efficient for generating syngas for energy or chemical synthesis. Both processes have unique advantages and limitations, making them suitable for different industrial and environmental contexts.
Key Points Explained:
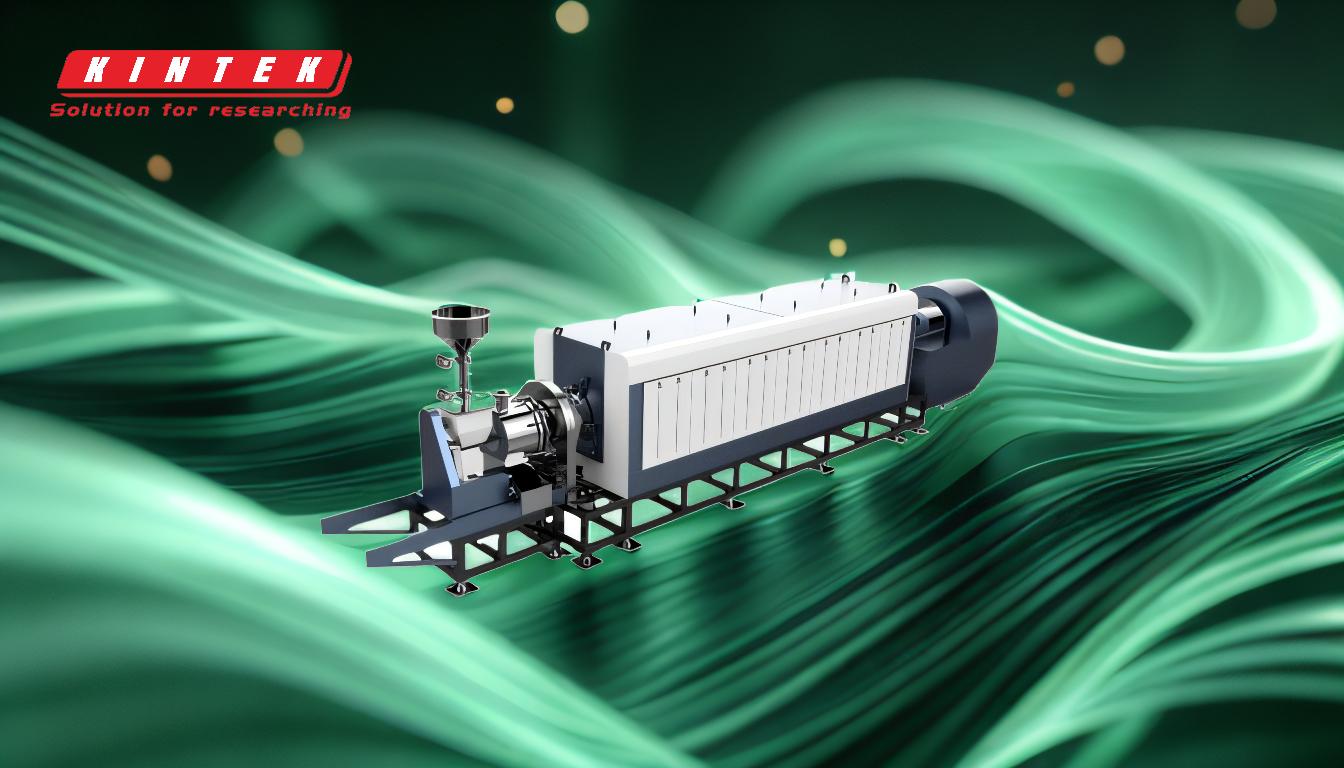
-
Process Conditions and Chemical Reactions:
- Pyrolysis: Occurs in the absence of oxygen, leading to thermal decomposition of organic materials. This process produces bio-oil, bio-char, and syngas. The absence of oxygen prevents combustion and allows for the formation of hydrocarbon-rich products.
- Gasification: Involves partial oxidation with a controlled amount of oxygen or steam. This process primarily produces syngas, a mixture of carbon monoxide and hydrogen, along with some carbon dioxide. The presence of oxygen enables partial combustion, which drives the gasification reactions.
-
End Products and Applications:
-
Pyrolysis:
- Bio-oil: A liquid fuel that can be refined and used as a transportation fuel or for industrial heating.
- Bio-char: A solid residue that can be used as a soil amendment to improve soil fertility and carbon sequestration.
- Syngas: A gaseous byproduct that can be used for energy generation or further processed into chemicals.
-
Gasification:
- Syngas: The primary product, consisting mainly of carbon monoxide and hydrogen, which can be used for electricity generation, chemical synthesis, or as a fuel for industrial processes.
- Tar and Ash: Byproducts that may require additional treatment or disposal.
-
Pyrolysis:
-
Energy Efficiency and Environmental Impact:
- Pyrolysis: Generally has a lower energy efficiency compared to gasification due to the lack of exothermic oxidation reactions. However, it produces valuable liquid and solid products that can be utilized in various applications, reducing waste and environmental impact.
- Gasification: Offers higher energy efficiency because the partial oxidation reactions release heat, which can be harnessed for the process. However, the production of syngas may require additional cleaning and reforming steps to remove impurities, which can increase operational complexity and cost.
-
Operational Complexity and Cost:
- Pyrolysis: Typically simpler and less expensive to operate than gasification, as it does not require precise control of oxygen levels. However, the quality and yield of bio-oil and bio-char can vary depending on feedstock and process conditions.
- Gasification: More complex and costly due to the need for precise control of oxygen and steam levels, as well as the requirement for additional gas cleaning and reforming steps. However, it offers higher energy recovery and more consistent syngas production.
-
Suitability for Different Feedstocks:
- Pyrolysis: Can handle a wide range of feedstocks, including biomass, plastics, and municipal solid waste. The process is particularly well-suited for materials that produce high-quality bio-oil and bio-char.
- Gasification: Also versatile in terms of feedstock but is particularly effective for materials that yield high-quality syngas, such as wood, agricultural residues, and certain types of waste.
-
Environmental and Regulatory Considerations:
- Pyrolysis: Produces fewer emissions compared to gasification due to the absence of oxygen, making it more environmentally friendly. However, the handling and disposal of bio-char and tar byproducts must be managed carefully.
- Gasification: May produce more emissions, including particulate matter and volatile organic compounds, depending on the feedstock and process conditions. However, advanced gasification technologies can mitigate these emissions through effective gas cleaning and treatment.
In conclusion, the choice between pyrolysis and gasification depends on the specific goals of the project, such as the desired end products, feedstock availability, energy efficiency, and environmental considerations. Pyrolysis is more suitable for applications requiring liquid fuels and soil amendments, while gasification is better for energy generation and chemical synthesis. Both processes have their unique advantages and challenges, and the decision should be based on a thorough evaluation of these factors.
Summary Table:
Aspect | Pyrolysis | Gasification |
---|---|---|
Process Conditions | Occurs in the absence of oxygen | Involves partial oxidation with limited oxygen or steam |
Main Products | Bio-oil, bio-char, syngas | Syngas (carbon monoxide and hydrogen), tar, ash |
Energy Efficiency | Lower efficiency due to lack of exothermic reactions | Higher efficiency due to heat release from partial oxidation |
Operational Complexity | Simpler and less expensive | More complex and costly, requiring precise control and gas cleaning |
Feedstock Suitability | Wide range, including biomass, plastics, and waste | Effective for materials yielding high-quality syngas (e.g., wood, residues) |
Environmental Impact | Fewer emissions, environmentally friendly | May produce more emissions, but advanced technologies can mitigate |
Need help deciding between pyrolysis and gasification? Contact our experts today for tailored solutions!