Wet grinding is a process used to reduce particle size in a liquid medium, and the choice of mill depends on factors such as material properties, desired particle size, and operational efficiency. Ball mills and bead mills are commonly preferred for wet grinding due to their ability to handle fine particles and provide consistent results. Ball mills are versatile and suitable for a wide range of materials, while bead mills excel in achieving ultra-fine grinding with high energy efficiency. The selection ultimately depends on the specific application, material characteristics, and desired output. Below, the key points are explained in detail.
Key Points Explained:
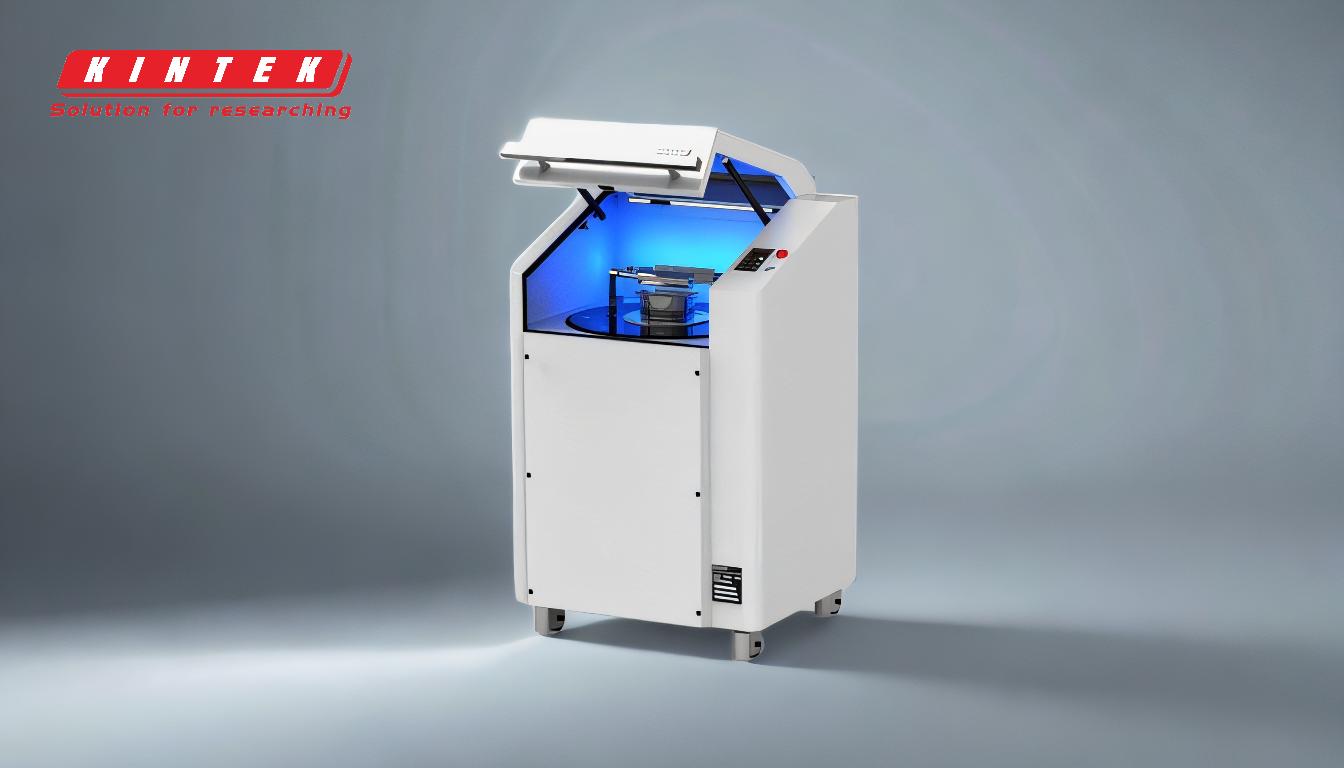
-
Wet Grinding Overview
- Wet grinding involves reducing particle size in a liquid medium, which helps in dispersing particles, preventing agglomeration, and improving mixing.
- It is widely used in industries like pharmaceuticals, paints, ceramics, and food processing.
- The choice of mill depends on factors such as material hardness, desired particle size, and production scale.
-
Preferred Mills for Wet Grinding
-
Ball Mills:
- Ball mills are cylindrical devices that use grinding media (usually steel or ceramic balls) to grind materials.
- They are versatile and can handle both dry and wet grinding.
- Ideal for coarse to medium-fine grinding, with particle sizes typically ranging from 10 to 100 microns.
- Suitable for materials like ores, ceramics, and pigments.
- Advantages: Simple design, easy operation, and cost-effectiveness.
- Limitations: Less efficient for ultra-fine grinding and can generate heat, which may affect heat-sensitive materials.
-
Bead Mills:
- Bead mills use small beads (often made of glass, ceramic, or steel) as grinding media.
- Designed for ultra-fine grinding, achieving particle sizes as small as 0.1 microns.
- Highly efficient for dispersing and grinding materials in liquid suspensions.
- Suitable for applications in paints, coatings, and nanotechnology.
- Advantages: High energy efficiency, precise control over particle size, and minimal heat generation.
- Limitations: Higher initial cost and more complex maintenance compared to ball mills.
-
-
Factors Influencing Mill Selection
-
Material Properties:
- Hardness, abrasiveness, and viscosity of the material determine the type of mill and grinding media required.
- For example, soft materials may require less aggressive grinding media, while hard materials may need durable media like zirconia beads.
-
Desired Particle Size:
- Ball mills are suitable for coarser grinding, while bead mills are better for achieving ultra-fine particles.
- The choice depends on the end-use requirements, such as paint viscosity or drug bioavailability.
-
Production Scale:
- Ball mills are often preferred for large-scale production due to their simplicity and lower cost.
- Bead mills are more suitable for small to medium-scale production where precision and fine particle size are critical.
-
Operational Efficiency:
- Bead mills are more energy-efficient for fine grinding, but ball mills may be more cost-effective for coarser applications.
- Consideration of maintenance requirements and downtime is also important.
-
-
Applications of Wet Grinding Mills
-
Ball Mills:
- Used in mining for grinding ores.
- Applied in ceramics for preparing raw materials.
- Utilized in the pharmaceutical industry for size reduction of active ingredients.
-
Bead Mills:
- Widely used in the paint and coatings industry for pigment dispersion.
- Employed in the food industry for homogenizing emulsions.
- Applied in nanotechnology for producing nano-sized particles.
-
-
Conclusion
- The preferred mill for wet grinding depends on the specific requirements of the application. Ball mills are versatile and cost-effective for coarse to medium-fine grinding, while bead mills excel in ultra-fine grinding and precision applications. Factors such as material properties, desired particle size, and production scale should guide the selection process. Understanding these key points ensures optimal performance and efficiency in wet grinding operations.
Summary Table:
Feature | Ball Mills | Bead Mills |
---|---|---|
Particle Size Range | 10 to 100 microns (coarse to medium-fine) | As small as 0.1 microns (ultra-fine) |
Material Suitability | Ores, ceramics, pigments | Paints, coatings, nanotechnology |
Advantages | Simple design, cost-effective, versatile | High energy efficiency, precise particle size control, minimal heat generation |
Limitations | Less efficient for ultra-fine grinding, heat generation | Higher initial cost, complex maintenance |
Best For | Large-scale production, coarse to medium-fine grinding | Small to medium-scale production, ultra-fine grinding |
Need help choosing the right mill for your wet grinding application? Contact our experts today for personalized advice!