Controlling the atmosphere during sintering is essential to ensure the desired material properties, prevent contamination, and optimize the sintering process. The atmosphere influences oxidation, reduction, and chemical reactions, which can significantly impact the final product's density, strength, and microstructure. By carefully selecting and controlling the atmosphere (e.g., inert gases, vacuum, or hydrogen), manufacturers can achieve uniform sintering, minimize defects, and tailor material properties to meet specific application requirements. This control is particularly critical for materials sensitive to oxidation or those requiring precise chemical compositions.
Key Points Explained:
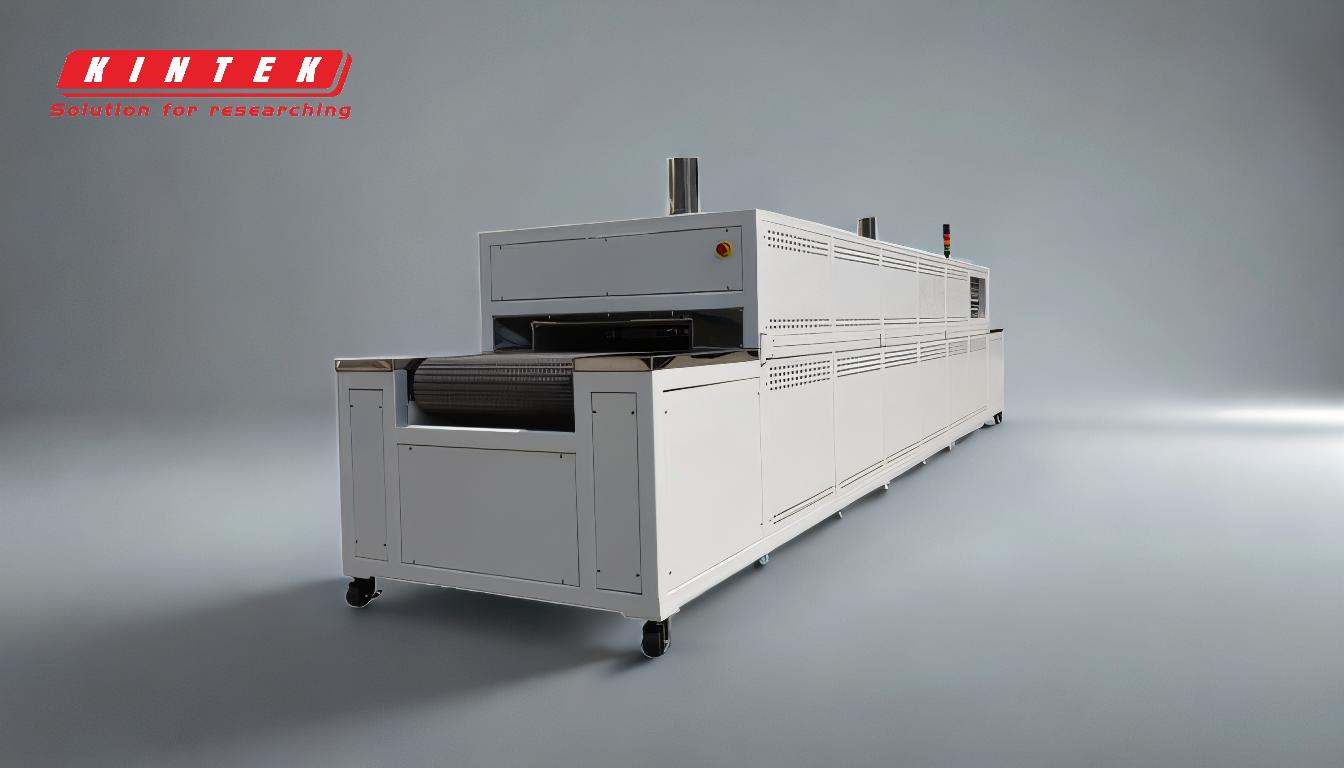
-
Prevention of Oxidation and Contamination
- Sintering often involves high temperatures, which can cause materials to react with oxygen or other gases in the environment. For example, metals like titanium or aluminum are highly reactive and can oxidize in the presence of air, leading to weakened mechanical properties and surface defects.
- An inert or protective atmosphere (e.g., argon or nitrogen) prevents oxidation by creating a barrier between the material and reactive gases. This ensures the material retains its chemical composition and structural integrity.
- In some cases, a vacuum environment is used to eliminate all gases, reducing the risk of contamination and unwanted chemical reactions.
-
Control of Chemical Reactions
- The sintering atmosphere can influence the chemical reactions that occur during the process. For instance, a hydrogen atmosphere is often used for sintering metals like tungsten or molybdenum because it acts as a reducing agent, removing oxides and impurities from the material surface.
- The choice of atmosphere depends on the material being sintered. For ceramics, an inert atmosphere may be sufficient, while metals may require a reducing or vacuum environment to achieve the desired properties.
-
Optimization of Material Properties
- The atmosphere affects the densification and microstructure of the sintered material. For example, a controlled atmosphere can promote uniform grain growth and reduce porosity, leading to higher density and improved mechanical properties such as tensile strength and fatigue resistance.
- In the case of ceramics, a controlled atmosphere ensures that particle diffusion occurs uniformly, resulting in a dense and homogeneous final product.
-
Impact on Sintering Kinetics
- The atmosphere influences the rate of sintering by affecting particle diffusion and rearrangement. For instance, a vacuum or inert atmosphere can enhance diffusion rates, reducing the time required for sintering and improving efficiency.
- The heating rate and cooling rate are also influenced by the atmosphere, as different gases have varying thermal conductivities and heat capacities. This can impact the overall sintering process and the final material properties.
-
Tailoring the Atmosphere for Specific Materials
- Different materials require specific atmospheric conditions to achieve optimal sintering results. For example:
- Metals: Often sintered in a reducing atmosphere (e.g., hydrogen) or vacuum to prevent oxidation and promote densification.
- Ceramics: Typically sintered in an inert atmosphere or air, depending on the material composition and desired properties.
- Powder Metallurgy: Inert gases like argon or nitrogen are commonly used to protect the material from contamination and ensure uniform sintering.
- Different materials require specific atmospheric conditions to achieve optimal sintering results. For example:
-
Economic and Practical Considerations
- Controlling the atmosphere can also have economic implications. For instance, using a vacuum furnace may be more expensive than using an inert gas atmosphere, but it may be necessary for materials that are highly sensitive to oxidation.
- The choice of atmosphere must balance cost, material requirements, and the desired properties of the final product.
-
Examples of Atmosphere Control in Sintering
- Inert Atmosphere (Argon, Nitrogen): Used for sintering metals and ceramics to prevent oxidation and contamination.
- Hydrogen Atmosphere: Used for sintering metals like tungsten or molybdenum to reduce oxides and improve densification.
- Vacuum Environment: Used for highly reactive materials or those requiring ultra-high purity.
- Air Atmosphere: Used for certain ceramics or materials that are not sensitive to oxidation.
By controlling the atmosphere during sintering, manufacturers can achieve consistent, high-quality results, minimize defects, and tailor material properties to meet specific application requirements. This control is a critical aspect of the sintering process, ensuring that the final product meets performance standards and functional needs.
Summary Table:
Key Aspect | Description |
---|---|
Prevention of Oxidation | Inert gases or vacuum prevent oxidation, ensuring material integrity. |
Control of Reactions | Hydrogen reduces oxides; inert gases protect ceramics. |
Optimize Material Properties | Uniform grain growth, reduced porosity, and improved strength. |
Sintering Kinetics | Atmosphere affects diffusion rates, heating, and cooling efficiency. |
Tailored Atmospheres | Metals: hydrogen/vacuum; ceramics: inert/air; powder metallurgy: argon/nitrogen. |
Economic Considerations | Balance cost and material requirements for optimal results. |
Discover how precise atmosphere control can enhance your sintering process—contact our experts today!