Low-Pressure Chemical Vapor Deposition (LPCVD) is a specialized form of CVD that operates under reduced pressure conditions. It is widely used in the semiconductor industry and other high-tech applications due to its ability to produce high-quality, uniform thin films with precise control over thickness and composition. LPCVD is particularly valued for its ability to deposit films at lower temperatures compared to atmospheric pressure CVD, making it suitable for temperature-sensitive substrates. It also offers excellent step coverage, ensuring uniform deposition over complex geometries, which is critical for advanced semiconductor devices and microfabrication processes.
Key Points Explained:
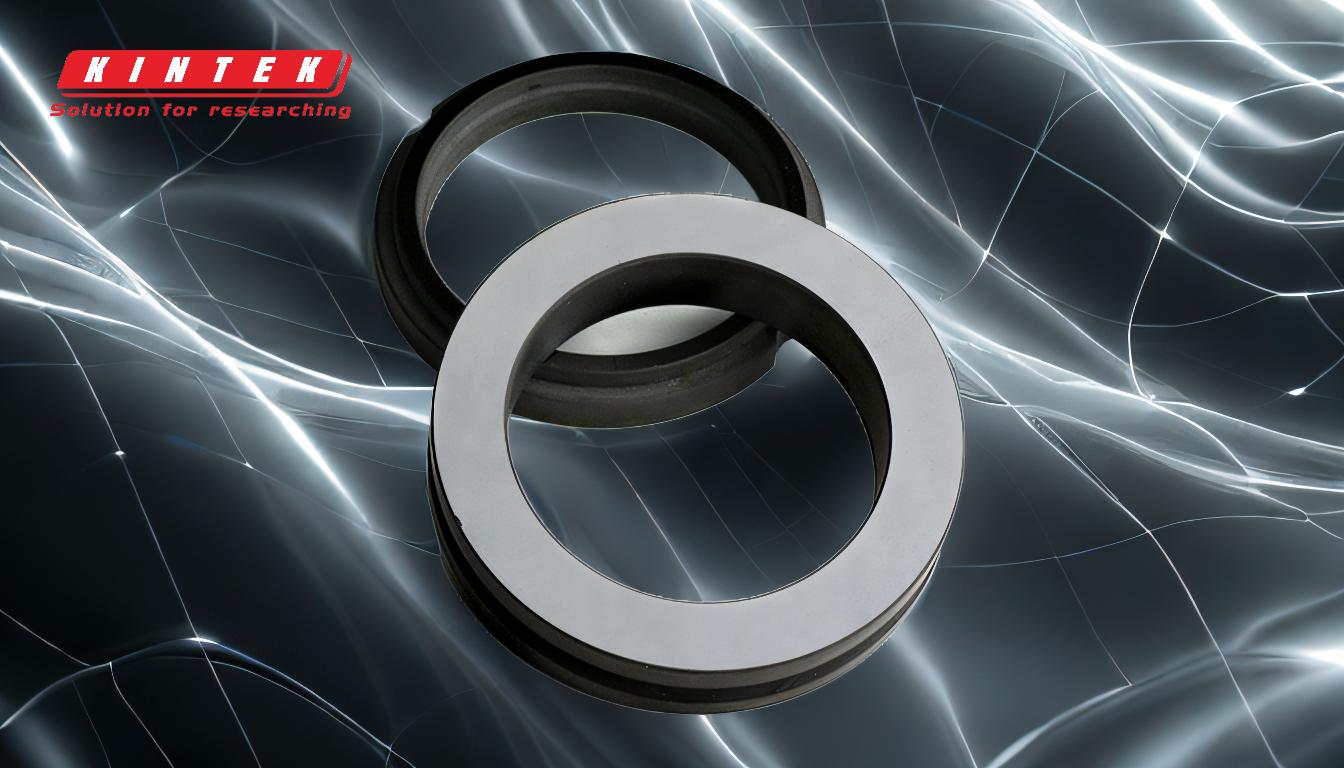
-
High-Quality Thin Films:
- LPCVD is renowned for producing high-purity and high-performance thin films, which are essential in semiconductor manufacturing. The process allows for the deposition of materials like silicon nitride, polysilicon, and silicon dioxide with exceptional uniformity and minimal defects.
- The reduced pressure environment in LPCVD minimizes unwanted reactions and contamination, resulting in films with superior electrical and mechanical properties.
-
Precise Thickness Control:
- One of the key advantages of LPCVD is its ability to achieve precise control over film thickness. This is critical in applications such as semiconductor device fabrication, where even nanometer-scale variations can impact performance.
- The process parameters, such as gas flow rates and pressure, can be finely tuned to achieve the desired film characteristics, ensuring reproducibility and consistency.
-
Lower Deposition Temperatures:
- LPCVD operates at lower temperatures compared to atmospheric pressure CVD, making it suitable for temperature-sensitive substrates and materials. This is particularly important in the semiconductor industry, where high temperatures can damage delicate components.
- The lower temperature also reduces thermal stress on the substrate, improving the overall quality and reliability of the deposited films.
-
Excellent Step Coverage:
- LPCVD provides superior step coverage, meaning it can uniformly coat complex geometries and high-aspect-ratio features. This is crucial for advanced semiconductor devices, which often have intricate structures.
- The conformal deposition ensures that even the smallest features are evenly coated, reducing the risk of defects and improving device performance.
-
Scalability and Manufacturing Efficiency:
- LPCVD is highly scalable, making it ideal for large-scale manufacturing. The deposition rate can be easily controlled by adjusting the flow rate of precursor gases, allowing for efficient production of thin films.
- The process is also compatible with batch processing, enabling multiple substrates to be coated simultaneously, which enhances throughput and reduces costs.
-
Versatility in Material Deposition:
- LPCVD can deposit a wide range of materials, including dielectrics, semiconductors, and metals. This versatility makes it a valuable tool in various industries, from electronics to optoelectronics and energy applications.
- For example, LPCVD is used to produce silicon nitride films for passivation layers in semiconductors and to create polysilicon layers for solar cells.
-
Environmental and Economic Benefits:
- LPCVD is more environmentally friendly compared to other deposition techniques, as it often requires fewer precursor materials and generates less waste. The reduced pressure environment also minimizes the release of harmful byproducts.
- The economic advantages of LPCVD include lower material costs, higher deposition rates, and the ability to produce high-quality films with minimal post-processing, making it a cost-effective solution for many applications.
In summary, LPCVD is a critical technology in modern manufacturing, particularly in the semiconductor industry, due to its ability to produce high-quality, uniform thin films with precise control over thickness and composition. Its lower operating temperatures, excellent step coverage, and scalability make it an indispensable tool for advanced microfabrication and large-scale production.
Summary Table:
Key Benefits of LPCVD | Details |
---|---|
High-Quality Thin Films | Produces high-purity, uniform films with minimal defects. |
Precise Thickness Control | Ensures nanometer-scale accuracy for semiconductor applications. |
Lower Deposition Temperatures | Protects temperature-sensitive substrates and reduces thermal stress. |
Excellent Step Coverage | Uniformly coats complex geometries, critical for advanced devices. |
Scalability and Efficiency | Ideal for large-scale manufacturing with batch processing capabilities. |
Versatility in Material Deposition | Deposits dielectrics, semiconductors, and metals for diverse applications. |
Environmental and Economic Benefits | Reduces waste, lowers costs, and minimizes harmful byproducts. |
Learn how LPCVD can enhance your manufacturing process—contact our experts today!