Nitrogen gas is widely used in the annealing process due to its ability to create an inert atmosphere, which prevents oxidation and decarburization of materials during heat treatment. It is particularly effective for tools, components, and non-ferrous metals like copper, aluminum, and brass. Nitrogen annealing ensures a clean, oxidation-free surface, making it ideal for processes such as bright annealing, neutral hardening, tempering, sintering, and brazing. Unlike hydrogen, nitrogen is safer and more cost-effective, though it has a lower heat transfer coefficient. Its inert nature and versatility make it a preferred choice for various industrial applications.
Key Points Explained:
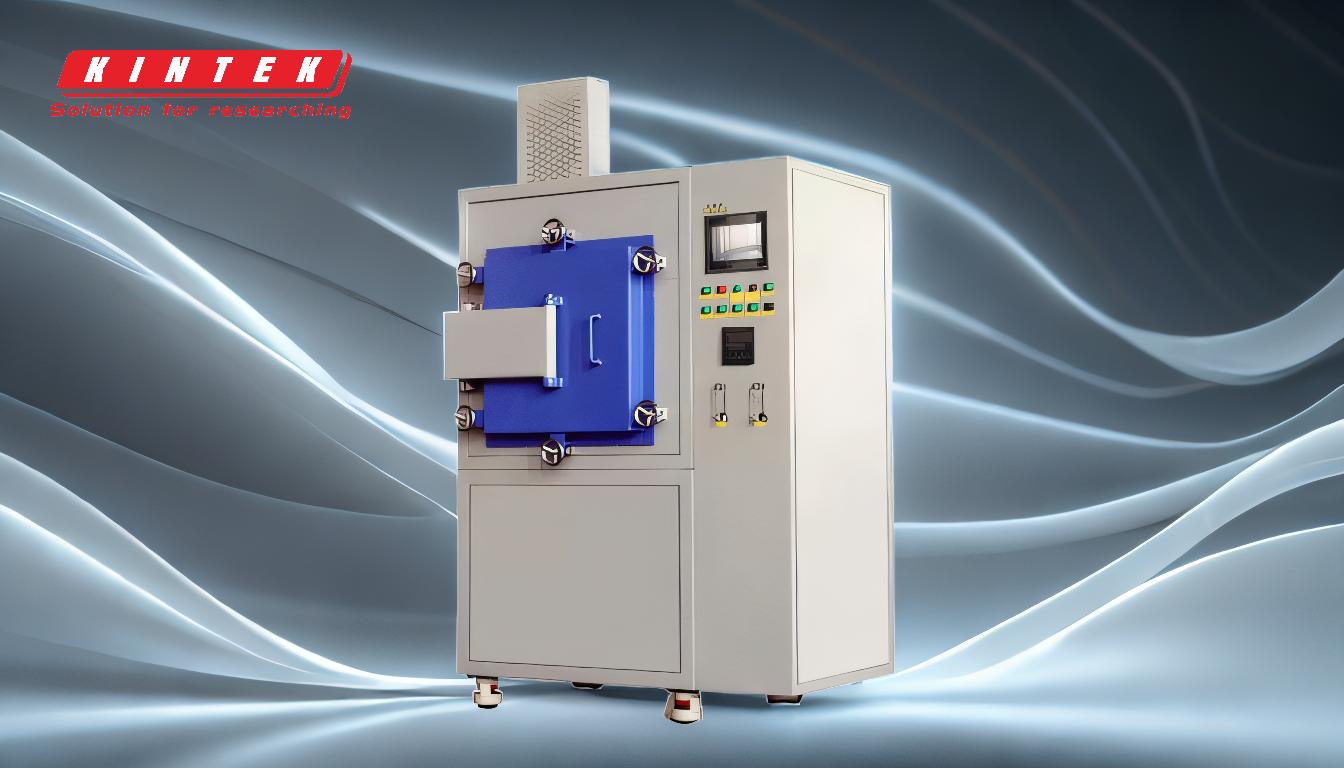
-
Prevention of Oxidation:
- Nitrogen creates an inert atmosphere in the annealing furnace, preventing oxygen from reacting with the material.
- Oxidation can degrade the surface quality and mechanical properties of metals, making nitrogen essential for maintaining material integrity.
-
Decarburization Control:
- Decarburization, the loss of carbon from the surface of steel, weakens the material.
- Nitrogen annealing minimizes decarburization by displacing oxygen and other reactive gases, ensuring uniform carbon content throughout the material.
-
Versatility in Applications:
- Nitrogen annealing is used for a wide range of materials, including ferrous and non-ferrous metals like copper, aluminum, and brass.
- It is also beneficial for tools and components such as screws, springs, bearings, and saw blades, as well as processes like nitriding, carbonitriding, and brazing.
-
Surface Quality and Bright Annealing:
- Bright annealing, a process that maintains a shiny, oxidation-free surface, relies on nitrogen to prevent discoloration and scaling.
- This is particularly important for applications where surface appearance and cleanliness are critical.
-
Safety and Cost-Effectiveness:
- Nitrogen is non-flammable and safer to handle compared to hydrogen, which is highly explosive.
- While hydrogen has a higher heat transfer coefficient, nitrogen is more cost-effective and widely available, making it a practical choice for many industries.
-
Process Efficiency:
- Nitrogen annealing ensures consistent and predictable results, reducing the need for post-treatment cleaning or surface finishing.
- Its inert nature also minimizes contamination, ensuring high-quality end products.
-
Comparison with Hydrogen:
- Hydrogen is sometimes used for its superior heat transfer properties, but it is less practical due to safety concerns and higher costs.
- Nitrogen, while less efficient in heat transfer, provides a safer and more economical alternative for most annealing applications.
By understanding these key points, purchasers and engineers can make informed decisions about using nitrogen gas in annealing processes, ensuring optimal results for their specific applications.
Summary Table:
Key Benefit | Description |
---|---|
Prevents Oxidation | Creates an inert atmosphere, stopping oxygen from degrading material surfaces. |
Controls Decarburization | Minimizes carbon loss in steel, ensuring uniform carbon content. |
Versatile Applications | Suitable for ferrous and non-ferrous metals, tools, and components. |
Bright Annealing | Maintains clean, shiny surfaces without oxidation or discoloration. |
Safety & Cost-Effectiveness | Non-flammable, safer than hydrogen, and more economical for industrial use. |
Process Efficiency | Delivers consistent results, reducing post-treatment cleaning and contamination. |
Optimize your annealing process with nitrogen gas—contact our experts today for tailored solutions!