Rotary kilns are inclined to facilitate the continuous flow of materials through the kiln, ensuring efficient processing and optimal heat transfer. The slight angle with the horizontal axis causes an axial displacement of the solid bed, moving the material towards the discharge end. This design feature is crucial for achieving the desired chemical reactions, thermal efficiency, and product quality. The inclination also aids in mixing and heat distribution, which are essential for uniform firing and sintering of materials. Additionally, the inclination helps in controlling the residence time of materials within the kiln, ensuring that they are exposed to the necessary thermal conditions for the required duration.
Key Points Explained:
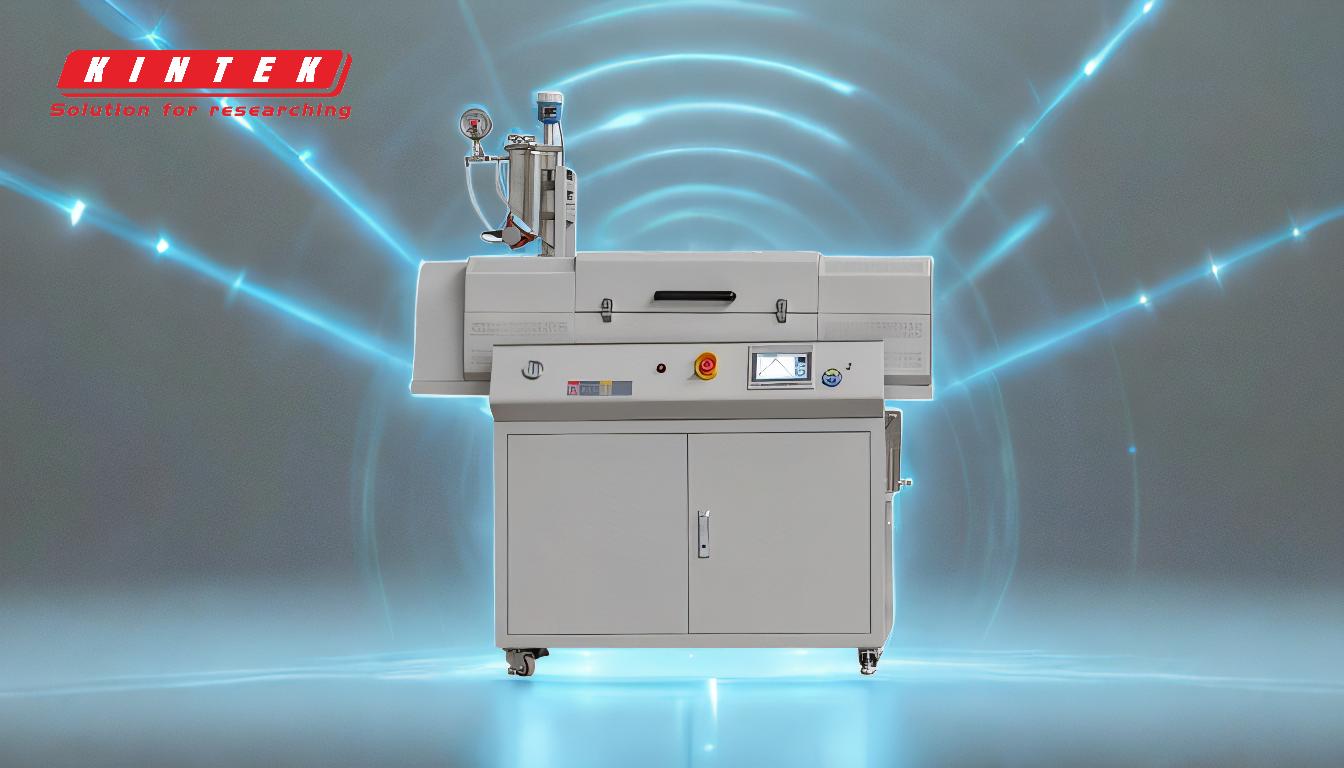
-
Facilitating Continuous Material Flow:
- The primary reason for the inclination of a rotary kiln is to ensure the continuous flow of materials from the feed end to the discharge end. The slight tilt causes the solid bed to move axially, driven by gravity, which is essential for maintaining a steady processing rate.
- This continuous flow is crucial for industries such as mining, metallurgy, and chemical processing, where consistent material movement is necessary for efficient operation.
-
Controlling Residence Time:
- The inclination angle directly affects the residence time of materials within the kiln. By adjusting the angle, operators can control how long materials are exposed to the high temperatures needed for specific chemical reactions or sintering processes.
- Proper control of residence time ensures that materials are adequately processed, leading to higher product quality and consistency.
-
Enhancing Heat Transfer and Mixing:
- The inclination aids in the mixing of materials as they move through the kiln. This mixing is essential for uniform heat distribution and efficient heat transfer, which are critical for achieving the desired thermal and chemical reactions.
- Improved mixing also helps in reducing temperature gradients within the kiln, leading to more uniform product quality.
-
Optimizing Thermal Efficiency:
- The design of the rotary kiln, including its inclination, is aimed at maximizing thermal efficiency. By ensuring a continuous and controlled flow of materials, the kiln can maintain optimal operating temperatures, reducing energy consumption and improving fuel efficiency.
- The inclination also helps in the recovery of energy from exhaust gases, which can be used to preheat the feed material, further enhancing thermal efficiency.
-
Supporting Various Process Requirements:
- Different materials and processes require specific thermal conditions and residence times. The inclination of the rotary kiln can be adjusted to meet these varying requirements, making it a versatile tool for a wide range of industrial applications.
- For example, in the production of cement, the inclination ensures that the raw materials are properly calcined and sintered, while in metallurgical processes, it helps in the reduction of ores.
-
Ensuring Safe and Efficient Operation:
- The inclination of the kiln also contributes to the safe handling of materials. By controlling the flow and residence time, the kiln can prevent overheating or underprocessing, which could lead to product defects or safety hazards.
- Additionally, the inclination helps in the efficient cooling of materials as they exit the kiln, ensuring they are safe for handling and further processing.
In summary, the inclination of a rotary kiln is a critical design feature that supports continuous material flow, controls residence time, enhances heat transfer and mixing, optimizes thermal efficiency, meets various process requirements, and ensures safe and efficient operation. This design element is essential for achieving the high-quality processing and energy efficiency required in industrial applications.
Summary Table:
Key Feature | Benefits |
---|---|
Continuous Material Flow | Ensures steady processing and efficient operation in industries like mining. |
Residence Time Control | Adjustable inclination optimizes exposure time for chemical reactions. |
Heat Transfer & Mixing | Improves uniform heat distribution and reduces temperature gradients. |
Thermal Efficiency | Maximizes energy recovery and reduces fuel consumption. |
Process Versatility | Supports diverse industrial applications like cement and metallurgy. |
Safe & Efficient Operation | Prevents overheating and ensures safe material handling. |
Learn how rotary kiln inclination can optimize your industrial processes—contact our experts today!