Vacuum is essential in thermal evaporation to ensure the deposition process is efficient, clean, and produces high-quality thin films. It achieves this by creating an environment where evaporated atoms can travel directly to the substrate without scattering or contamination from residual gas molecules. A high vacuum (typically 10^-5 to 10^-7 Torr) ensures a long mean free path for the atoms, minimizes interference from gas particles, and allows materials with low vapor pressure to form a stable vapor cloud. This results in uniform, adherent, and contamination-free thin films on the substrate.
Key Points Explained:
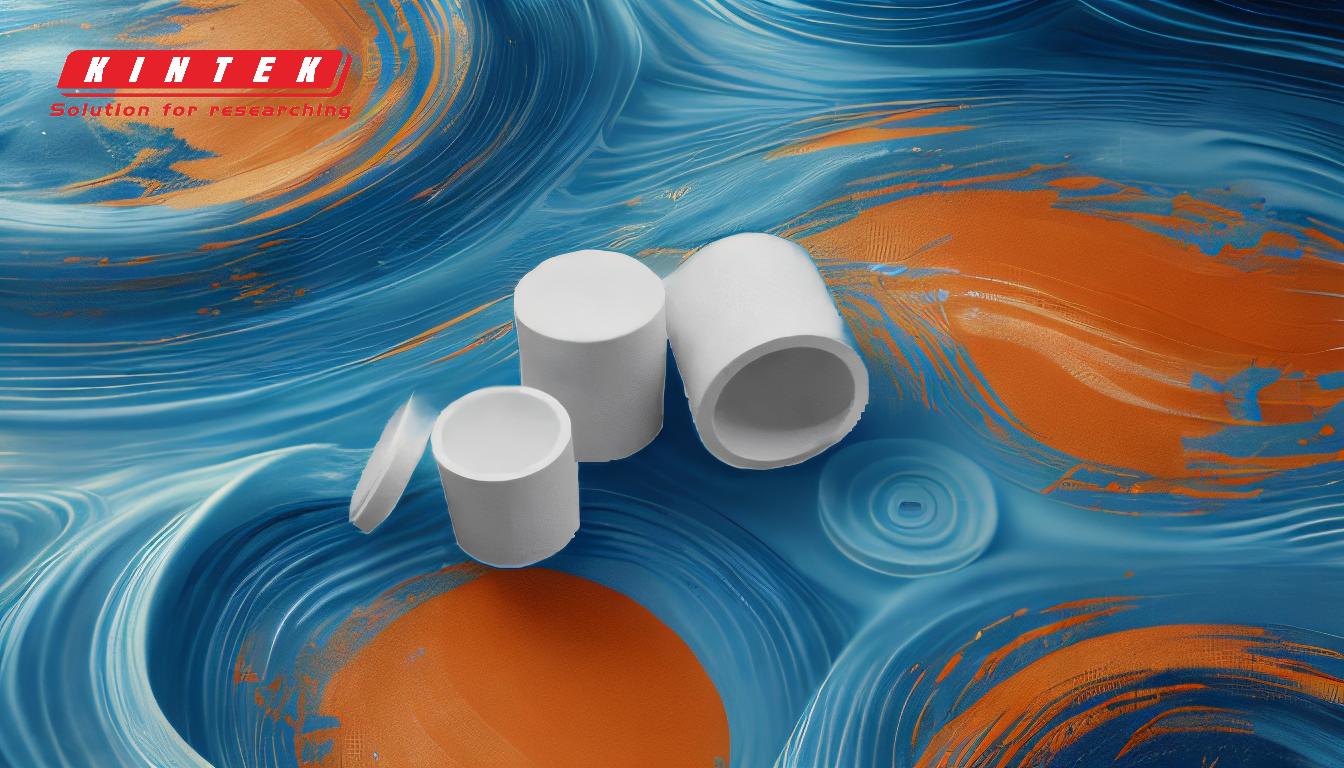
-
Ensures a Long Mean Free Path for Evaporated Atoms
- The mean free path is the average distance a particle travels before colliding with another particle. In thermal evaporation, a high vacuum ensures that the mean free path of evaporated atoms is much longer than the distance between the source and the substrate.
- At a pressure of 10^-5 Torr, the mean free path is approximately 1 meter, allowing atoms to travel in a straight line to the substrate without scattering.
- Without a vacuum, residual gas molecules would scatter the evaporated atoms, leading to poor film quality and non-uniform deposition.
-
Prevents Contamination and Ensures Clean Deposition
- A high vacuum removes residual gases (e.g., oxygen, nitrogen, water vapor) that could react with the evaporated material or interfere with the deposition process.
- Contaminants can form unstable layers or impurities in the thin film, reducing its performance and adhesion to the substrate.
- Clean surfaces are critical for ensuring that the evaporated atoms stick well and form a stable, uniform film.
-
Enables Deposition of Low Vapor Pressure Materials
- Some materials have low vapor pressures, meaning they require significant energy to evaporate. A high vacuum reduces the pressure in the chamber, allowing these materials to form a vapor cloud more easily.
- The vapor cloud then condenses on the substrate, forming a thin film. Without a vacuum, these materials might not evaporate effectively or deposit uniformly.
-
Maintains Film Quality and Uniformity
- A vacuum environment ensures that the evaporated atoms reach the substrate without collisions or deviations, resulting in a smooth, uniform film.
- Collisions with gas molecules could alter the trajectory of the atoms, leading to uneven deposition and poor film quality.
- High vacuum conditions are particularly important for applications requiring precise control over film thickness and properties, such as in semiconductor manufacturing or optical coatings.
-
Optimizes Process Efficiency
- A high vacuum minimizes energy losses due to collisions between evaporated atoms and gas molecules, making the deposition process more efficient.
- It also reduces the risk of re-evaporation or desorption of deposited material, ensuring that the film remains stable and adherent to the substrate.
By maintaining a high vacuum, thermal evaporation achieves the necessary conditions for producing high-quality thin films with minimal defects, contamination, and process inefficiencies. This is critical for applications in electronics, optics, and other advanced technologies where film performance is paramount.
Summary Table:
Key Benefit | Description |
---|---|
Long Mean Free Path | Ensures atoms travel directly to the substrate without scattering, maintaining film uniformity. |
Contamination Prevention | Removes residual gases, ensuring clean deposition and stable, adherent films. |
Deposition of Low Vapor Pressure Materials | Enables evaporation of materials with low vapor pressure, forming stable vapor clouds. |
Film Quality and Uniformity | Prevents collisions, ensuring smooth, uniform films for precise applications. |
Process Efficiency | Minimizes energy losses and re-evaporation, optimizing deposition efficiency. |
Ready to enhance your thin film deposition process? Contact us today for expert guidance!