Magnetron sputtering sources are cooled during deposition primarily to manage the significant heat generated during the process, ensuring system stability and maintaining the quality of the deposited thin film. Heat is produced due to the bombardment of the target material by high-energy ions, which can lead to overheating if not properly managed. Cooling mechanisms, such as water cooling or physical vapor deposition systems, help dissipate this heat, preventing damage to the target material and maintaining consistent deposition conditions. This ensures the reliability of the thin film's properties, such as uniformity, adhesion, and stoichiometry.
Key Points Explained:
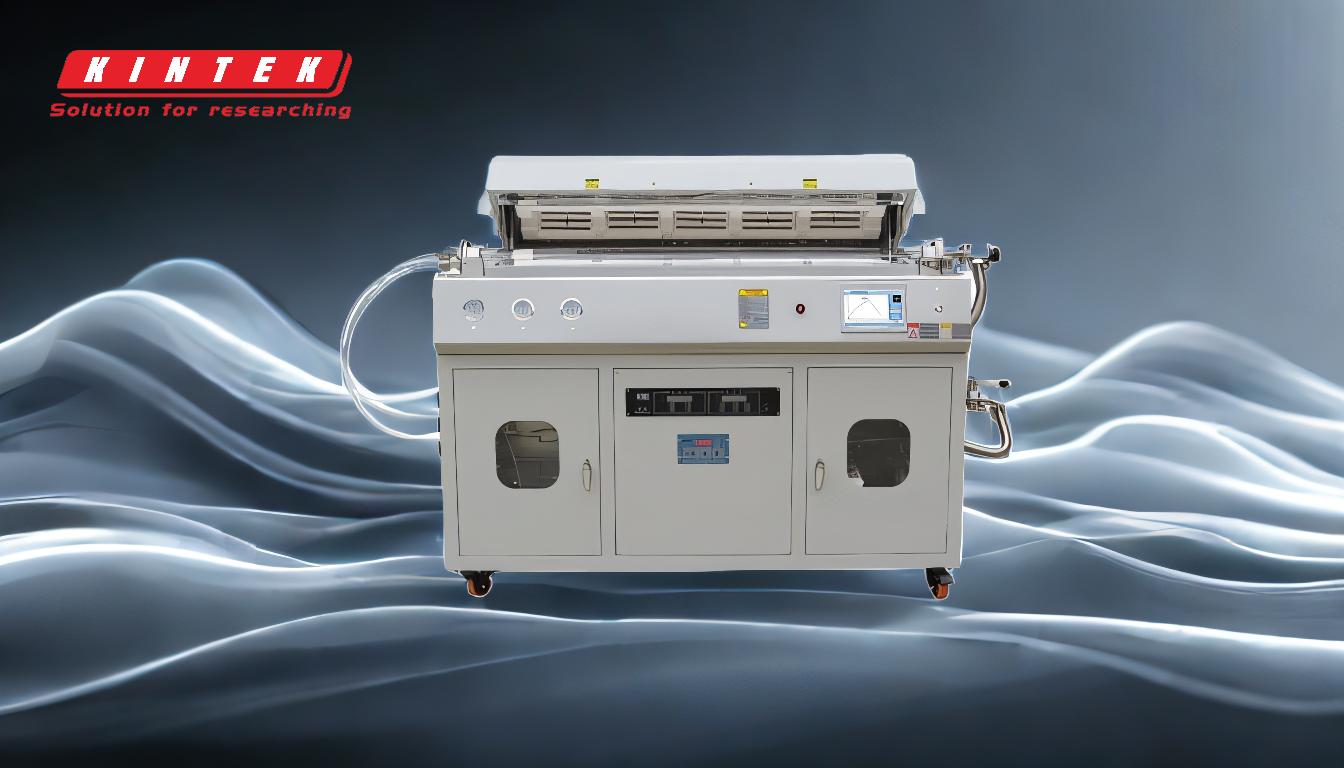
-
Heat Generation in Magnetron Sputtering
- During magnetron sputtering, high-energy ions from the sputtering gas bombard the target material, causing atoms to be ejected and deposited onto the substrate.
- This process generates significant heat due to the kinetic energy transfer from the ions to the target.
- Without proper cooling, the target and magnetron assembly can overheat, leading to thermal stress, deformation, or even melting of the target material.
-
Impact of Overheating on Deposition Quality
- Overheating can cause thermal expansion of the target, leading to cracks or warping, which disrupts the uniformity of the sputtered film.
- Excessive heat can also cause the target material to evaporate unevenly, resulting in poor film adhesion and non-uniform thickness.
- In reactive sputtering, overheating can alter the stoichiometry of the deposited film, leading to undesired chemical compositions and properties.
-
Cooling Mechanisms
- Water Cooling: The most common method, where water circulates through channels in the backing plate or magnetron assembly to absorb and dissipate heat.
- Physical Vapor Deposition (PVD) Systems: Some systems use advanced cooling techniques, such as cryogenic cooling or gas-based cooling, to maintain low temperatures.
- Cooling ensures that the target remains at a stable temperature, typically limiting the temperature rise to less than 10°C, as mentioned in the references.
-
Benefits of Cooling
- System Stability: Cooling prevents thermal runaway, ensuring consistent sputtering conditions and prolonging the lifespan of the target and magnetron.
- Film Quality: By maintaining a stable temperature, cooling ensures uniform deposition rates, better film adhesion, and precise control over film properties.
- Process Efficiency: Efficient cooling allows for higher power inputs and faster deposition rates without compromising the integrity of the target or the film.
-
Role of the Backing Plate
- The target material is mounted on a backing plate, which acts as a heat sink to transfer heat away from the target.
- The backing plate is often made of materials with high thermal conductivity, such as copper or aluminum, to enhance heat dissipation.
- In some systems, the backing plate is actively cooled using water or other cooling fluids.
-
Temperature Control in Reactive Sputtering
- In reactive sputtering, where a reactive gas (e.g., oxygen or nitrogen) is introduced, precise temperature control is critical to maintain the desired chemical reactions.
- Overheating can lead to uncontrolled reactions, affecting the stoichiometry and properties of the deposited film.
- Cooling ensures that the target and substrate remain at optimal temperatures for controlled reactive sputtering.
-
Magnetic Field and Heat Management
- The magnetic field in DC magnetron sputtering traps electrons near the target surface, increasing the efficiency of ion formation and sputtering.
- However, this localized plasma also concentrates heat in specific areas of the target, making cooling even more critical to prevent hot spots and uneven erosion.
-
Operational Parameters and Cooling
- The references mention typical operational parameters, such as a sputtering voltage of 100V to 3kV and a current of 0 to 50mA.
- These parameters generate substantial heat, and cooling ensures that the system operates within safe temperature limits, maintaining consistent deposition rates and film quality.
By addressing these key points, it becomes clear that cooling is not just a supplementary feature but a fundamental requirement for the successful operation of magnetron sputtering systems. It ensures the longevity of the equipment, the quality of the deposited films, and the overall efficiency of the deposition process.
Summary Table:
Key Aspect | Details |
---|---|
Heat Generation | High-energy ions bombard the target, generating significant heat. |
Overheating Impact | Causes thermal stress, uneven film deposition, and altered stoichiometry. |
Cooling Mechanisms | Water cooling, PVD systems, and cryogenic cooling maintain stable temperatures. |
Benefits of Cooling | Ensures system stability, film quality, and process efficiency. |
Role of Backing Plate | Acts as a heat sink, often made of copper or aluminum for better dissipation. |
Reactive Sputtering | Precise temperature control is critical for controlled chemical reactions. |
Magnetic Field Impact | Concentrates heat, making cooling essential to prevent hot spots. |
Operational Parameters | Sputtering voltage (100V-3kV) and current (0-50mA) require effective cooling. |
Optimize your magnetron sputtering process with expert guidance—contact us today!