Pre-sintering is a critical step in the manufacturing process of certain metals, particularly those with high melting points or those used in specialized applications like zirconia. It involves heating the material to a temperature below its melting point to remove organic binders, partially densify the material, and prepare it for further processing. This step ensures the material is in a "bisque state," which is soft enough for milling but durable enough to maintain structural integrity during handling. Pre-sintering also helps reduce porosity, improve mechanical properties, and enhance the final product's strength, durability, and consistency.
Key Points Explained:
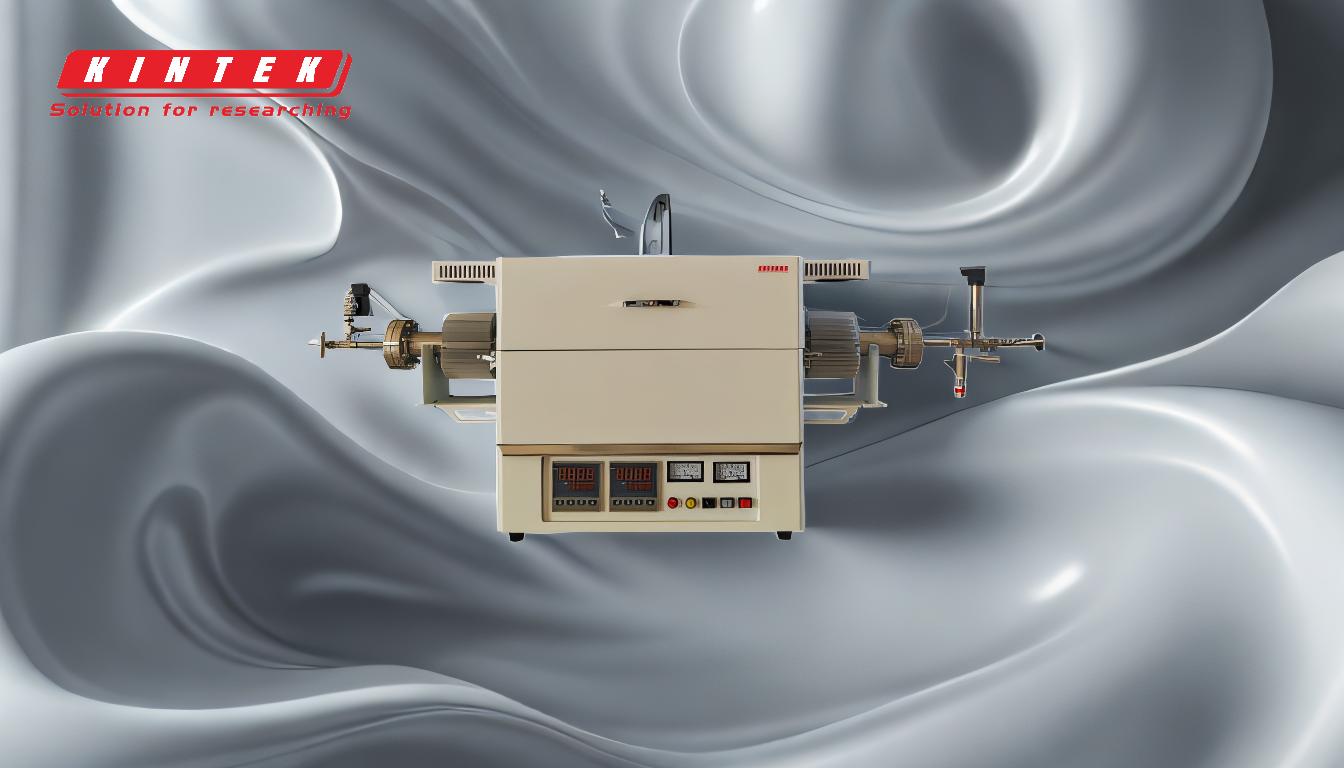
-
Removal of Organic Binders
- Pre-sintering is essential for removing organic binders used during the compaction process. These binders help shape the material initially but must be eliminated to avoid defects in the final product.
- Heating the material to a specific temperature burns off these binders, ensuring the material is free from impurities that could compromise its structural integrity or performance.
-
Partial Densification
- Pre-sintering partially densifies the material, reducing porosity and improving its mechanical properties.
- This step creates a "bisque state," where the material is soft enough for machining or milling but retains enough strength to withstand handling and further processing.
-
Preparation for Final Sintering
- Pre-sintering prepares the material for the final sintering process by creating a stable structure that can undergo further heating without losing shape or integrity.
- It ensures that the material shrinks uniformly during final sintering, maintaining dimensional accuracy and consistency in the final product.
-
Enhanced Mechanical Properties
- By reducing porosity and forming sintered necks between particles, pre-sintering enhances the material's strength, durability, and structural integrity.
- This step is particularly important for materials used in high-stress applications, such as filters, catalysts, or dental implants, where strength and consistency are critical.
-
Improved Workability
- Pre-sintered materials are easier to machine or mill compared to fully sintered materials, which are often too hard or brittle for precise shaping.
- This workability is crucial for creating complex geometries or fine details in the final product.
-
Controlled Atmosphere and Temperature
- Pre-sintering is performed in a controlled atmosphere furnace at temperatures below the material's melting point. This prevents melting while allowing the material to bond and densify.
- The controlled environment also helps reduce surface oxidation and other chemical reactions that could degrade the material's properties.
-
Customizable Cooling Rates
- The cooling rate during pre-sintering can be adjusted to fine-tune the material's properties, such as hardness, toughness, or thermal conductivity.
- This customization is vital for meeting specific application requirements and optimizing performance.
-
Application-Specific Benefits
- For materials like zirconia, pre-sintering creates blocks that are soft enough for milling into dental crowns or other medical devices but durable enough to maintain their shape during handling.
- In industrial applications, pre-sintering ensures that filters or catalysts maintain gas absorbency while gaining strength and durability.
By addressing these key points, pre-sintering plays a vital role in ensuring the quality, consistency, and performance of metal components, particularly in specialized applications where precision and durability are paramount.
Summary Table:
Key Benefits of Pre-Sintering | Description |
---|---|
Removal of Organic Binders | Burns off binders to eliminate impurities and ensure structural integrity. |
Partial Densification | Reduces porosity, creating a 'bisque state' for machining and handling. |
Preparation for Final Sintering | Ensures uniform shrinkage and dimensional accuracy during final sintering. |
Enhanced Mechanical Properties | Improves strength, durability, and structural integrity for high-stress applications. |
Improved Workability | Makes materials easier to machine or mill for complex geometries. |
Controlled Atmosphere | Prevents melting and oxidation, preserving material properties. |
Customizable Cooling Rates | Fine-tunes hardness, toughness, and thermal conductivity for specific needs. |
Application-Specific Benefits | Enables precise milling for dental crowns, filters, and catalysts. |
Discover how pre-sintering can optimize your metal manufacturing process—contact our experts today!