Introduction
Table of Contents
- Introduction
- Understanding Isostatic Pressing
- Isostatic Pressing in Food Processing
- Effects of Isostatic High-Pressure Presses
- Changes to the Functional and Sensory Properties of Food Components
- Applied Pressure and Temperature in Isostatic Pressing
- Advantages of Isostatic Pressing
- Application of Isostatic Pressing in Other Industries
- Conclusion
Isostatic pressing is a fascinating technology that has numerous applications and benefits across various industries. It involves the application of uniform, simultaneous, and omnidirectional pressure to materials, resulting in unique properties and transformations. In the world of food processing, isostatic pressing plays a crucial role as a mild preservation technology. It helps in deactivating microorganisms and enzymes, while also preserving the vitamins, natural colorings, and flavorings of food products. Furthermore, it can bring about beneficial alterations to macromolecules, such as protein denaturation and starch gelatinization. Let's explore the effects and advantages of isostatic pressing in greater detail.
Understanding Isostatic Pressing
Definition and process of isostatic pressing
Isostatic pressing is a powder processing technique that uses fluid pressure to compact materials. It involves applying equal pressure from all directions to a powder mixture, reducing its porosity and increasing its density. The powder mixture is enclosed within a flexible membrane or hermetic container, which acts as a pressure barrier. The pressure is then applied using a liquid or gas medium.
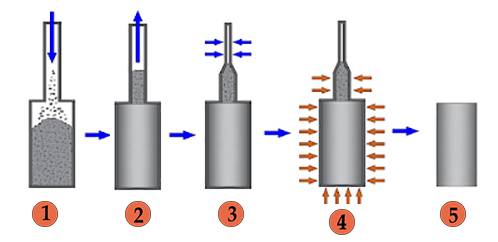
Isostatic pressing differs from uniaxial pressing in that it takes place under hydrostatic conditions, with pressure transmitted equally in all directions. This eliminates or significantly reduces die wall friction. The tooling used in isostatic pressing consists of elastomeric molds instead of rigid dies. The powder is loaded into the flexible mold, sealed, and pressure is applied in a pressure vessel.
Application of uniform, simultaneous, and omnidirectional pressure in food products
Isostatic pressing is commonly used in the food industry for mild preservation techniques such as pasteurization and sterilization. It applies uniform, simultaneous, and omnidirectional pressure to food products, which helps in deactivating microorganisms and enzymes, denaturing proteins and polysaccharides, and breaking down cell walls and membranes.
By applying uniform pressure from every direction, isostatic pressing helps preserve the vitamins, natural colorings, and flavorings in food products. It also allows unwanted substances to penetrate the cell walls, cell membranes, and nuclei of microorganisms, providing effective preservation.
Isostatic pressing is a valuable manufacturing process that is used in various industries, including ceramics, metals, composites, plastics, and carbon. It offers unique benefits for ceramic and refractory applications, allowing for precise shaping of products and reducing the need for costly machining.
Isostatic Pressing in Food Processing
Role as a mild preservation technology
Isostatic pressing is a powder processing technique that applies uniform, equal force over the entire product, regardless of shape or size. In food processing, it serves as a mild preservation technology for both pasteurization and sterilization. This process helps preserve vitamins, natural colorings, and flavorings in food products.
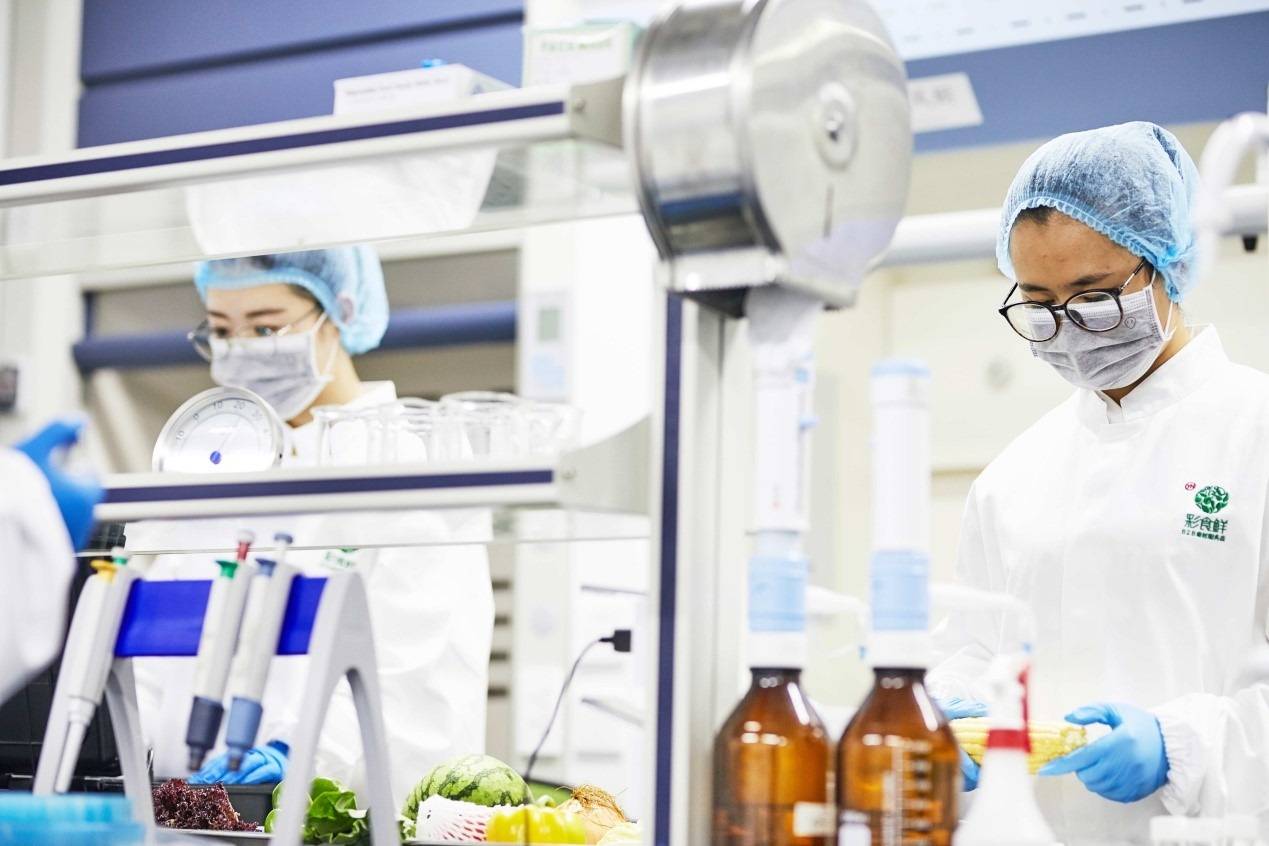
Preservation of vitamins, natural colorings, and flavorings
The isostatic pressing process helps preserve the nutritional value and sensory attributes of food. By applying uniform pressure from every direction, it breaks down the cell wall, cell membrane, and membrane surrounding the nucleus of microorganisms. This breakdown allows unwanted substances to penetrate, deactivating microorganisms and enzymes that can lead to spoilage.
Breakdown of cell wall, cell membrane, and membrane surrounding the nucleus of microorganisms
The isostatic pressing process applies uniform, simultaneous, and omnidirectional pressure to food products. This pressure leads to the breakdown of the cell wall, cell membrane, and membrane surrounding the nucleus of microorganisms. As a result, the unwanted substances can penetrate and deactivate these microorganisms, ensuring food safety and extending shelf life.
Isostatic pressing offers several advantages in food processing, including uniform strength in all directions, uniform density, and shape flexibility. It is a valuable technique for preserving the quality and safety of food products while retaining their natural attributes.
Effects of Isostatic High-Pressure Presses
Deactivation of Microorganisms and Enzymes
Isostatic high-pressure presses have the ability to deactivate microorganisms and enzymes in food products. The uniform and simultaneous pressure applied by these presses can effectively break down the cell walls, cell membranes, and membranes surrounding the nucleus of microorganisms. This process leads to the deactivation of harmful microorganisms and enzymes, ensuring the safety and preservation of the food.
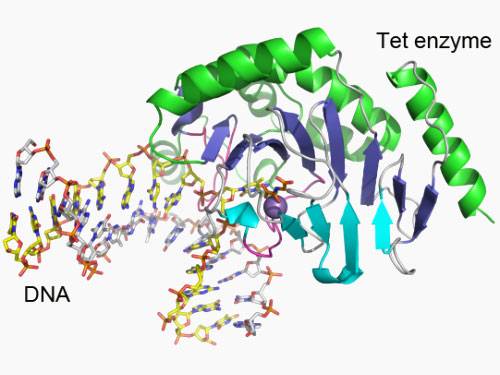
Denaturing of Proteins and Polysaccharides
The application of isostatic high-pressure presses can also result in the denaturation of proteins and polysaccharides. The uniform pressure exerted from all directions alters the tertiary and quaternary structures of these molecules, which are mainly maintained by hydrophobic and ionic interactions. This denaturation process can be beneficial in altering the functional and sensory properties of various food components, particularly proteins.
Alterations to Macromolecules
Isostatic high-pressure presses have the capability to induce alterations to macromolecules such as lipid crystallization, protein and enzyme denaturation, and starch gelatinization. The uniform and equal force exerted by these presses throughout the entire product allows for uniform compaction of powders and uniform density within the compacted part. This process is particularly advantageous in the production of parts with larger sizes, high thickness to diameter ratios, and superior material properties.
Isostatic pressing is commonly used in various industries, including pharmaceuticals, explosives, chemicals, food, nuclear fuel, and ferrites. The advantages of isostatic pressing include uniform strength in all directions, uniform density, and shape flexibility. This manufacturing process offers efficient material utilization, making it suitable for difficult-to-compact and expensive materials.
In food processing, isostatic high-pressure presses serve as a mild preservation technology that preserves vitamins, natural colorings, and flavorings. The uniform pressure applied to the food products helps maintain their shape and integrity while deactivating microorganisms and enzymes. This process also allows for pasteurization and sterilization, ensuring the safety and quality of the food.
Overall, isostatic high-pressure presses have significant effects on the deactivation of microorganisms and enzymes, denaturation of proteins and polysaccharides, and alterations to macromolecules. These presses offer numerous advantages in various industries, particularly in food processing, where they contribute to food safety, preservation, and quality.
Changes to the Functional and Sensory Properties of Food Components
Alteration of tertiary and quaternary structures of molecules
The functional and sensory properties of food components can be altered through various processes. One such process is the alteration of tertiary and quaternary structures of molecules. These structures are maintained mainly by hydrophobic and ionic interactions. High pressure above 200 MPa can beneficially alter these structures (25).
The applied pressure is isostatic, meaning it is uniformly propagated throughout the entire product. This ensures that the pressure is evenly distributed, resulting in uniform changes to the molecular structures. Additionally, the temperature of the treated foodstuff may increase, but it can be controlled by cooling the pressure chamber if necessary.
Among the advantages of isostatic pressing is the ability to achieve uniform strength in all directions and uniform density. This process also offers shape flexibility, allowing for the alteration of various food components regardless of their shape or size.
Beneficial alterations brought by high pressure above 200 MPa
High pressure above 200 MPa can bring about beneficial alterations to food components. This process, known as isostatic high-pressure pressing, applies a uniform, equal force over the entire product, deactivating microorganisms and enzymes and denaturing proteins and polysaccharides.
Isostatic high-pressure pressing is a mild preservation technology used for both pasteurization and sterilization. It preserves vitamins, natural colorings, and flavorings in food products. This process breaks down the cell wall, cell membrane, and membrane surrounding the nucleus of microorganisms, allowing unwanted substances to penetrate.
Overall, pressure treatment can be used to alter the functional and sensory properties of various food components, especially proteins. By altering the tertiary and quaternary structures of molecules, isostatic pressing provides a means to enhance the quality and characteristics of food products.
Applied Pressure and Temperature in Isostatic Pressing
Uniform propagation of isostatic pressure throughout the product
Isostatic pressing is a manufacturing process that applies a uniform and equal force over the entire product, regardless of its shape or size. This technique is commonly used in industries such as ceramics, metals, composites, plastics, and carbon. The all-around pressure exerted by the fluid during isostatic pressing provides uniform compaction of the powder and uniform density within the compacted part. This ensures that there is no density variation within the product, which is a major concern in conventional processing methods. Isostatic pressing is particularly beneficial for parts that are larger, have high thickness to diameter ratios, or require superior material properties.
Max temperature increase to 25°C due to energy input via high pressure
In hot isostatic pressing, the products are placed into a closed container and subjected to high pressure (50-200MPa) of argon gas. At the same time, the products are heated through a heating furnace inside the container. This combination of high temperature (400-2000℃) and high pressure allows for the densification of the products. The temperature increase during hot isostatic pressing is limited to a maximum of 25°C due to the energy input via high pressure. This controlled temperature increase ensures that the products are treated effectively without compromising their structural integrity.
Possibility of pressure chamber cooling if temperature rise is undesirable
During the hot isostatic pressing process, if the temperature rise becomes undesirable for certain products or materials, it is possible to implement pressure chamber cooling. This involves cooling the pressure chamber to counteract the temperature increase. By controlling the temperature rise, the desired characteristics of the products can still be achieved while maintaining their structural integrity.
Isostatic pressing offers unique benefits in terms of uniform pressure distribution and precise shaping of products. It is widely used in various industries for consolidating powders or healing defects in castings. The process ensures uniform compaction and density within the product, resulting in improved material properties. Whether it's cold isostatic pressing or hot isostatic pressing, the applied pressure and temperature play crucial roles in achieving the desired results.
Advantages of Isostatic Pressing
Uniform strength in all directions
Isostatic pressing applies pressure equally from all directions, resulting in uniform strength throughout the material. This ensures that the final product has consistent mechanical properties and can withstand external forces from any direction.
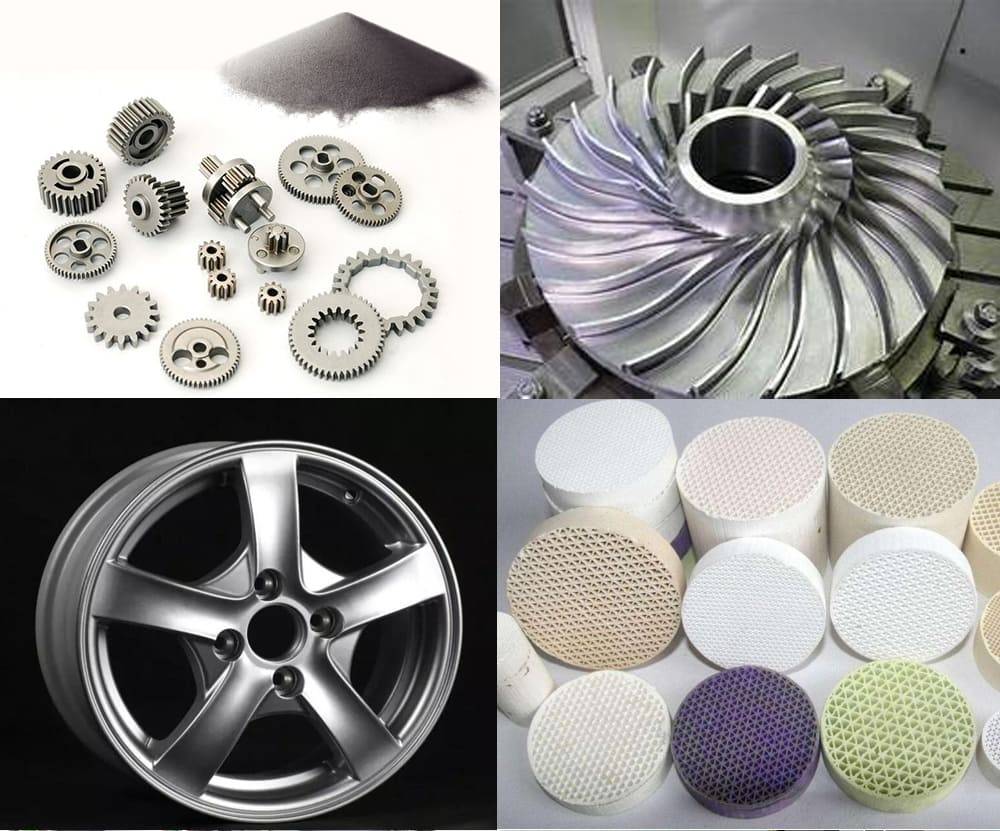
Uniform density
Isostatic pressing allows for the achievement of high and uniform density in the compacted powder. The process eliminates the need for lubricants, resulting in a compacted piece with minimal shrinkage during sintering or hot isostatic pressing. This leads to a final product with uniform density and little to no warpage.
Shape flexibility
One of the major advantages of isostatic pressing is its ability to produce shapes and dimensions that are difficult or impossible to achieve with other manufacturing methods. The process removes many constraints that limit the geometry of parts compacted unidirectionally in rigid dies. This shape flexibility opens up possibilities for designing complex components and customized parts.
Component size
Isostatic pressing can be used to produce a wide range of component sizes. From massive 30-ton near net PM shapes to densifying less than 100-gram MIM parts, the process is versatile in accommodating different sizes. The size of the parts is limited only by the size of the isostatic pressure chamber, allowing for the production of both small and large components.
Low tooling cost
In comparison to other manufacturing methods, isostatic pressing offers low tooling costs for short production runs. The process requires minimal tooling, making it an economical choice for producing complex shapes in small quantities. This cost advantage makes isostatic pressing an attractive option for prototyping and low-volume production.
Enhance alloying possibilities
Isostatic pressing allows for the enhancement of alloying elements without inducing segregation in the material. This means that the process can be used to create materials with improved properties by incorporating alloying elements in a uniform manner. This enhances the overall performance and functionality of the final product.
Reduced lead times
Isostatic pressing enables the economical production of complex shapes from prototype to production quantities with significantly reduced lead times compared to other methods such as forgings or machined components. The flexibility and efficiency of the process contribute to faster turnaround times, allowing businesses to bring their products to market more quickly.
Material and machining costs
By utilizing isostatic pressing to create near-net-shape parts, material and machining costs can be greatly reduced. The process allows for the fabrication of components with minimal material waste, resulting in cost savings. Additionally, the need for extensive machining operations is minimized, further reducing production costs.
Isostatic pressing offers numerous advantages for the manufacturing of components. From uniform strength and density to shape flexibility and cost efficiency, this process provides business professionals with a reliable and versatile method for producing high-quality parts.
Application of Isostatic Pressing in Other Industries
Industries that apply isostatic press:
- Pharmaceuticals
- Explosives
- Chemicals
- Nuclear fuel Ferrites
Other application industries of isostatic presses (pharmaceuticals, explosives, chemicals, nuclear fuel ferrite)
Two main types of isostatic presses:
- Cold isostatic presses (CIP)
- Hot isostatic presses (HIP)
Cold Isostatic Pressing vs. Hot Isostatic Pressing: A Comparative Overview
In the realm of materials processing, two powerful techniques stand out: Cold Isostatic Pressing (CIP) and Hot Isostatic Pressing (HIP). While both methods share the goal of enhancing material properties, they do so under different conditions, each offering unique advantages. Here's a comparative overview of Cold Isostatic Pressing vs. Hot Isostatic Pressing:
Cold Isostatic Pressing (CIP):
Cold Isostatic Pressing, often referred to as cold isostatic compaction, involves subjecting a material to uniform pressure from all sides. This is achieved by immersing the material in a high-pressure fluid medium and applying hydraulic pressure. CIP is particularly effective for shaping and consolidating powdered materials, creating intricate shapes and achieving high green density.
Advantages of Isostatic Press:
- Powder is compacted with the same pressure in all directions, and, since no lubricant is needed, high and uniform density can be achieved.
- The process removes many of the constraints that limit the geometry of parts compacted unidirectionally in rigid dies.
- It is applicable to difficult-to-compact and expensive materials such as superalloys, titanium, tool steels, stainless steel, and beryllium, with material utilization that is highly efficient.
Application of Isostatic Press:
- Pharmaceuticals
- Explosives
- Chemicals
- Food
- Nuclear fuel Ferrites
Cold Isostatic Pressing (CIP) and Hot Isostatic Pressing (HIP) are two powder metallurgy techniques used to produce dense and high-quality metal components.
In CIP, metal powder is placed inside a flexible mould made of rubber, urethane, or PVC. The assembly is then pressurized hydrostatically in a chamber, usually using water, with pressures ranging from 400 to 1000MPa. The powder gets compacted, and the green compact is taken out and sintered.
The isostatic pressing process was pioneered in the mid-1950s and has steadily grown from a research curiosity to a viable production tool. Many industries apply this technique for consolidation of powders or defect healing of castings. The process is used for a range of materials, including ceramics, metals, composites, plastics, and carbon.
Isostatic pressing applies a uniform, equal force over the entire product, regardless of shape or size. It thus offers unique benefits for ceramic and refractory applications. The ability to form product shapes to precise tolerances (reducing costly machining) has been a major driving force for its commercial development.
Other industries that applied isostatic press include: pharmaceuticals, explosives, chemicals, nuclear fuel Ferrites. There are two main types of isostatic presses; cold isostatic presses (CIP) that function at room temperature and hot isostatic presses (HIP) that function at elevated temperatures.
Conclusion
Isostatic pressing offers a wide range of benefits and applications in various industries, including food processing. As a mild preservation technology, it helps in deactivating microorganisms and enzymes while preserving the vitamins, natural colorings, and flavorings of food products. Additionally, isostatic pressing brings about beneficial alterations to macromolecules, such as lipid crystallization, protein and enzyme denaturation, and starch gelatinization. It also alters the tertiary and quaternary structures of molecules, resulting in improved functional and sensory properties. With the advantages of uniform strength in all directions, uniform density, and shape flexibility, isostatic pressing proves to be a valuable technique for enhancing product quality and performance.
If you are interested in this product you can browse our company website: https://kindle-tech.com/product-categories/isostatic-press, we understand that every customer's needs are unique. Therefore, we offer a flexible customisation service to meet your specific requirements. Whether it is the specification, functionality or design of the equipment, we are able to personalise it to suit your needs. Our dedicated team will work closely with you to ensure that the customised solution will perfectly meet your experimental needs.
CONTACT US FOR A FREE CONSULTATION
KINTEK LAB SOLUTION's products and services have been recognized by customers around the world. Our staff will be happy to assist with any inquiry you might have. Contact us for a free consultation and talk to a product specialist to find the most suitable solution for your application needs!