Historical Overview of Isostatic Pressing
Table of Contents
Origins in the mid-1950s
The isostatic pressing process was pioneered in the mid-1950s and has steadily grown from a research curiosity to a viable production tool. Many industries apply this technique for consolidation of powders or defect healing of castings. The process is used for a range of materials, including ceramics, metals, composites, plastics, and carbon.
Application across various industries
Isostatic pressing applies a uniform, equal force over the entire product, regardless of shape or size. It thus offers unique benefits for ceramic and refractory applications. The ability to form product shapes to precise tolerances (reducing costly machining) has been a major driving force for its commercial development.
Industries such as aerospace, automotive, and medical require complex parts with specific geometries, and isostatic pressing offers a solution for producing these parts with superior structural integrity. By applying hydrostatic pressure to the printed part, its density and mechanical strength can be improved, which is driving adoption in sectors that utilize 3D printing technology.
The isostatic pressing industry is seeing advances in process automation and control systems, reducing human error and ensuring higher product quality. With growing concerns about sustainability and environmental impact, the isostatic pressing market is moving towards greener practices by optimizing resource utilization and reducing material waste in the stamping process.
Use across a range of materials including ceramics, metals, composites, plastics, and carbon
Isostatic pressing has applications in energy storage technologies such as lithium-ion batteries and fuel cells, which, coupled with the popularity of electric vehicles and renewable energy systems, has increased the demand for isostatic pressing technologies.

The global isostatic pressing industry size is likely to reach a valuation of US$ 8.7 billion by 2023. It is further estimated to surpass US$ 22.7 billion in 2033. The market is projected to witness steady growth at a CAGR of 10.1% over the forecast period 2023 to 2033.
The isostatic pressing industry is a dynamic and rapidly developing industry that plays a vital role in the manufacturing and production of several materials. Isostatic pressing is a technique for producing dense, uniform products with excellent mechanical properties.
Isostatic pressing encloses a powdered material in a flexible mold or container and applies even pressure on all sides. This pressure is usually applied by a liquid, such as water or oil, which acts as a medium to evenly transfer force to the material. This process effectively eliminates voids and air pockets, resulting in products with increased density, strength, and dimensional accuracy.
The isostatic press market is an important sector of the manufacturing industry, offering a unique opportunity to produce high-density, high-performance materials. The market is expected to continue to grow as the demand for advanced materials increases, creating opportunities for technological advancements and innovative solutions across industries.
The applications of isostatic presses are diverse and span a variety of industries. They are often used to manufacture advanced ceramics such as ceramic parts for the aerospace and automotive industries. Isostatically pressed ceramics have improved mechanical properties such as high hardness, wear resistance, and thermal stability.
Mechanism of Isostatic Pressing
Isostatic pressing is a powder processing technique that applies a uniform, equal force over the entire product, regardless of shape or size. This process has gained popularity in various industries, including ceramics, metals, composites, plastics, and carbon. It offers unique benefits for ceramic and refractory applications and allows for precise product shape formation.
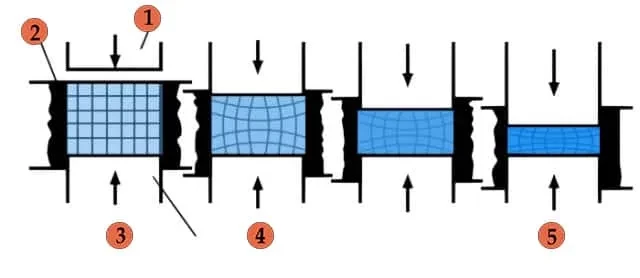
Application of uniform, equal force over the entire product
Isostatic pressing involves placing metal powders in a flexible container, which acts as the mold for the part. Fluid pressure is exerted over the entire outside surface of the container, causing the container to press and form the powder into the desired geometry. Unlike other processes that exert forces on the powder through an axis, isostatic pressing uses all-around pressure. This ensures that the force is evenly distributed, resulting in a uniform density throughout the product.
Benefits for ceramic and refractory applications
Isostatic pressing has been particularly beneficial for ceramic and refractory applications. The ability to apply equal pressure to all surfaces of the product allows for the consolidation of powders and the reduction of porosity. This leads to increased density and improved performance of the ceramic or refractory material. Additionally, isostatic pressing enables the formation of product shapes to precise tolerances, reducing the need for costly machining.
Precise product shape formation
The isostatic pressing process allows for the precise formation of product shapes. By applying equal pressure from all directions, the powder mixture is compacted and encapsulated within a flexible membrane or hermetic container. This confinement ensures that the force of compaction is uniform, resulting in a uniform density distribution and improved product performance.
Isostatic pressing has become a viable production tool since its development in the mid-1950s. Its versatility in consolidating powders and forming products with precise tolerances has made it a valuable technique in various industries. Whether it's for ceramics, metals, composites, plastics, or carbon, isostatic pressing offers a mechanism that ensures uniform force application and enables the production of high-quality products.
Types of Isostatic Pressing
Cold Isostatic Pressing (CIP)
Cold Isostatic Pressing (CIP) is a method of isostatic pressing that involves applying pressure from multiple directions to achieve greater uniformity of compaction and increased shape capability compared to uniaxial pressing. In CIP, the powder is encased in a rubber mold, which is then immersed in a liquid or filled with high-pressure fluid. This process allows for the formation of complicated shapes that cannot be achieved with other pressing methods.
Warm Isostatic Pressing (WIP)
Warm Isostatic Pressing (WIP) is a variant of cold isostatic pressing that includes a heating element. It involves applying uniform pressure to powdered products from all directions using warm water or a similar medium. WIP enables isostatic pressing at a temperature that does not exceed the boiling point of the liquid medium. This process utilizes flexible materials as a jacket mold and hydraulic pressure to shape and press the powder material.
Hot Isostatic Pressing (HIP)
Hot Isostatic Pressing (HIP) is a material processing method that compresses materials by applying high temperature and isostatic pressure simultaneously. It involves subjecting metal or ceramic products to equal pressure in all directions using an inert gas, usually argon. HIP is used for heat treatment, sintering, densification, and bonding of materials. It can improve material properties and remove defects in castings for critical applications.
Hot isostatic pressing equipment consists of a high-pressure vessel, heating furnace, compressor, vacuum pump, storage tank, cooling system, and computer control system. The high-pressure vessel is the key device in the entire equipment.
In summary, isostatic pressing is a powder processing technique that uses fluid pressure to compact the part. Cold Isostatic Pressing (CIP), Warm Isostatic Pressing (WIP), and Hot Isostatic Pressing (HIP) are different methods of applying pressure to achieve optimal density and microstructure uniformity. Each method has its own advantages and applications in various industries.
Use of Isostatic Presses in Pharmaceutical Industry
Compressing pharmaceutical particles and raw material
Isostatic pressing is a widely used process in the pharmaceutical industry for compressing pharmaceutical particles and raw materials into predetermined shapes. This pressurizing system ensures a uniform compaction pressure throughout the powder mass and a homogeneous density distribution in the final product. By applying equal pressure in all directions, isostatic presses allow for high and uniform density to be achieved without the need for lubricants.

Some advantages of using isostatic presses in the pharmaceutical industry include:
- High and uniform density: Powder is compacted with the same pressure in all directions, leading to high and uniform density in the final product.
- Greater design flexibility: Isostatic pressing removes many of the constraints that limit the geometry of parts compacted unidirectionally in rigid dies, allowing for greater design flexibility.
- Efficient material utilization: Isostatic pressing is applicable to difficult-to-compact and expensive materials, such as superalloys, titanium, tool steels, stainless steel, and beryllium, with highly efficient material utilization.
Ensuring uniform compaction pressure and homogeneous density distribution
Isostatic pressing is a manufacturing process that applies equal pressure in all directions on a powder compact, ensuring maximum uniformity of density and microstructure. This process involves subjecting a material, typically a powder, to high pressure in a sealed container filled with a fluid or gas medium. The pressure is evenly distributed, allowing for uniform compaction and consolidation of the material.
There are three basic types of isostatic pressing used in the pharmaceutical industry:
-
Cold isostatic pressing (CIP): This method is used to consolidate ceramic or refractory powders loaded into elastomeric bags at ambient temperatures.
-
Warm isostatic pressing (WIP): Similar to CIP, WIP involves pressing shapes at warm temperatures, typically around 100°C.
-
Hot isostatic pressing (HIP): HIP applies both temperature and pressure simultaneously to obtain fully dense parts with 100% theoretical density. It is mainly used for engineered ceramics that require optimum properties for high-performance applications.
Isostatic pressing offers several advantages over conventional processing methods in terms of density variation, material properties, and production capabilities. The all-around pressure exerted by the fluid during isostatic pressing provides uniform compaction of the powder and uniform density within the compacted part. This makes it particularly suitable for producing parts with larger sizes, high thickness to diameter ratios, or superior material properties.
In addition to the pharmaceutical industry, isostatic pressing finds applications in other sectors such as aerospace, automotive, and medical, where complex parts with specific geometries and superior structural integrity are required. The adoption of isostatic pressing in the 3D printing industry is also increasing, as it can improve the density and mechanical strength of printed parts. The use of automation and control systems in the isostatic press industry is reducing human error and ensuring higher product quality.
Moreover, there is a growing focus on sustainability and environmental impact, leading to the optimization of resource utilization and reduction of material waste in the stamping process. Isostatic pressing is also playing a role in energy storage technologies, such as lithium-ion batteries and fuel cells, which are in high demand due to the popularity of electric vehicles and renewable energy systems.
In conclusion, isostatic presses are valuable tools in the pharmaceutical industry for compressing particles and raw materials. They ensure uniform compaction pressure and homogeneous density distribution, leading to high-quality products. With advancements in automation, control systems, and sustainability practices, the use of isostatic pressing is expected to continue growing in various industries.
Working of Isostatic Press
Isostatic pressing is a process that enables the production of various materials from powder compacts by reducing the porosity of the powder mixture. The key to this process is the use of isostatic pressure, which is applied equally from all directions.
The powder mixture is compacted and encapsulated within a flexible membrane or hermetic container, which acts as a pressure barrier. This container ensures that the pressure is evenly distributed throughout the powder, resulting in a high and uniform density. Unlike other pressing methods, isostatic pressing does not require the use of lubricants.
Advantages of Isostatic Press
One of the main advantages of isostatic pressing is that it allows for the production of parts with complex geometries. Unlike other pressing methods that are limited by rigid dies, isostatic pressing can accommodate a wider range of shapes and sizes.
Additionally, isostatic pressing is suitable for difficult-to-compact and expensive materials such as superalloys, titanium, tool steels, stainless steel, and beryllium. The process ensures highly efficient material utilization, making it a cost-effective choice.
Application of Isostatic Press

Isostatic pressing finds applications in various industries, including:
- Pharmaceuticals
- Explosives
- Chemicals
- Food
- Nuclear fuel
- Ferrites
Types of Isostatic Pressing
Isostatic pressing can be carried out using different techniques. One common method is cold isostatic pressing, where a mold or vacuumed sample is placed into a chamber filled with a working fluid, usually water with a corrosion inhibitor. The chamber is then pressurized by an external pump, resulting in uniform pressure being exerted on the sample from all directions.
Compared to cold pressing, isostatic compaction offers several advantages. It eliminates die-wall friction, which can affect the density distribution of cold-pressed parts, resulting in more uniform densities.
Alternative Processes
Isostatic pressing stands out from other powder processing techniques due to its use of fluid pressure and its ability to apply pressure evenly from all directions. Most processes exert forces on the powder through an axis, while isostatic pressing applies pressure uniformly over the entire surface of the mold. This unique characteristic makes isostatic pressing suitable for producing complex parts with high and uniform density.
In summary, the working of isostatic press involves the use of isostatic pressure to reduce the porosity of powder mixtures and produce various materials. The advantages of this process include the ability to achieve high and uniform density, the flexibility to create complex geometries, and its suitability for difficult-to-compact and expensive materials. Isostatic pressing finds applications in various industries, and its cold isostatic pressing method offers several advantages over traditional cold pressing techniques.
Advantages of Isostatic Press
Isostatic pressing is a manufacturing method that offers several advantages over other traditional methods. Let's take a closer look at some of these advantages:
Achievement of high and uniform density
Isostatic pressing allows for the compacting of powder with the same pressure in all directions. This results in the achievement of high and uniform density in the compacted piece. During sintering or hot isostatic pressing, the piece will have minimal shrinkage and little to no warpage.
Removal of constraints limiting part geometry
Unlike other methods, isostatic pressing removes many of the constraints that limit the geometry of parts compacted unidirectionally in rigid dies. This means that isostatic pressing makes it practical to produce shapes and dimensions that are difficult or impossible to produce by other methods.
Applicability to difficult-to-compact and expensive materials
Isostatic pressing is applicable to difficult-to-compact and expensive materials such as superalloys, titanium, tool steels, stainless steel, and beryllium. These materials can be compacted effectively using isostatic pressing, allowing for the production of high-quality parts.
Highly efficient material utilization
Isostatic pressing offers highly efficient material utilization. The process ensures that the powder is compacted with the same pressure in all directions, eliminating the need for lubricant. This results in minimal material waste and efficient use of resources.
Isostatic pressing has several practical applications across different industries. Some of the most common applications include:
- Pharmaceuticals
- Explosives
- Chemicals
- Food
- Nuclear fuel Ferrites
Isostatic pressing also offers additional benefits compared to general press machines. These benefits include:
- Excellent temperature uniformity performance
- Can be processed in a dry state
- Excellent strength and accuracy
- High densification, low density variation, and uniformity
Overall, the advantages of isostatic pressing make it a preferred manufacturing method for achieving high and uniform density, producing complex shapes, working with difficult-to-compact materials, and maximizing material utilization. Whether it's in the pharmaceutical, chemical, or food industries, isostatic pressing offers numerous benefits for businesses looking to optimize their manufacturing processes.
Applications of Isostatic Press
Pharmaceuticals
The isostatic press is widely used in the pharmaceutical industry. It offers the advantage of compacting powder with the same pressure in all directions, resulting in high and uniform density. This is particularly beneficial for materials that are difficult to compact, such as certain pharmaceutical powders.
Explosives
Isostatic pressing is also applied in the production of explosives. The process allows for the uniform compaction of explosive powders, ensuring consistent performance and safety.
Chemicals
Chemical manufacturers utilize the isostatic press for various applications. It enables the compaction of chemical powders to achieve desired properties, such as improved flowability and reduced particle size.
Food
The food industry has found value in the isostatic press for its unique ability to apply uniform pressure to food products. This gentle compression process is used for mild preservation techniques like pasteurization and sterilization. It helps preserve vitamins, natural colorings, and flavorings, while also breaking down cell walls and membranes of microorganisms.
Nuclear Fuel Ferrites
Isostatic pressing plays a crucial role in the production of nuclear fuel ferrites. The process allows for the efficient compaction of these materials, ensuring their integrity and performance in nuclear applications.
Isostatic pressing is a versatile technique that finds applications in various industries. Its ability to apply uniform pressure regardless of shape or size makes it a valuable tool for compacting powders and shaping materials. Whether it's in pharmaceuticals, explosives, chemicals, food, or nuclear fuel ferrites, the isostatic press offers unique advantages and contributes to the advancement of these industries.
CONTACT US FOR A FREE CONSULTATION
KINTEK LAB SOLUTION's products and services have been recognized by customers around the world. Our staff will be happy to assist with any inquiry you might have. Contact us for a free consultation and talk to a product specialist to find the most suitable solution for your application needs!