Electric arc furnaces (EAFs) are highly efficient for specific applications, particularly in steel recycling and production. They offer significant advantages, such as 100% scrap metal recycling, operational flexibility, and the ability to produce both carbon and alloy steels. However, their efficiency is influenced by factors like energy consumption, scrap composition, and operational management. While they provide environmental benefits by reducing reliance on raw materials, their high power demand can strain electrical systems. Overall, EAFs are a versatile and efficient solution for modern steelmaking, especially in scenarios where recycling and flexibility are prioritized.
Key Points Explained:
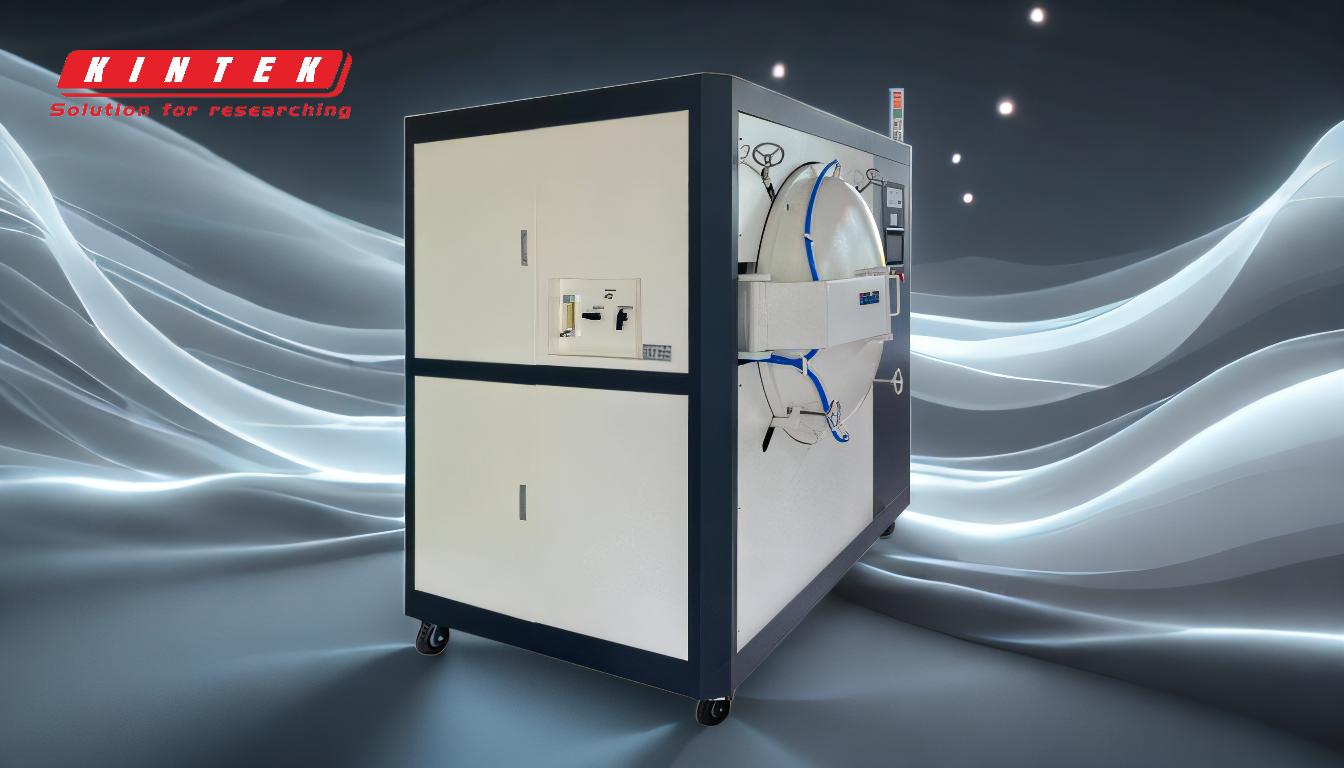
-
100% Scrap Metal Recycling:
- Electric arc furnaces excel in recycling scrap metal, making them a sustainable choice for steel production. They can process ferrous scrap into high-quality steel, reducing the need for raw materials and minimizing environmental impact. This capability aligns with global efforts to promote circular economies and reduce waste.
-
Operational Flexibility:
- EAFs offer unparalleled flexibility in operation. They can be started and stopped as needed, allowing smelters to adjust production based on demand. This intermittent operation is particularly advantageous in industries with fluctuating steel requirements, as it reduces energy waste during idle periods.
-
Energy Consumption:
- The energy required to melt scrap in an EAF ranges from 350 kWh to 370 kWh, depending on the scrap composition. While this is a significant amount of power, modern EAFs are designed to optimize energy use. However, their high power demand can strain electrical systems, necessitating careful energy management to maintain efficiency.
-
Environmental Benefits:
- By recycling scrap metal, EAFs significantly reduce the carbon footprint associated with steel production. Traditional blast furnaces rely on raw materials like iron ore and coal, which contribute to higher greenhouse gas emissions. In contrast, EAFs use electricity, which can be sourced from renewable energy, further enhancing their environmental credentials.
-
Applications in Steel Production:
- EAFs are widely used to produce carbon steel and alloy steel. The process involves melting scrap using high-powered electric arcs formed by a cathode and anodes. Limestone is added to facilitate slag formation, which helps remove impurities. This method is cost-effective and efficient for producing high-quality steel.
-
Challenges and Considerations:
- Despite their advantages, EAFs face challenges such as high power consumption and the need for precise operational control. Smelters must carefully manage energy use and scrap quality to ensure optimal performance. Additionally, the initial investment in EAF technology can be substantial, though the long-term benefits often outweigh the costs.
In summary, electric arc furnaces are efficient and versatile tools for modern steelmaking, particularly in recycling and flexible production scenarios. While they require careful energy management and operational oversight, their environmental and economic benefits make them a valuable asset in the steel industry.
Summary Table:
Key Aspect | Details |
---|---|
Scrap Metal Recycling | 100% recycling capability, reducing reliance on raw materials. |
Operational Flexibility | Can be started/stopped as needed, ideal for fluctuating steel demand. |
Energy Consumption | 350–370 kWh per ton of scrap; requires careful energy management. |
Environmental Benefits | Reduces carbon footprint and promotes circular economies. |
Applications | Produces carbon and alloy steels efficiently. |
Challenges | High power demand, operational control, and initial investment costs. |
Learn how electric arc furnaces can transform your steel production—contact us today for expert advice!