Pyrolytic ovens, also known as self-cleaning ovens, are designed to burn off food residues at high temperatures, typically around 500°C (932°F), turning them into ash that can be easily wiped away. This feature makes them highly convenient for maintaining cleanliness without the need for harsh chemical cleaners. However, whether they are "better" depends on the specific needs and priorities of the user. Pyrolytic ovens are energy-intensive during the cleaning cycle and may not be suitable for all kitchen setups. They are ideal for those who prioritize ease of cleaning and are willing to invest in a higher-end appliance. On the other hand, traditional ovens or steam-cleaning models may be more energy-efficient and cost-effective for users who are less concerned about the self-cleaning feature.
Key Points Explained:
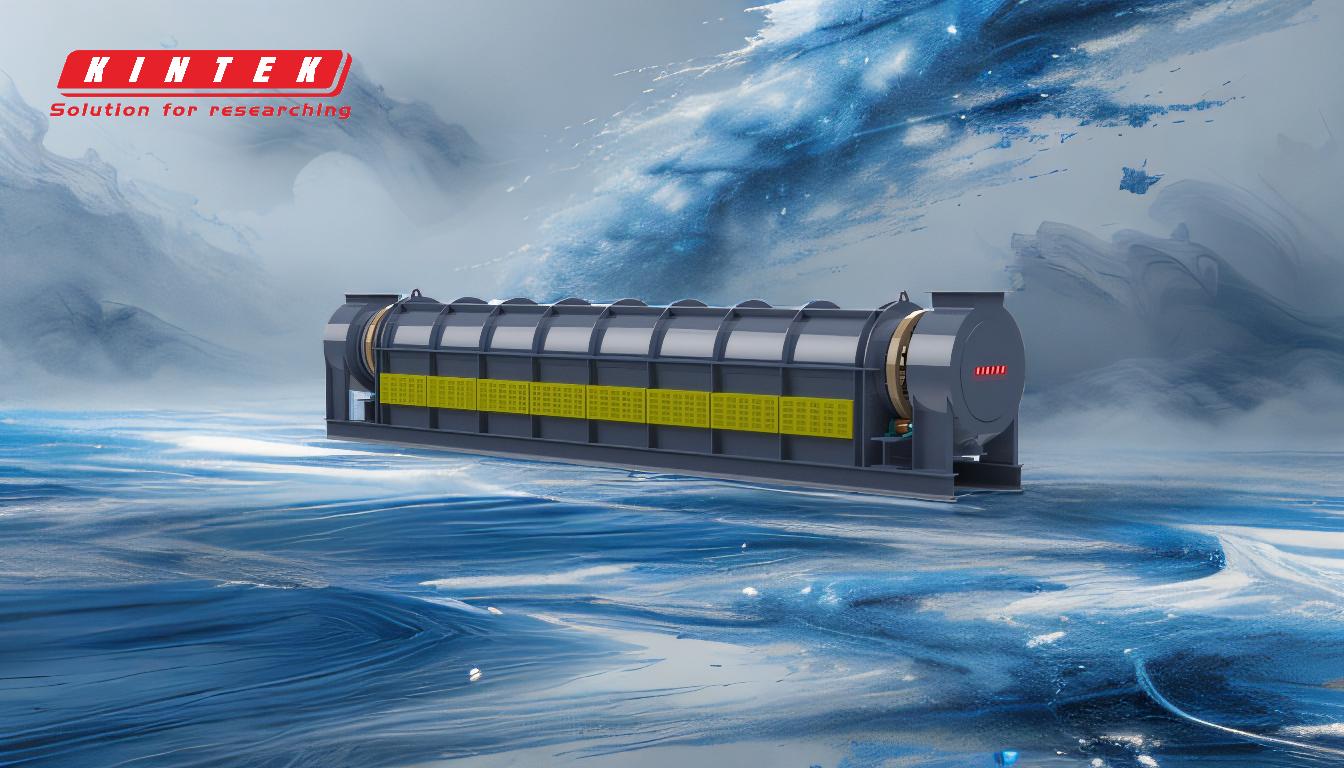
-
Self-Cleaning Mechanism:
- Pyrolytic ovens use extremely high temperatures to incinerate food residues, turning them into ash. This eliminates the need for manual scrubbing or chemical cleaners, making them highly convenient for users who value low-maintenance appliances.
- The process typically takes 2-3 hours and requires the oven to reach temperatures of around 500°C (932°F). This high heat ensures thorough cleaning but also consumes significant energy.
-
Energy Consumption:
- The pyrolytic cleaning cycle is energy-intensive, which can lead to higher electricity bills. This is a key consideration for environmentally conscious users or those looking to minimize energy costs.
- Compared to traditional ovens or steam-cleaning models, pyrolytic ovens are less energy-efficient during the cleaning process. However, they may offset this with their overall performance and convenience.
-
Safety and Ventilation:
- Pyrolytic ovens require proper ventilation due to the high temperatures and potential release of smoke or odors during the cleaning cycle. This makes them less suitable for kitchens with inadequate ventilation systems.
- Users must also ensure that the oven is free of plastic or other materials that could melt or emit harmful fumes during the cleaning process.
-
Cost and Investment:
- Pyrolytic ovens are generally more expensive than traditional ovens due to their advanced self-cleaning technology. They are considered a premium option and are often found in high-end kitchen setups.
- For users who prioritize long-term convenience and are willing to invest in a durable, low-maintenance appliance, the higher upfront cost may be justified.
-
Comparison with Steam-Cleaning Ovens:
- Steam-cleaning ovens offer an alternative to pyrolytic models, using steam to loosen food residues for easier cleaning. These models are generally more energy-efficient and may be better suited for users who prefer a gentler cleaning method.
- However, steam-cleaning ovens may not achieve the same level of cleanliness as pyrolytic ovens, particularly for heavily soiled interiors.
-
Suitability for Different Users:
- Pyrolytic ovens are ideal for busy households or individuals who value convenience and minimal effort in maintaining their appliances.
- For users with smaller kitchens, budget constraints, or a focus on energy efficiency, traditional or steam-cleaning ovens may be more practical.
-
Environmental Impact:
- The high energy consumption of pyrolytic ovens during the cleaning cycle raises concerns about their environmental impact. Users who prioritize sustainability may prefer alternatives with lower energy requirements.
- However, the long-term durability and reduced need for chemical cleaners can be seen as a positive environmental trade-off.
-
Integration with Modern Kitchens:
- Pyrolytic ovens are often integrated into modern, high-end kitchen designs, offering sleek aesthetics and advanced features. They are compatible with smart home systems and can be controlled remotely in some models.
- This makes them a popular choice for users who want a technologically advanced and visually appealing kitchen setup.
In conclusion, pyrolytic ovens are a superior choice for users who prioritize convenience, advanced features, and long-term durability. However, their higher cost, energy consumption, and ventilation requirements may make them less suitable for some households. For those interested in exploring related technologies, you can learn more about pyrolysis plants, which operate on similar principles of high-temperature decomposition.
Summary Table:
Feature | Pyrolytic Ovens | Traditional/Steam-Cleaning Ovens |
---|---|---|
Cleaning Mechanism | High-temperature burn-off (500°C/932°F) | Steam or manual cleaning |
Energy Consumption | High during cleaning cycle | Lower energy use |
Cost | Higher upfront cost | More affordable |
Maintenance | Minimal, self-cleaning | Requires manual scrubbing or steam cycles |
Ventilation Needs | Requires proper ventilation | Less stringent ventilation requirements |
Suitability | Ideal for high-end, modern kitchens | Better for budget-conscious or smaller kitchens |
Environmental Impact | High energy use, but fewer chemical cleaners | Lower energy use, eco-friendly options |
Still unsure if a pyrolytic oven is right for you? Contact our experts today for personalized advice!