Yes, a crucible can crack, and this is a common issue that can occur due to various operational and material-related factors. Crucibles are designed to withstand extreme temperatures and harsh chemical environments, but they are not immune to damage. The primary causes of cracking include improper heating and cooling cycles, rapid solidification of materials, and physical stresses. Regular inspection and proper handling are essential to prevent breakage and ensure the longevity of the crucible.
Key Points Explained:
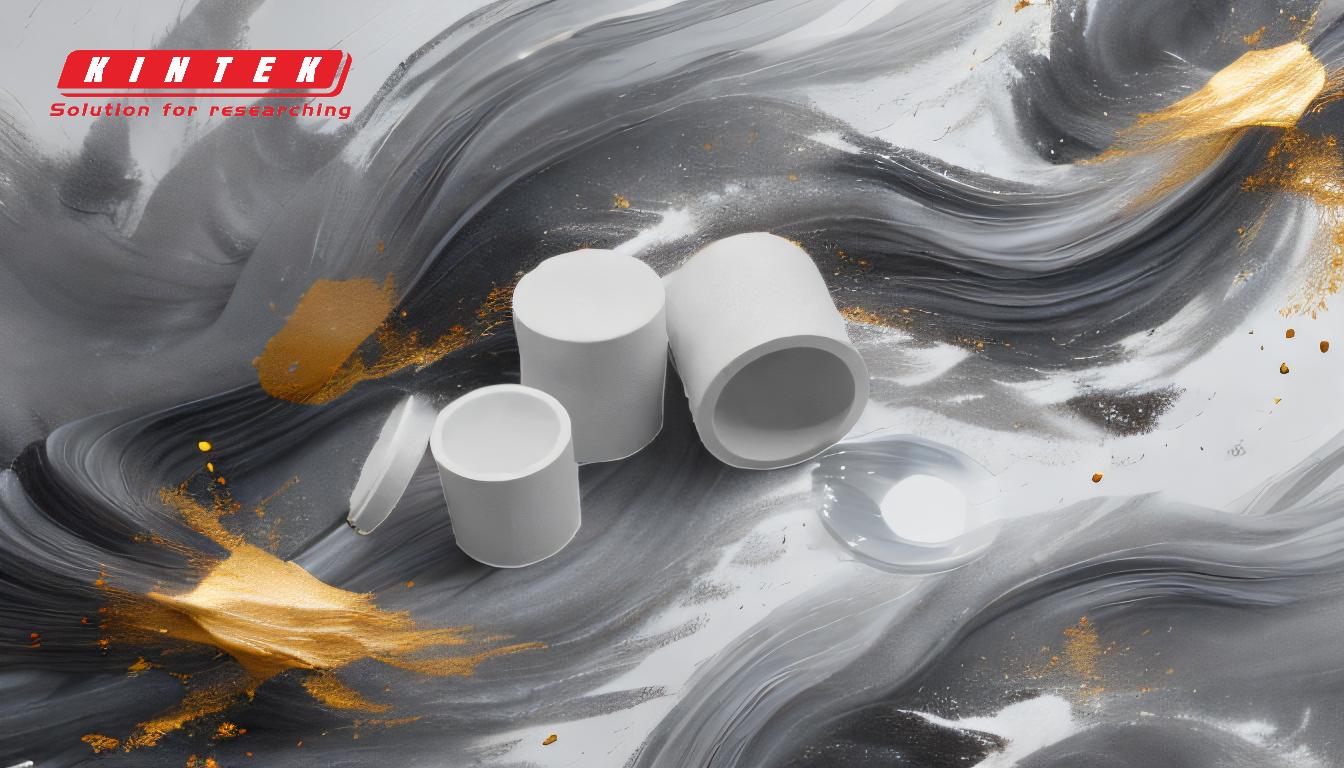
-
Causes of Crucible Cracking:
-
Incorrect Ramp/Soak Levels:
- Crucibles are often subjected to specific heating and cooling cycles, known as ramp/soak levels, which must be carefully controlled. Incorrect ramp/soak levels can cause thermal stress, leading to cracks. For example, heating or cooling the crucible too quickly can create uneven thermal expansion or contraction, which stresses the material and may result in cracking.
-
Improper Power Supply Shutdown or Short Ramp-Down Time:
- Abruptly shutting off the power supply or having a very short ramp-down time after deposition can cause the material inside the crucible to solidify rapidly. This rapid solidification creates internal stresses that can damage the crucible liner, leading to cracks or complete breakage.
-
Incorrect Ramp/Soak Levels:
-
Inspection and Testing for Cracks:
-
Auditory Testing:
- Before each use, crucibles should be tested for cracks. A common method is to gently tap the crucible with a soft hammer. A good ceramic crucible will produce a clear, ringing sound, while a damaged one will produce a dull "clunk" sound. This auditory test is a quick way to identify potential cracks.
-
Visual Inspection:
- Some operators prefer visual inspections to check for cracks. This involves closely examining the crucible for any visible signs of damage, such as hairline cracks, chips, or other imperfections. Visual inspection is particularly useful for identifying surface-level damage that might not be detected through auditory testing.
-
Auditory Testing:
-
Material Properties and Compatibility:
-
High-Temperature Resistance:
- Crucibles must be made from materials that can withstand extremely high temperatures without degrading. The material should have a melting point higher than the materials it contains to prevent melting or warping during use.
-
Chemical and Physical Stability:
- The crucible material must be chemically stable and resistant to reactions with the materials being melted. Chemical incompatibility can lead to deterioration of the crucible, contamination of the melt, and ultimately, cracking or breakage.
-
Thermal Shock Resistance:
- Crucibles should be able to withstand rapid changes in temperature without cracking. Materials with high thermal shock resistance are less likely to crack under the stress of rapid heating or cooling.
-
High-Temperature Resistance:
-
Preventive Measures:
-
Proper Heating and Cooling Cycles:
- To prevent cracking, it is crucial to follow the recommended heating and cooling cycles for the specific material being processed. This includes adhering to the correct ramp/soak levels and avoiding abrupt changes in temperature.
-
Gradual Power Supply Shutdown:
- When shutting down the power supply, it is important to allow for a gradual ramp-down time. This helps to prevent rapid solidification of the melt, which can stress the crucible and lead to cracking.
-
Regular Maintenance and Inspection:
- Regular maintenance and inspection of crucibles can help identify potential issues before they lead to breakage. This includes both auditory and visual inspections, as well as checking for any signs of wear or damage.
-
Proper Heating and Cooling Cycles:
In summary, while crucibles are designed to be durable, they can crack due to improper handling, thermal stress, and material incompatibility. Regular inspection, proper heating and cooling cycles, and careful handling are essential to prevent cracking and ensure the longevity of the crucible.
Summary Table:
Key Topic | Details |
---|---|
Causes of Cracking | - Incorrect ramp/soak levels |
- Improper power supply shutdown or short ramp-down time | |
Inspection Methods | - Auditory testing (ringing vs. dull sound) |
- Visual inspection for cracks or chips | |
Material Properties | - High-temperature resistance |
- Chemical and physical stability
- Thermal shock resistance | | Preventive Measures | - Proper heating/cooling cycles
- Gradual power supply shutdown
- Regular maintenance and inspection |
Need help selecting or maintaining crucibles? Contact our experts today for tailored solutions!