Yes, copper can be melted in an induction furnace. Induction furnaces are highly versatile and efficient, making them suitable for melting a variety of metals, including copper. They offer precise temperature control, uniform heating, and the ability to stir the molten metal, which are critical for achieving high-quality results in copper melting processes. Below, we will explore the key aspects of melting copper in an induction furnace, focusing on its suitability, advantages, and considerations.
Key Points Explained:
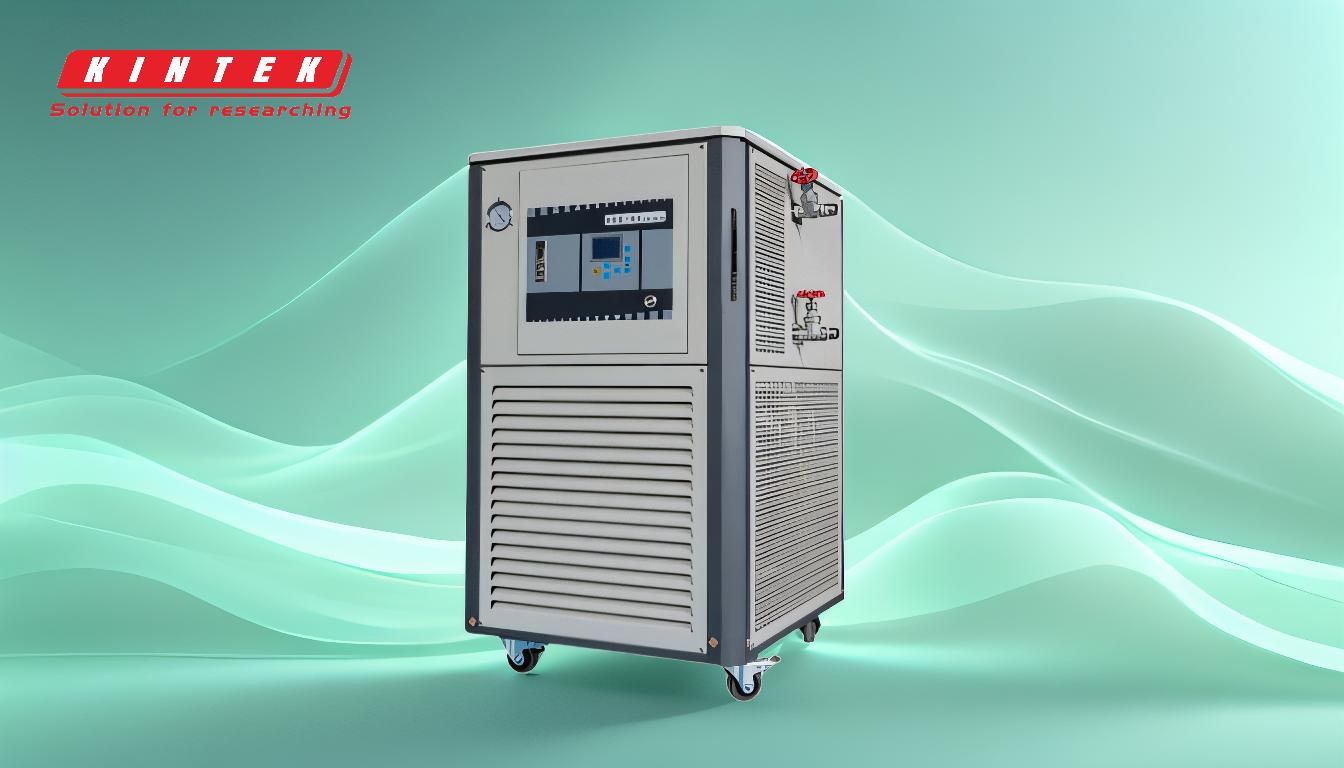
-
Suitability of Induction Furnaces for Copper Melting:
- Induction furnaces are specifically designed to handle a wide range of metals, including copper. The electromagnetic induction process generates heat directly within the metal, ensuring efficient and uniform melting.
- Copper's excellent electrical conductivity makes it particularly well-suited for induction heating, as it responds effectively to the electromagnetic fields generated by the furnace.
-
Advantages of Using an Induction Furnace for Copper Melting:
- Energy Efficiency: Induction furnaces are known for their high energy efficiency, as they directly heat the metal without significant heat loss to the surrounding environment.
- Precise Temperature Control: The ability to precisely control the temperature is crucial for copper melting, as it prevents overheating and ensures consistent quality.
- Uniform Heating and Stirring: The electromagnetic stirring action in an induction furnace ensures uniform mixing of the molten copper, which is essential for achieving homogeneity in the final product.
- Clean and Contamination-Free Melting: Induction furnaces operate without combustion, reducing the risk of contamination from gases or impurities.
-
Considerations for Melting Copper in an Induction Furnace:
- Furnace Design: The furnace must be designed to handle the specific requirements of copper, such as its melting point (1085°C) and thermal conductivity.
- Power Supply: Copper's high conductivity requires a robust power supply, such as an IGBT induction furnace, which can deliver the necessary power efficiently and reliably.
- Refractory Lining: The furnace's refractory lining must be compatible with copper to prevent chemical reactions or erosion during the melting process.
- Cooling System: Adequate cooling is essential to maintain the furnace's performance and longevity, especially when melting high-conductivity metals like copper.
-
Applications of Copper Melting in Induction Furnaces:
- Copper melted in induction furnaces is used in various industries, including electrical wiring, electronics, plumbing, and alloy production (e.g., brass and bronze).
- The ability to achieve high-purity copper with minimal impurities makes induction furnaces ideal for applications requiring superior electrical and thermal conductivity.
In conclusion, induction furnaces, particularly those powered by IGBT technology, are highly effective for melting copper. Their energy efficiency, precise control, and ability to produce high-quality molten copper make them a preferred choice for industrial applications. Proper design and operational considerations ensure optimal performance and longevity of the furnace when used for copper melting.
Summary Table:
Aspect | Details |
---|---|
Suitability | Designed for copper; efficient and uniform heating due to electromagnetic induction. |
Advantages | Energy-efficient, precise temperature control, uniform stirring, clean melting. |
Considerations | Proper furnace design, robust power supply (e.g., IGBT), compatible refractory lining, and cooling system. |
Applications | Electrical wiring, electronics, plumbing, and alloy production (e.g., brass, bronze). |
Ready to melt copper efficiently and precisely? Contact us today to find the perfect induction furnace for your needs!