Physical Vapor Deposition (PVD) can indeed be applied to aluminum, although it requires specific considerations due to the unique properties of aluminum and the requirements of the PVD process. PVD is a versatile coating technique used to enhance the surface properties of materials, including hardness, durability, and resistance to corrosion and wear. While aluminum is not explicitly listed among the most common materials for PVD coatings, it is a vacuum-compatible material that can be pre-treated to ensure proper adhesion and performance of the coating. The process involves creating a thin, dense film on the substrate surface, which can replicate the original finish of the material while significantly improving its mechanical and chemical properties. However, the high-temperature and vacuum requirements of PVD, along with the need for skilled operators and specialized equipment, make the process more complex and costly compared to other coating methods.
Key Points Explained:
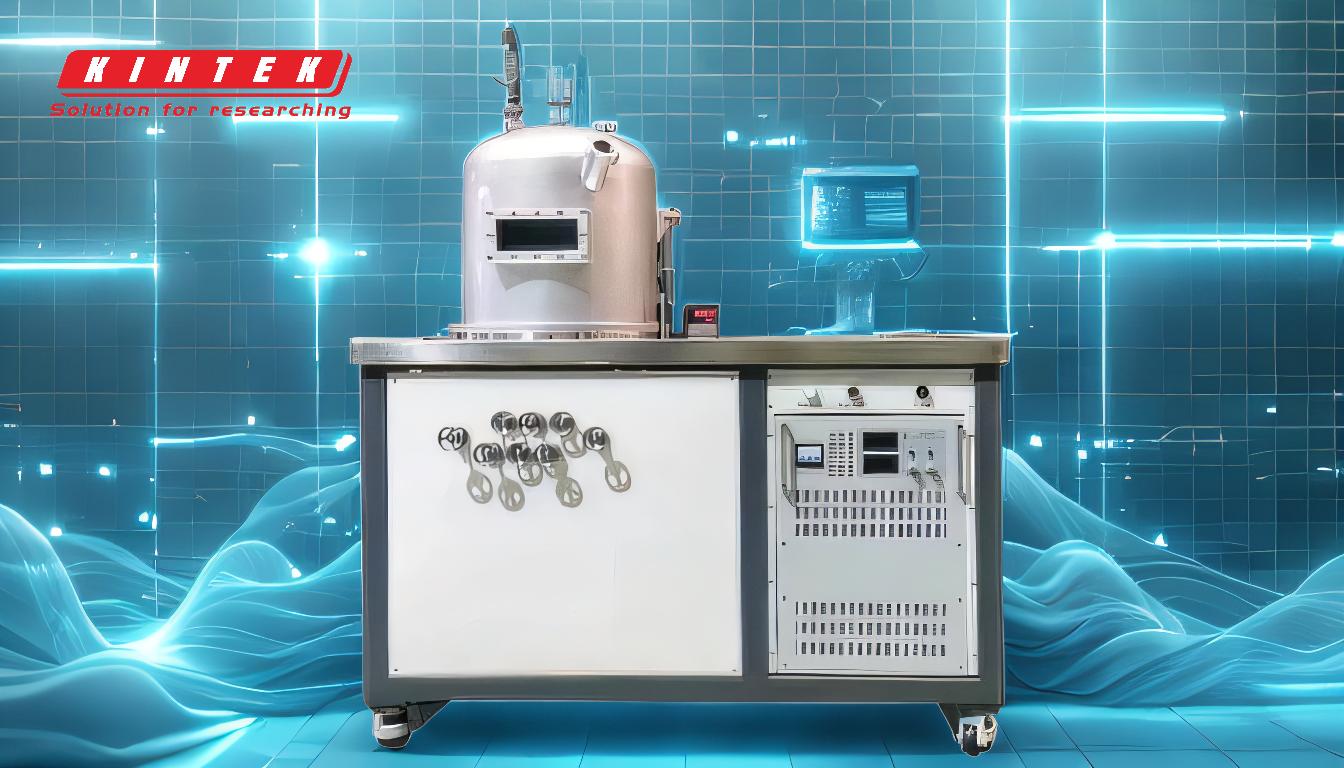
-
PVD Compatibility with Aluminum:
- Aluminum is vacuum-compatible, which is a prerequisite for PVD coating. However, it often requires pre-treatment, such as organic coatings or electroplating with materials like nickel or chromium, to improve adhesion and performance.
- The substrate material plays a critical role in determining the properties of the PVD coating. For aluminum, the coating can enhance its surface hardness, corrosion resistance, and durability.
-
Benefits of PVD Coating on Aluminum:
- Enhanced Durability: PVD coatings are four times harder than chrome, making them highly resistant to scratches and wear. This is particularly beneficial for aluminum components exposed to harsh environments or mechanical stress.
- Corrosion Resistance: PVD coatings provide excellent protection against corrosion and oxidation, which is crucial for aluminum, especially in coastal or industrial settings.
- Aesthetic Replication: The thin nature of PVD coatings (0.5 to 5 microns) allows them to replicate the original finish of aluminum with minimal effort, maintaining its appearance while improving functionality.
-
Challenges of Applying PVD to Aluminum:
- High-Temperature Requirements: PVD typically operates at high temperatures, which may affect the structural integrity of aluminum if not properly managed. Cooling systems are often required to dissipate heat during the process.
- Complexity and Cost: The need for a vacuum environment, skilled operators, and specialized equipment makes PVD a more complex and costly coating method compared to alternatives like electroplating or anodizing.
-
Applications of PVD-Coated Aluminum:
- Aerospace Industry: Aluminum components in aerospace applications benefit from PVD coatings due to their lightweight nature and enhanced durability.
- Decorative Coatings: PVD-coated aluminum is used in decorative applications, such as architectural elements or consumer products, where both aesthetics and performance are important.
- Cutting Tools and Industrial Components: While not as common as steel or titanium, aluminum tools and components can be PVD-coated to improve wear resistance and extend their lifespan.
-
Comparison with Other Coating Methods:
- Anodizing: Anodizing is a common method for aluminum but primarily improves corrosion resistance and surface hardness. PVD, on the other hand, offers superior hardness and wear resistance, along with a wider range of aesthetic options.
- Electroplating: Electroplating can provide a thicker coating but may not match the durability and thinness of PVD coatings. PVD is also more environmentally friendly, as it does not involve hazardous chemicals.
-
Technical Considerations:
- Adhesion: Proper surface preparation is critical to ensure strong adhesion between the PVD coating and the aluminum substrate. This may involve cleaning, etching, or applying intermediate layers.
- Coating Materials: Common PVD coating materials for aluminum include titanium nitride (TiN), chromium nitride (CrN), and aluminum oxide (Al2O3), each offering specific benefits such as increased hardness or improved corrosion resistance.
In summary, PVD can be successfully applied to aluminum, offering significant improvements in durability, corrosion resistance, and aesthetics. However, the process requires careful consideration of pre-treatment, temperature management, and cost factors to ensure optimal results.
Summary Table:
Aspect | Details |
---|---|
Compatibility | Aluminum is vacuum-compatible but requires pre-treatment for adhesion. |
Benefits | Enhanced durability, corrosion resistance, and aesthetic replication. |
Challenges | High-temperature requirements, complexity, and cost. |
Applications | Aerospace, decorative coatings, cutting tools, and industrial components. |
Comparison | Superior to anodizing and electroplating in hardness and environmental impact. |
Technical Considerations | Proper surface preparation and choice of coating materials (e.g., TiN, CrN). |
Ready to enhance your aluminum components with PVD coatings? Contact us today to learn more!