PVD (Physical Vapor Deposition) coatings are renowned for their durability, hardness, and resistance to wear, corrosion, and oxidation. Due to their strong adhesion to the substrate and extreme thinness (ranging from 0.5 to 5 microns), removing PVD coatings is challenging and typically requires specialized methods. While they do not fall off on their own, techniques such as mechanical abrasion, chemical etching, or laser ablation can be employed to remove them. However, these methods must be carefully applied to avoid damaging the underlying substrate. The removal process is complex and often depends on the specific coating material, substrate, and application requirements.
Key Points Explained:
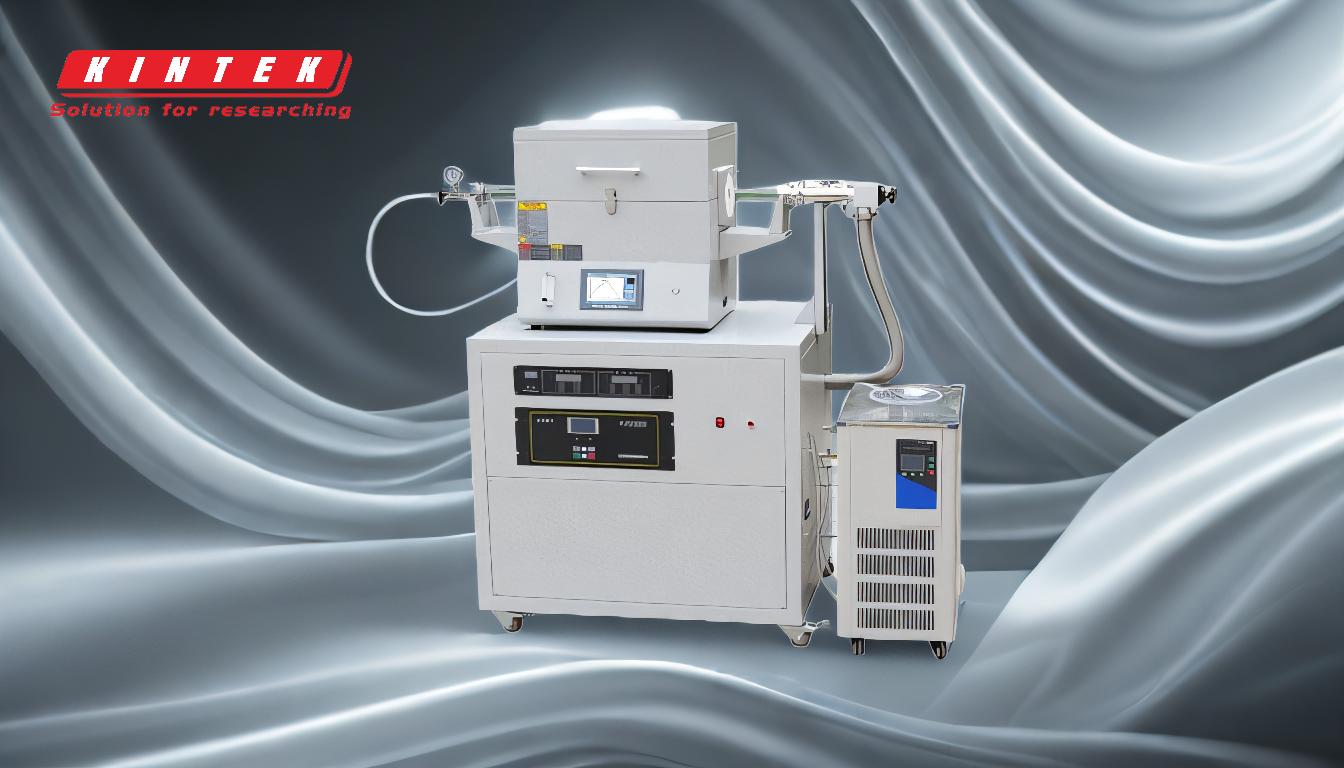
-
Durability and Adhesion of PVD Coatings
- PVD coatings are known for their exceptional hardness, wear resistance, and strong adhesion to the substrate.
- They are almost as hard as diamonds, making them highly resistant to scratching or spontaneous removal.
- The coatings are very thin (0.5 to 5 microns) and replicate the original finish of materials, which contributes to their durability.
-
Challenges in Removing PVD Coatings
- Due to their strong adhesion and hardness, PVD coatings do not fall off on their own and are difficult to remove.
- The extreme thinness of the coatings makes mechanical removal challenging without damaging the substrate.
- Chemical resistance and high-temperature stability further complicate the removal process.
-
Methods for Removing PVD Coatings
-
Mechanical Abrasion:
- Techniques like grinding, polishing, or sandblasting can be used to remove PVD coatings.
- However, these methods risk damaging the substrate if not performed carefully.
-
Chemical Etching:
- Specialized chemical solutions can dissolve or weaken the coating, but they must be chosen carefully to avoid harming the substrate.
- This method is often used in controlled industrial environments.
-
Laser Ablation:
- Laser technology can precisely remove PVD coatings without significantly affecting the substrate.
- This method is highly effective but requires specialized equipment and expertise.
-
Mechanical Abrasion:
-
Considerations for Substrate Protection
- The substrate material plays a critical role in determining the removal method.
- For example, softer substrates like aluminum or plastics require gentler techniques to avoid damage.
- The removal process must balance coating removal with preserving the integrity and functionality of the substrate.
-
Applications and Industry Implications
- PVD coatings are widely used in industries such as automotive, aerospace, and medical due to their durability and performance-enhancing properties.
- In some cases, the need to remove coatings arises during rework, repair, or recycling of components.
- Understanding the removal process is essential for industries that rely on PVD-coated components for critical applications.
-
Alternatives to Removal
- In some cases, recoating or refinishing the component may be more practical than removing the existing PVD coating.
- This approach can save time and resources while maintaining the component's performance characteristics.
In summary, while PVD coatings are highly durable and resistant to removal, specialized techniques such as mechanical abrasion, chemical etching, or laser ablation can be employed. The choice of method depends on the coating material, substrate, and application requirements, with careful consideration needed to avoid damaging the underlying material.
Summary Table:
Key Aspect | Details |
---|---|
Durability | Exceptional hardness, wear resistance, and strong adhesion to the substrate. |
Challenges in Removal | Strong adhesion, thinness (0.5-5 microns), and chemical resistance. |
Removal Methods | Mechanical abrasion, chemical etching, or laser ablation. |
Substrate Protection | Requires careful selection of methods to avoid damage. |
Applications | Automotive, aerospace, and medical industries. |
Need help removing PVD coatings? Contact our experts today for tailored solutions!