Pyrolysis can indeed be performed in a furnace, specifically a pyrolysis furnace, which is designed to thermally decompose organic materials in the absence of oxygen. This process is widely used in industrial applications to convert biomass, plastics, and other organic waste into valuable products such as bio-oil, gases, and char. The pyrolysis furnace operates under high temperatures and controlled conditions to ensure efficient decomposition while minimizing hazards. However, the process requires careful monitoring of parameters like temperature and pressure, as well as advanced control systems to maintain safe and optimal operations. Despite its benefits, challenges such as corrosion and high operational risks must be addressed to sustain long-term performance.
Key Points Explained:
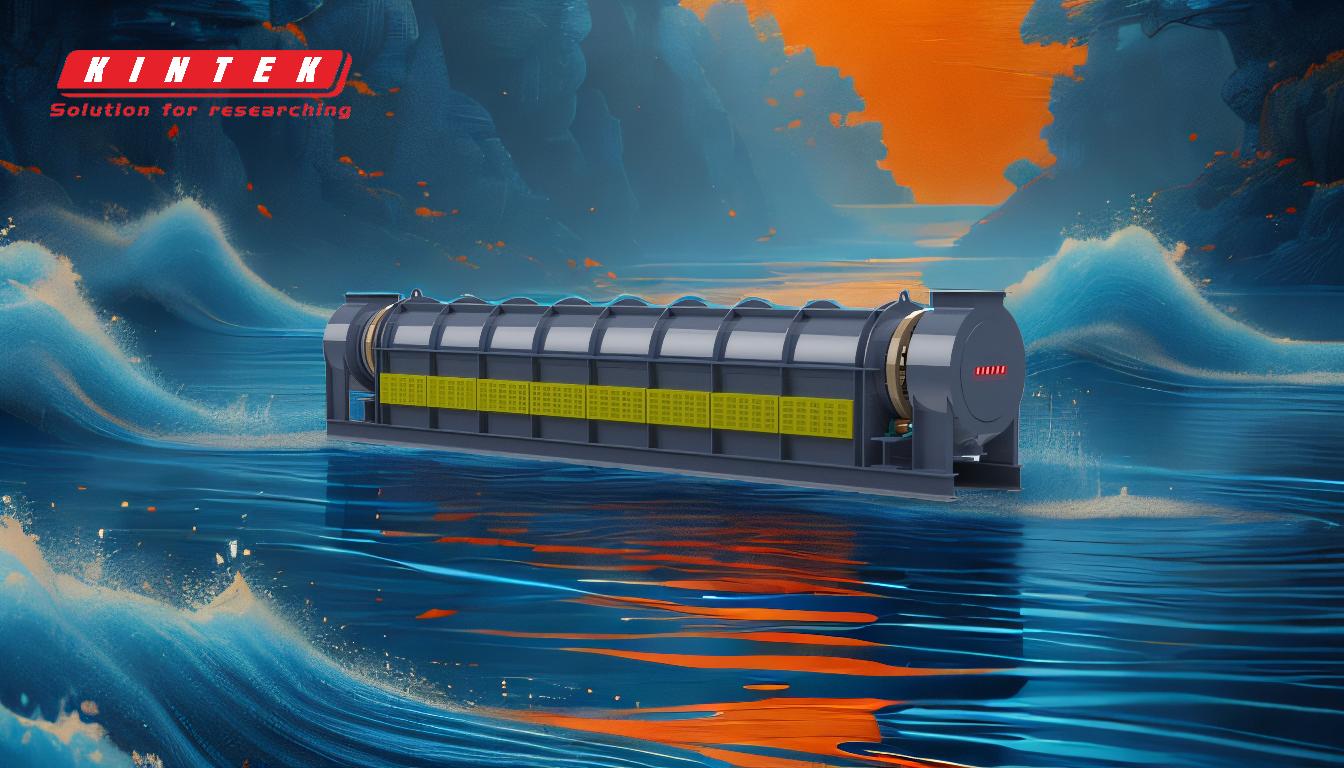
-
Pyrolysis in a Furnace:
- Pyrolysis is a thermal decomposition process that breaks down organic materials in the absence of oxygen. A pyrolysis furnace is specifically designed to facilitate this process, enabling the conversion of biomass, plastics, and other organic waste into useful products like bio-oil, syngas, and biochar.
- The furnace provides controlled conditions, including high temperatures and an oxygen-free environment, which are essential for efficient pyrolysis. This ensures that the organic materials decompose into their constituent components without combustion.
-
Industrial Benefits:
- Pyrolysis furnaces offer significant industrial benefits by transforming waste materials into valuable products. For example, bio-oil produced through pyrolysis can be upgraded and fractionated for use as transportation fuel or processed into specialty chemicals like adhesives.
- The process also contributes to waste management by reducing the volume of organic waste and converting it into usable energy or chemical feedstocks.
-
Operational Challenges:
- Operating a pyrolysis furnace involves high temperatures and pressures, which can pose significant hazards. Corrosion is a major challenge due to the harsh operating conditions, requiring regular maintenance and the use of corrosion-resistant materials.
- Safety is a critical concern, as the process involves flammable gases and high-energy reactions. Advanced control systems and predictive intelligence models are often employed to monitor and mitigate risks.
-
Control and Monitoring:
- Safe and efficient operation of a pyrolysis furnace relies on integrated control loops that monitor key parameters such as temperature, pressure, and gas composition. Visual monitoring and smart technologies are also used to detect and rectify issues in real time.
- Predictive maintenance and advanced analytics help optimize the process, ensuring consistent performance and minimizing downtime.
-
Applications and Stages:
- Pyrolysis furnaces can be used for various stages of biomass processing, including torrefaction (mild pyrolysis) and carbonization (complete pyrolysis). These stages produce different outputs, such as biochar and syngas, depending on the temperature and duration of the process.
- The versatility of pyrolysis furnaces makes them suitable for a wide range of applications, from energy production to chemical manufacturing.
-
Environmental and Economic Impact:
- Pyrolysis in a furnace supports sustainable practices by converting waste into valuable resources, reducing landfill use, and lowering greenhouse gas emissions. The production of bio-oil and other renewable products also contributes to the circular economy.
- Economically, pyrolysis furnaces offer a cost-effective solution for waste management and resource recovery, particularly in industries dealing with large volumes of organic waste.
In conclusion, pyrolysis can be effectively conducted in a furnace, offering numerous industrial and environmental benefits. However, the process requires careful management of operational challenges, advanced monitoring systems, and a focus on safety to ensure sustainable and efficient performance.
Summary Table:
Aspect | Details |
---|---|
Process | Thermal decomposition of organic materials in the absence of oxygen. |
Outputs | Bio-oil, syngas, and biochar. |
Industrial Benefits | Converts waste into valuable products; reduces landfill use. |
Operational Challenges | High temperatures, corrosion risks, and safety concerns. |
Control & Monitoring | Advanced systems for temperature, pressure, and gas composition monitoring. |
Applications | Energy production, chemical manufacturing, and waste management. |
Environmental Impact | Reduces greenhouse gas emissions and supports the circular economy. |
Ready to explore how a pyrolysis furnace can transform your waste into valuable resources? Contact us today to learn more!