Pyrolysis oil, also known as bio-oil, is a complex mixture of oxygenated organic compounds produced through the pyrolysis of biomass. While it has potential as a renewable fuel, its high oxygen content, acidity, and instability make it unsuitable for direct use in conventional engines or fuel systems. However, pyrolysis oil can indeed be refined and upgraded to improve its quality and make it more compatible with existing fuel infrastructure. The refining process primarily focuses on reducing oxygen content, stabilizing the oil, and enhancing its energy density. Below, we explore the key aspects of refining pyrolysis oil, including the methods, challenges, and applications of upgraded bio-oil.
Key Points Explained:
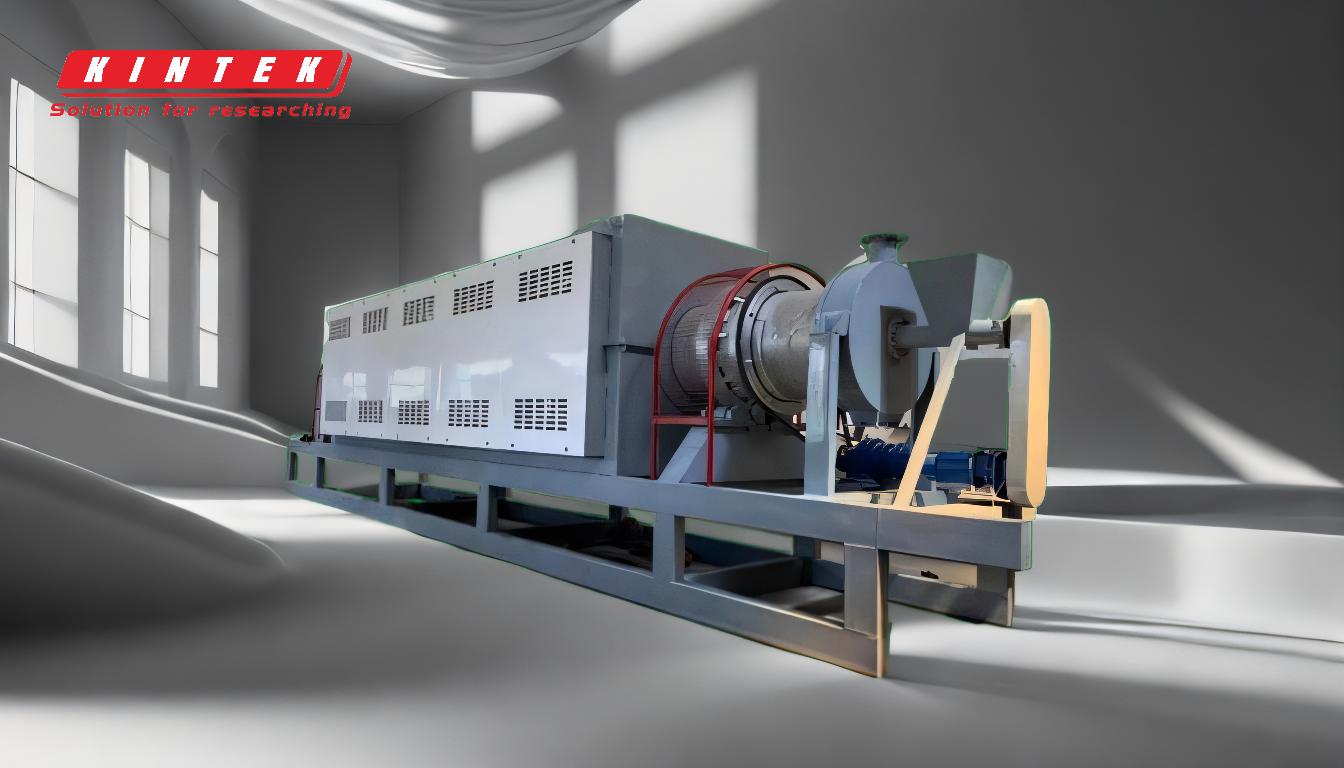
-
Why Refining Pyrolysis Oil is Necessary
- Pyrolysis oil contains high levels of oxygen (up to 40% by weight), which leads to low energy density, high acidity, and poor thermal stability.
- The presence of oxygenated compounds, such as acids, aldehydes, and phenols, makes the oil corrosive and unstable during storage or transportation.
- Refining aims to reduce oxygen content, improve stability, and enhance compatibility with existing fuel systems.
-
Key Refining Methods
- Hydrodeoxygenation (HDO): This process involves treating pyrolysis oil with hydrogen at high temperatures and pressures in the presence of a catalyst. HDO removes oxygen in the form of water, producing a more stable and energy-dense hydrocarbon fuel.
- Catalytic Cracking: This method uses catalysts to break down large oxygenated molecules into smaller, more stable hydrocarbons. It can be combined with HDO for better results.
- Esterification and Acetylation: These chemical processes convert acidic components in bio-oil into esters or acetates, reducing acidity and improving stability.
- Steam Reforming: This process converts pyrolysis oil into syngas (a mixture of hydrogen and carbon monoxide), which can then be used to produce synthetic fuels or chemicals.
-
Challenges in Refining Pyrolysis Oil
- High Cost: Refining processes like HDO require significant energy input, expensive catalysts, and specialized equipment, making them costly.
- Catalyst Deactivation: The high oxygen and impurity content in pyrolysis oil can deactivate catalysts, reducing their effectiveness over time.
- Complex Composition: The diverse range of compounds in pyrolysis oil makes it difficult to develop a one-size-fits-all refining solution.
- Scalability: Many refining methods are still in the experimental or pilot stage and have not been widely adopted on an industrial scale.
-
Applications of Refined Pyrolysis Oil
- Transportation Fuels: Upgraded pyrolysis oil can be blended with conventional fuels like diesel or gasoline, or used as a standalone fuel in modified engines.
- Heating Oil: Refined bio-oil can be used as a cleaner alternative to traditional heating oils in industrial or residential settings.
- Chemical Feedstock: The hydrocarbons produced during refining can serve as raw materials for the production of plastics, solvents, and other chemicals.
- Power Generation: Upgraded pyrolysis oil can be used in gas turbines or boilers to generate electricity.
-
Future Prospects and Research Directions
- Catalyst Development: Researchers are working on developing more efficient and durable catalysts to reduce costs and improve refining efficiency.
- Integrated Processes: Combining pyrolysis with refining steps in a single, continuous process could enhance efficiency and reduce costs.
- Co-Processing: Refining pyrolysis oil alongside petroleum-derived feedstocks in existing refineries could lower costs and accelerate adoption.
- Sustainability: Efforts are underway to ensure that the entire lifecycle of pyrolysis oil production and refining is environmentally sustainable.
In conclusion, pyrolysis oil can indeed be refined through various methods, such as hydrodeoxygenation, catalytic cracking, and esterification. While challenges like high costs and catalyst deactivation remain, ongoing research and technological advancements are paving the way for more efficient and scalable refining processes. Upgraded pyrolysis oil has the potential to serve as a renewable fuel and chemical feedstock, contributing to a more sustainable energy future.
Summary Table:
Aspect | Details |
---|---|
Why Refine? | High oxygen content, acidity, and instability make raw pyrolysis oil unsuitable for direct use. |
Key Methods | Hydrodeoxygenation (HDO), catalytic cracking, esterification, steam reforming. |
Challenges | High costs, catalyst deactivation, complex composition, scalability issues. |
Applications | Transportation fuels, heating oil, chemical feedstock, power generation. |
Future Prospects | Catalyst development, integrated processes, co-processing, sustainability. |
Discover how refined pyrolysis oil can transform your energy solutions—contact us today to learn more!