Stainless steel can indeed be sintered, and the process is widely used in various industries to create complex and durable components. Sintering involves compacting powdered stainless steel and then heating it to a temperature below its melting point, allowing the particles to bond through atomic diffusion. This method is particularly advantageous for producing parts with intricate geometries, high strength, and excellent corrosion resistance. The sintering process is compatible with stainless steel due to its ability to form strong metallurgical bonds without reaching the melting point, making it a preferred choice for applications requiring precision and durability.
Key Points Explained:
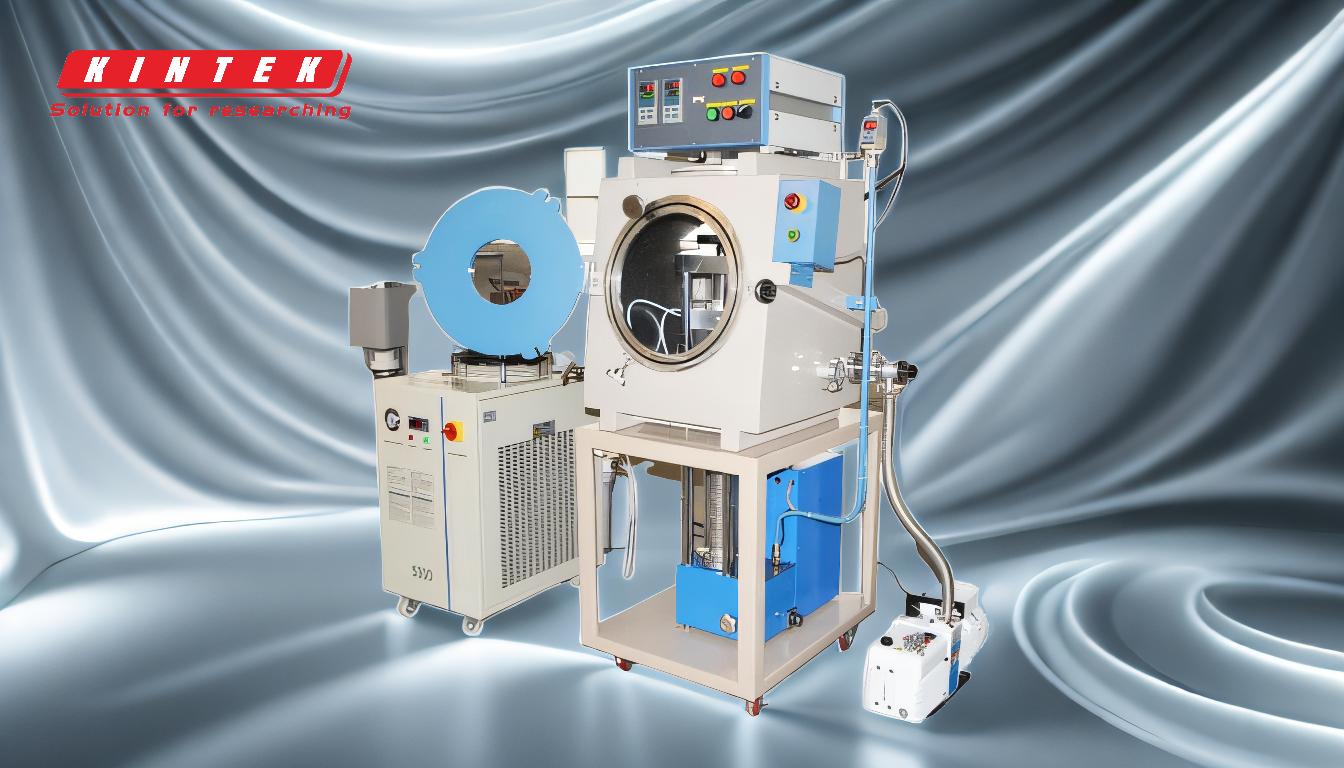
-
What is Sintering?
- Sintering is a manufacturing process that compacts powdered materials into a solid mass by applying heat or pressure without melting the material to a liquid state. This process relies on atomic diffusion, where atoms move across particle boundaries, fusing them together into a cohesive structure.
-
Why Stainless Steel is Suitable for Sintering
- Stainless steel is an ideal candidate for sintering due to its high melting point and ability to form strong metallurgical bonds at elevated temperatures. The process allows for the creation of complex shapes and components with excellent mechanical properties, such as high strength, corrosion resistance, and durability.
-
Steps in the Sintering Process for Stainless Steel
- Powder Preparation: Stainless steel powder is carefully selected and prepared to ensure uniformity in particle size and composition.
- Compaction: The powder is compacted into the desired shape using a die and high pressure. This step ensures the powder particles are in close contact, facilitating bonding during sintering.
- Sintering: The compacted part is heated in a controlled atmosphere (often inert or reducing) to a temperature below the melting point of stainless steel. During this stage, atomic diffusion occurs, bonding the particles together.
- Post-Processing: After sintering, the part may undergo additional treatments, such as machining, polishing, or heat treatment, to achieve the desired final properties.
-
Advantages of Sintering Stainless Steel
- Complex Geometries: Sintering allows for the production of intricate shapes that would be difficult or impossible to achieve with traditional machining or casting.
- Material Efficiency: The process minimizes material waste, as the powder can be reused or recycled.
- High Strength and Durability: Sintered stainless steel parts exhibit excellent mechanical properties, making them suitable for demanding applications.
- Corrosion Resistance: Stainless steel retains its corrosion-resistant properties after sintering, making it ideal for use in harsh environments.
-
Applications of Sintered Stainless Steel
- Sintered stainless steel is used in a wide range of industries, including automotive, aerospace, medical, and consumer goods. Common applications include filters, bearings, gears, and structural components that require high strength and resistance to wear and corrosion.
-
Challenges and Considerations
- While sintering stainless steel offers many benefits, it also presents challenges, such as controlling the sintering atmosphere to prevent oxidation and ensuring uniform density throughout the part. Proper process control and material selection are critical to achieving high-quality sintered stainless steel components.
In summary, sintering is a highly effective method for producing stainless steel parts with complex geometries and excellent mechanical properties. The process leverages the material's inherent strengths, making it a versatile and reliable choice for various industrial applications.
Summary Table:
Aspect | Details |
---|---|
What is Sintering? | Compacting powdered materials using heat/pressure without melting. |
Why Stainless Steel? | High melting point, strong bonds, and excellent mechanical properties. |
Process Steps | Powder Preparation → Compaction → Sintering → Post-Processing |
Advantages | Complex geometries, material efficiency, high strength, corrosion resistance |
Applications | Automotive, aerospace, medical, consumer goods (filters, bearings, gears). |
Challenges | Controlling atmosphere, ensuring uniform density, proper material selection. |
Ready to explore sintered stainless steel solutions for your industry? Contact our experts today to get started!