PVD (Physical Vapor Deposition) coatings are known for their durability, corrosion resistance, and aesthetic versatility. While PVD coatings bond at a micron level to the substrate, altering the surface properties without adding a significant layer, the question arises whether ceramic coatings can be applied over PVD. Ceramic coatings, often used for additional protection and enhanced surface properties, are typically applied to metals or other substrates. However, applying ceramic coatings over PVD requires careful consideration of the adhesion, compatibility, and thermal properties of both materials. The process is feasible but depends on the specific materials and application requirements.
Key Points Explained:
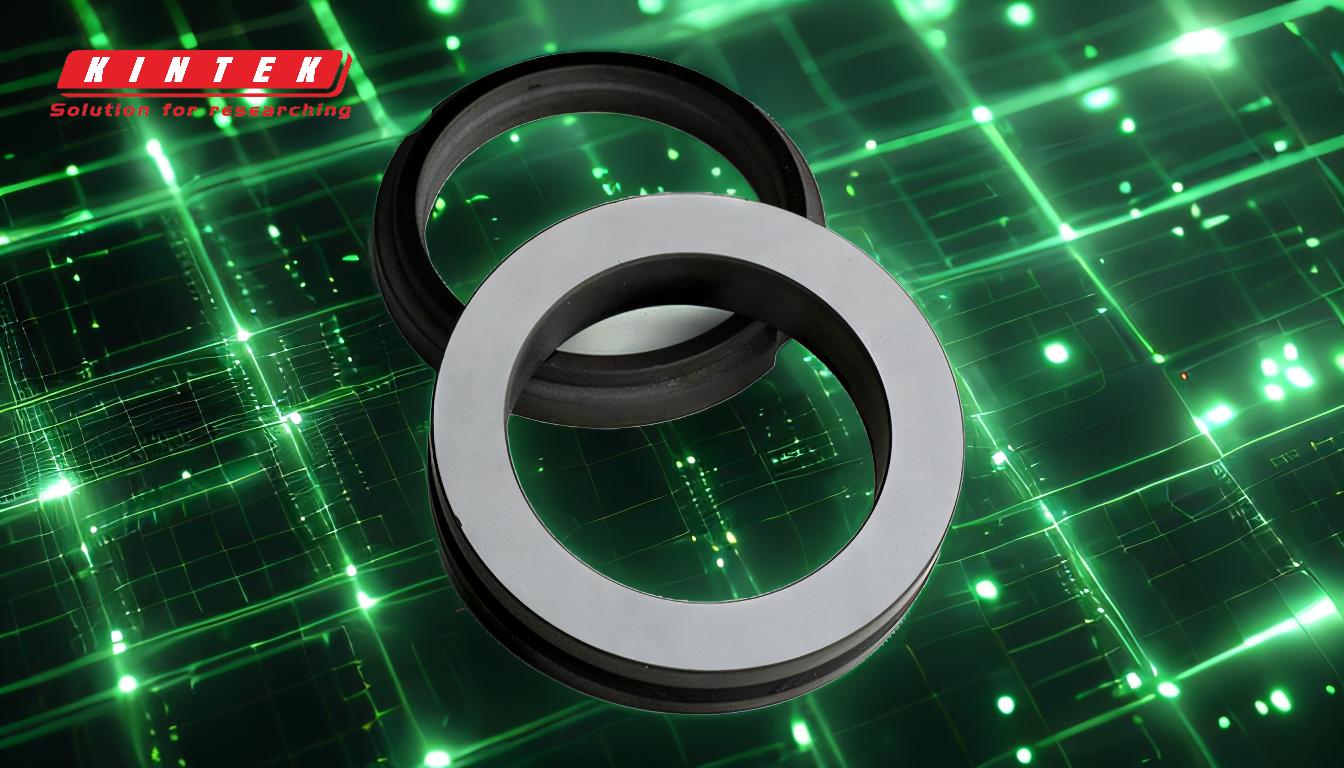
-
Understanding PVD Coatings:
- PVD coatings are applied in a vacuum chamber under low pressure, involving evaporation, transportation, and condensation of the coating material.
- They bond at a micron level to the substrate, altering the surface properties rather than adding a thick layer.
- PVD coatings are known for their durability, corrosion resistance, and ability to enhance the lifespan of products.
-
Ceramic Coatings Overview:
- Ceramic coatings are typically used to provide additional protection, such as thermal insulation, scratch resistance, and chemical resistance.
- They are often applied to metals, ceramics, or other substrates to enhance surface properties.
-
Feasibility of Ceramic Coating Over PVD:
- Applying ceramic coatings over PVD is possible but requires careful consideration of adhesion and compatibility.
- The thin, bonded nature of PVD coatings means that the ceramic coating must adhere well to the altered surface properties of the PVD layer.
- Thermal expansion and contraction properties of both materials must be compatible to avoid delamination or cracking.
-
Process Considerations:
- Surface preparation is critical. The PVD-coated surface must be clean and free of contaminants to ensure proper adhesion of the ceramic coating.
- The application method for the ceramic coating (e.g., spraying, dipping, or thermal spraying) must be chosen based on the specific PVD-coated material and desired outcome.
- Curing or sintering temperatures for the ceramic coating should not exceed the thermal stability limits of the PVD coating.
-
Applications and Benefits:
- Combining ceramic coatings with PVD can enhance the overall performance of the product, such as increased wear resistance, thermal protection, and improved aesthetics.
- This combination is particularly useful in industries like aerospace, automotive, and medical devices, where both durability and surface properties are critical.
-
Challenges and Limitations:
- Adhesion issues may arise if the ceramic coating does not bond well with the PVD layer.
- Thermal mismatch between the two materials can lead to stress and potential failure during thermal cycling.
- The process may require specialized equipment and expertise, increasing costs and complexity.
In conclusion, while ceramic coatings can be applied over PVD, the process requires careful planning and execution to ensure compatibility and durability. The combination of these two advanced coating technologies can offer significant benefits, but it is essential to address the challenges to achieve optimal results.
Summary Table:
Aspect | Details |
---|---|
PVD Coating Properties | Durable, corrosion-resistant, micron-level bonding, enhances surface properties |
Ceramic Coating Role | Adds thermal insulation, scratch resistance, and chemical protection |
Feasibility | Possible with proper adhesion, compatibility, and thermal property alignment |
Key Considerations | Surface preparation, application method, curing temperature limits |
Applications | Aerospace, automotive, medical devices for enhanced durability and aesthetics |
Challenges | Adhesion issues, thermal mismatch, specialized equipment and expertise needed |
Ready to enhance your product's performance with ceramic-coated PVD? Contact our experts today for tailored solutions!