Yes, aluminum can be melted in an induction furnace, and it is a widely used method due to its efficiency and ability to produce high-quality aluminum alloys. Induction furnaces, particularly those using IGBT (Insulated Gate Bipolar Transistor) technology, are well-suited for melting aluminum because they provide precise temperature control, reduce oxidation losses, and ensure uniform heating. However, there are specific considerations and steps to ensure safe and efficient operation, such as proper equipment setup, maintenance, and understanding the unique challenges of melting aluminum.
Key Points Explained:
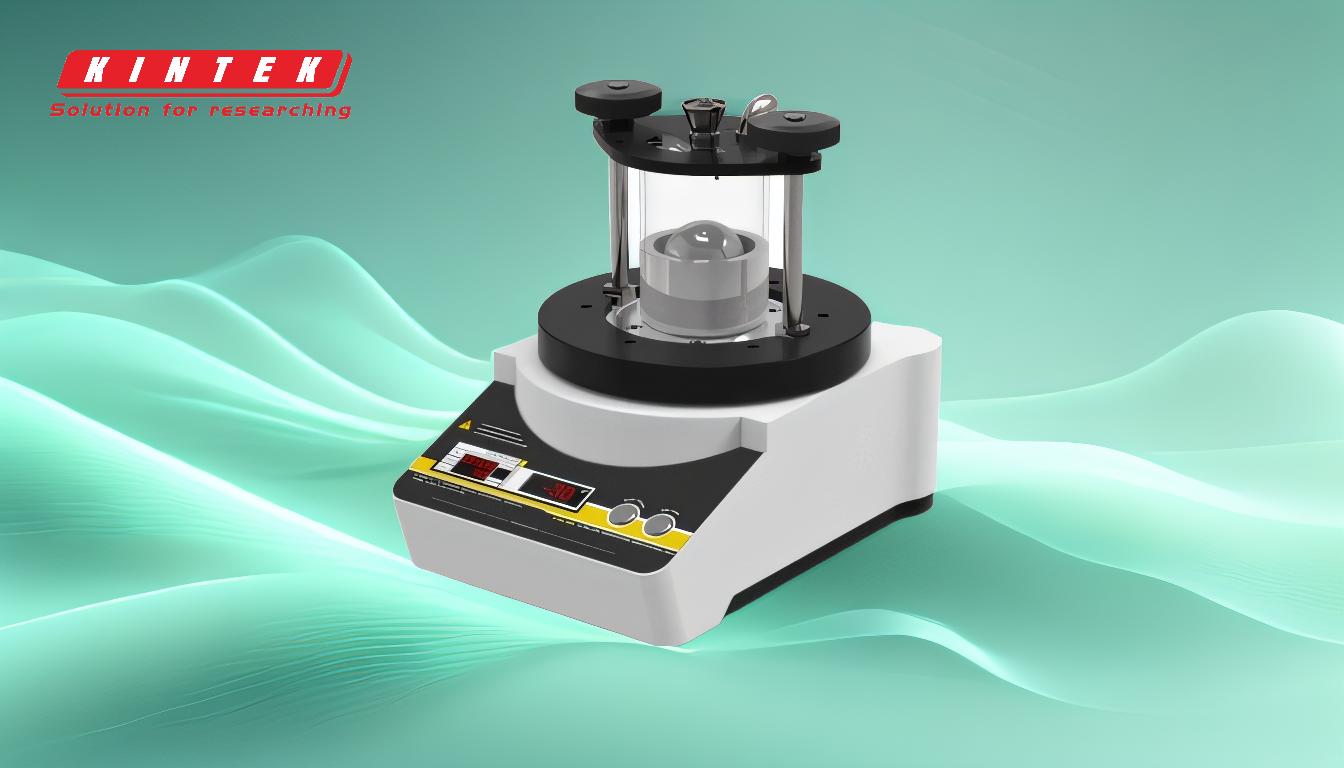
-
Feasibility of Melting Aluminum in an Induction Furnace:
- Aluminum can be melted in an induction furnace, and it is a preferred method for producing high-quality aluminum alloys. The induction furnace's ability to provide uniform heating and precise temperature control makes it ideal for melting aluminum.
- The igbt induction furnace is particularly suitable for this purpose due to its efficiency and ability to handle the unique properties of aluminum.
-
Equipment Setup and Operation:
- Before starting the melting process, ensure that the waterway and all equipment parts are functioning correctly. Turn on the filaments sequentially, waiting five minutes between each, and then apply high voltage. Always start with the output adjustment potentiometer at the minimum setting to avoid sudden power surges.
- The input voltage required is three-phase 380V with a three-phase five-wire power supply. Ensure all electrical connections are secure and avoid touching power supply and transformer connectors when the machine is powered on.
-
Challenges in Melting Aluminum:
- During the early stages of melting, a large eddy current is generated, and the irregular distribution of the charge can cause strong impacts on the power supply. This can lead to the burnout of thyristors if not properly managed. Therefore, the design of the intermediate-frequency power supply must account for impact resistance.
- Crucible induction furnaces, while effective, have a maximum capacity of 8-10 tonnes, making them unsuitable for large-scale production. They are typically used for remelting fine aluminum chips and require significant capital investment and maintenance.
-
Components of an Aluminum Melting Induction Furnace:
- The main components include the intermediate frequency power supply (with a frequency of 2500HZ), compensation capacitor, furnace body, water-cooled cable, and reducer. These components work together to ensure efficient and uniform heating of the aluminum.
-
Advantages of Using an Induction Furnace for Aluminum:
- Induction melting furnaces offer a 60 to 75% rate of efficiency, significantly reducing losses due to oxidation. They produce low emissions and ensure a high degree of purity and uniformity in the end product.
- The heat source does not come into direct contact with the aluminum, and the electrical field stirs the molten metal, making it ideal for producing aluminum alloys.
-
Maintenance and Safety Considerations:
- After each shift, remove water from the equipment using an air gun and clean dust and debris to prevent rust and scale. Ensure the cooling water quality is good and avoid heating the coil without water.
- Maintain the equipment in a suitable environment, away from direct sunlight, rain, and humidity, to prolong its lifespan and ensure safe operation.
In summary, melting aluminum in an induction furnace is not only feasible but also advantageous due to the efficiency, purity, and uniformity it offers. Proper setup, operation, and maintenance are crucial to overcoming the challenges associated with melting aluminum and ensuring safe and efficient production.
Summary Table:
Key Aspect | Details |
---|---|
Feasibility | Aluminum can be melted in an induction furnace, especially with IGBT technology. |
Setup | Requires three-phase 380V power supply, proper waterway checks, and sequential filament activation. |
Challenges | Large eddy currents and irregular charge distribution can impact power supply. |
Components | Includes intermediate frequency power supply, capacitor, furnace body, and water-cooled cable. |
Advantages | 60-75% efficiency, low oxidation losses, high purity, and uniform heating. |
Maintenance | Regular cleaning, water removal, and proper environmental conditions are essential. |
Ready to optimize your aluminum melting process? Contact our experts today for tailored solutions!