Ceramics are generally known for their chemical inertness and resistance to reactions with many substances, but they are not entirely unreactive. Depending on their composition and structure, ceramics can react with certain chemicals, extreme temperatures, or mechanical stresses. For example, some ceramics may react with strong acids, bases, or molten metals, while others may degrade under high thermal or mechanical stress. The reactivity of ceramics is highly dependent on their specific material properties, such as purity, porosity, and crystalline structure. Understanding these factors is crucial when selecting ceramics for specific applications, especially in environments where chemical or thermal stability is required.
Key Points Explained:
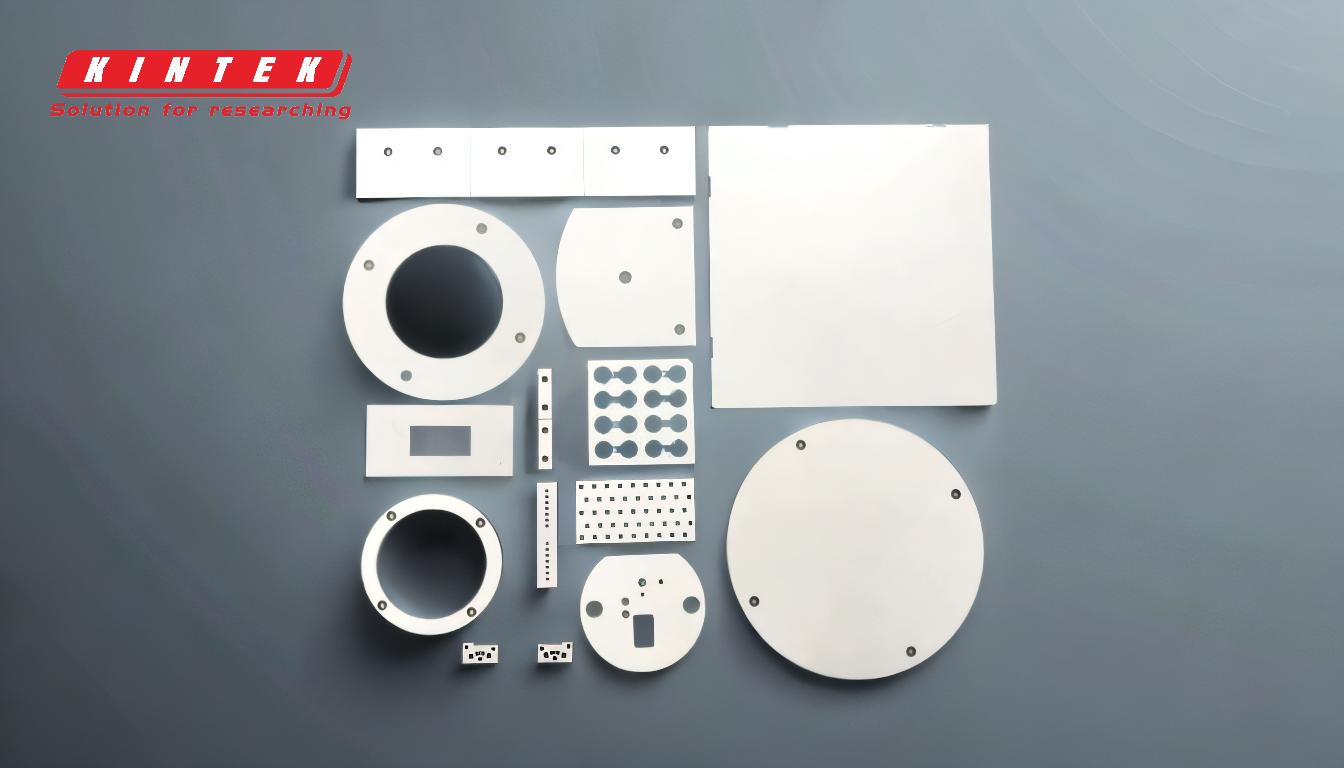
-
Chemical Inertness of Ceramics:
- Ceramics are typically chemically inert, meaning they do not readily react with most substances. This property makes them suitable for use in harsh chemical environments, such as in laboratory equipment or chemical processing industries.
- However, certain ceramics, especially those with impurities or porous structures, may react with strong acids, bases, or oxidizing agents. For example, alumina ceramics are resistant to most acids but can be attacked by hydrofluoric acid.
-
Reactivity with Acids and Bases:
- Strong acids (e.g., sulfuric acid, hydrochloric acid) and bases (e.g., sodium hydroxide) can degrade some ceramics, particularly those with lower chemical resistance. For instance, silica-based ceramics may dissolve in strong alkaline solutions.
- The reactivity depends on the ceramic's composition. Advanced ceramics like silicon carbide or silicon nitride are highly resistant to acids and bases, while traditional ceramics like clay-based materials may be more susceptible.
-
Reactivity with Molten Metals:
- Ceramics are often used in high-temperature applications, such as crucibles for molten metals. However, some ceramics can react with molten metals, leading to corrosion or degradation. For example, alumina ceramics may react with molten aluminum at very high temperatures.
- The choice of ceramic for such applications must consider the specific metal and operating conditions to avoid unwanted reactions.
-
Thermal and Mechanical Stress:
- Ceramics are generally resistant to high temperatures, but thermal shock (rapid temperature changes) can cause cracking or failure. This is due to the brittleness of ceramics and their low thermal conductivity.
- Mechanical stress, such as impact or abrasion, can also lead to fractures or wear, especially in ceramics with low toughness. This is not a chemical reaction but a physical degradation process.
-
Environmental Factors:
- In certain environments, such as those with high humidity or corrosive gases, ceramics may undergo slow degradation. For example, some ceramics may react with water vapor or sulfur dioxide over time.
- The presence of impurities or defects in the ceramic structure can accelerate these reactions.
-
Applications and Material Selection:
- When selecting ceramics for specific applications, it is essential to consider the chemical and thermal environment they will be exposed to. For example, in the semiconductor industry, high-purity alumina ceramics are chosen for their excellent chemical resistance and electrical insulation properties.
- Advanced ceramics like zirconia or silicon nitride are often preferred for applications requiring high strength, wear resistance, and thermal stability.
-
Summary of Reactivity:
- Ceramics are generally unreactive with most substances, but their reactivity depends on their composition, structure, and environmental conditions. Understanding these factors is critical for ensuring the longevity and performance of ceramic components in various applications.
By carefully considering the specific properties and potential reactivity of ceramics, users can make informed decisions when selecting materials for their intended applications.
Summary Table:
Factor | Reactivity Details |
---|---|
Chemical Inertness | Generally inert but can react with strong acids, bases, or oxidizing agents. |
Acids & Bases | Susceptible to degradation from strong acids (e.g., sulfuric acid) and bases. |
Molten Metals | May react with molten metals, leading to corrosion or degradation. |
Thermal Stress | Prone to cracking under rapid temperature changes due to brittleness. |
Mechanical Stress | Can fracture or wear under impact or abrasion. |
Environmental Factors | Degrades slowly in humid or corrosive environments, especially with impurities. |
Applications | Advanced ceramics (e.g., silicon carbide, zirconia) preferred for harsh environments. |
Need help selecting the right ceramic for your application? Contact our experts today!