PVD (Physical Vapor Deposition) coatings are renowned for their durability and resistance to scratches, corrosion, and wear. These coatings are super-hard, making them far more durable than traditional finishes. Their hardness, combined with excellent abrasion resistance, ensures that PVD coatings are highly resistant to scratching. Additionally, their thinness (ranging from 0.5 to 5 microns) and strong adhesion to the substrate further enhance their scratch resistance. PVD coatings are widely used in demanding applications where durability and longevity are critical, making them a reliable choice for industries requiring high-performance surface finishes.
Key Points Explained:
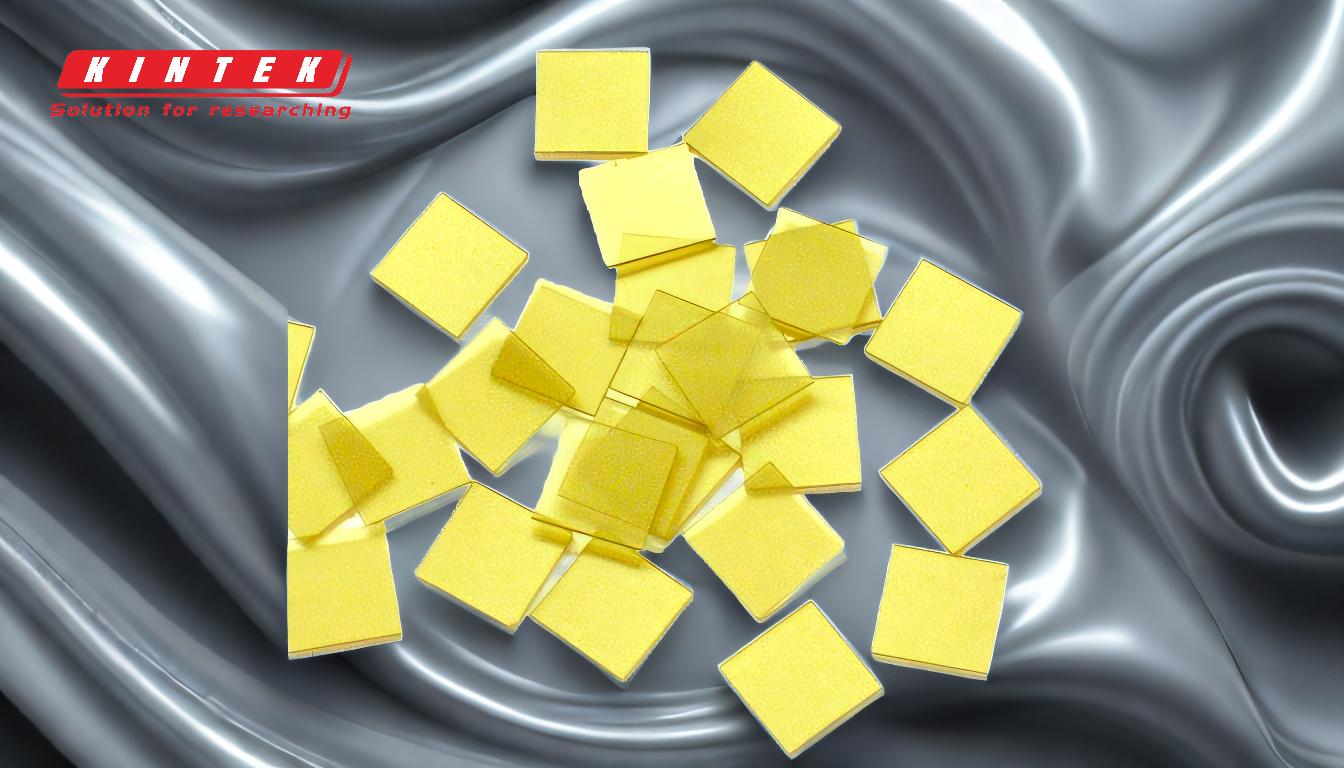
-
Super-Hard Nature of PVD Coatings:
- PVD coatings are classified as super-hard coatings, which means they are significantly harder than traditional finishes. This hardness is a key factor in their scratch resistance.
- The hardness of the coating material, such as TiN (Titanium Nitride), contributes to its ability to withstand mechanical stresses and abrasion without scratching easily.
-
Abrasion Resistance:
- PVD coatings exhibit excellent abrasion resistance, which directly correlates to their ability to resist scratches. This property is particularly important in high-wear environments.
- The robust abrasion resistance ensures that the coating maintains its integrity even under repeated friction or contact with hard surfaces.
-
Thinness and Adhesion:
- PVD coatings are extremely thin, ranging from 0.5 to 5 microns. Despite their thinness, they adhere strongly to the substrate, making them difficult to remove or damage.
- The strong adhesion ensures that the coating remains intact even under mechanical stress, further enhancing its scratch resistance.
-
Durability in Demanding Applications:
- PVD coatings are designed for use in demanding applications where durability is critical. Their resistance to scratches, corrosion, and wear makes them suitable for industries such as aerospace, automotive, and medical devices.
- The coatings' ability to withstand harsh conditions without degrading ensures long-lasting performance.
-
Comparison with Traditional Finishes:
- PVD coatings outperform traditional finishes in terms of durability and scratch resistance. They are considered the most durable coating available today, offering superior quality and longevity.
- Traditional finishes, such as electroplating or painting, are more prone to scratching and wear compared to PVD coatings.
-
Resistance to Corrosion and Oxidation:
- In addition to scratch resistance, PVD coatings are highly resistant to corrosion and oxidation. This dual resistance makes them ideal for use in environments where both mechanical and chemical stresses are present.
- The combination of scratch resistance and corrosion resistance ensures that the coating remains functional and aesthetically pleasing over time.
-
Replication of Original Finish:
- PVD coatings can replicate the original finish of materials with minimal effort, maintaining the aesthetic appeal while enhancing durability.
- This property is particularly useful in applications where both appearance and performance are important, such as in decorative hardware or consumer electronics.
In summary, PVD coatings are highly resistant to scratching due to their super-hard nature, excellent abrasion resistance, strong adhesion, and thinness. These properties make them a superior choice for applications requiring durable and long-lasting surface finishes.
Summary Table:
Property | Description |
---|---|
Super-Hard Nature | Significantly harder than traditional finishes, enhancing scratch resistance. |
Abrasion Resistance | Excellent resistance to wear, maintaining integrity under friction. |
Thinness & Adhesion | Thin (0.5–5 microns) yet strongly adheres to substrates, preventing damage. |
Durability | Designed for demanding applications like aerospace and medical devices. |
Corrosion Resistance | Highly resistant to corrosion and oxidation, ensuring long-lasting performance. |
Aesthetic Replication | Replicates original finishes while enhancing durability. |
Upgrade your materials with PVD coatings for unmatched durability—contact us today to learn more!