PVD (Physical Vapor Deposition) coatings are renowned for their durability, versatility, and high performance. They are widely used across industries due to their excellent abrasion, corrosion, and temperature resistance. While PVD coatings are highly durable, they are not entirely immune to wear over time, especially under extreme conditions or improper use. However, their wear resistance is superior to many other coating methods, making them a preferred choice for applications requiring long-lasting protection and performance.
Key Points Explained:
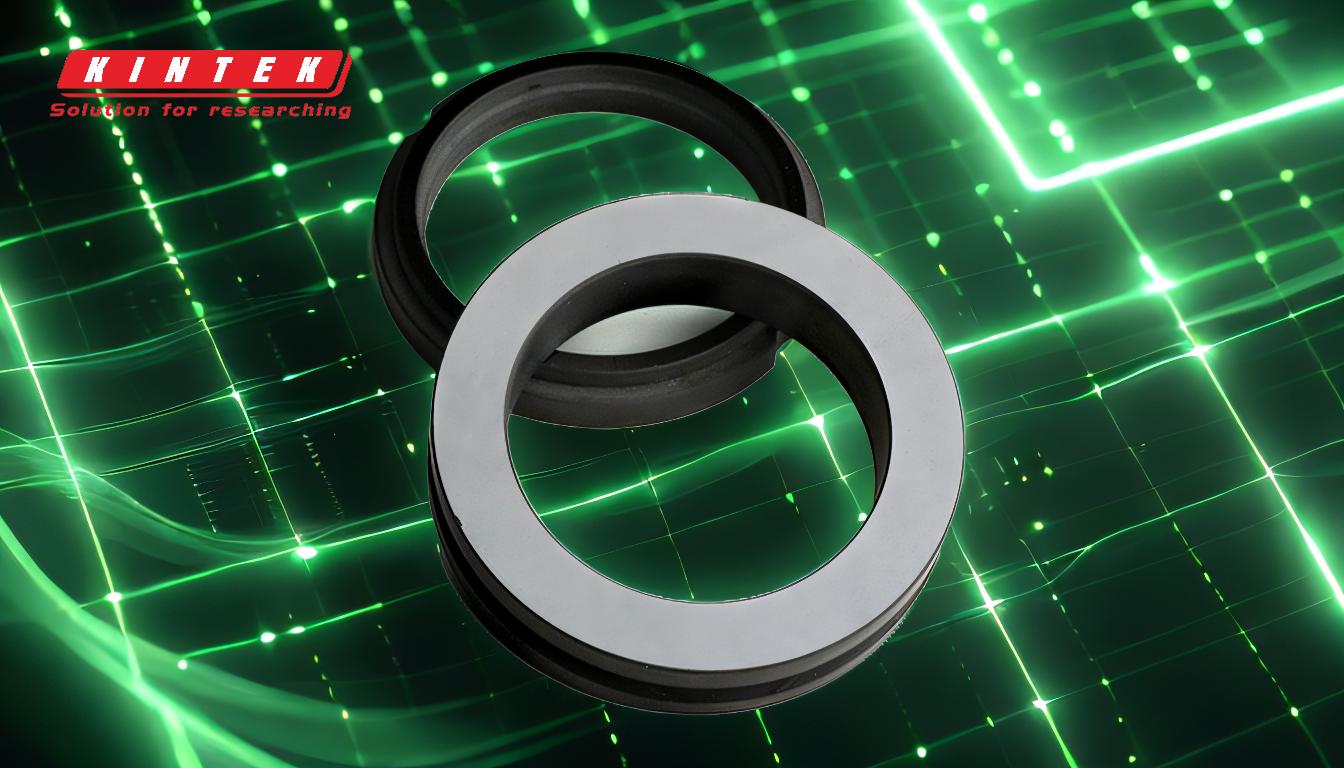
-
Durability of PVD Coatings
- PVD coatings are designed to be highly durable, with exceptional resistance to abrasion, corrosion, and temperature fluctuations.
- They are applied in a thin, uniform layer, which enhances their adhesion to the substrate and contributes to their longevity.
- While they are not indestructible, their wear resistance is significantly higher than many traditional coatings, making them suitable for demanding applications.
-
Factors Affecting Wear
- Environmental Conditions: Exposure to harsh chemicals, extreme temperatures, or abrasive materials can accelerate wear.
- Mechanical Stress: High-impact or high-friction applications, such as cutting tools or engine components, may experience gradual wear over time.
- Substrate Quality: The durability of the coating also depends on the quality of the substrate material and its preparation before coating.
-
Applications Where PVD Coatings Excel
- PVD coatings are used in industries such as aerospace, automotive, medical devices, and electronics due to their thinness, purity, and durability.
- Examples include microchips, optical lenses, solar panels, and protective films, where long-term performance is critical.
-
Maintenance and Longevity
- Proper maintenance and care can extend the lifespan of PVD coatings.
- Avoiding harsh cleaning agents or abrasive tools can help preserve the coating's integrity.
-
Comparison to Other Coating Methods
- PVD coatings outperform many other coating techniques, such as electroplating or chemical vapor deposition (CVD), in terms of durability and environmental resistance.
- Their ability to maintain performance under extreme conditions makes them a preferred choice for high-stress applications.
In summary, while PVD coatings can wear off over time under extreme conditions, their inherent durability and resistance to wear make them one of the most reliable coating options available. Proper application, substrate preparation, and maintenance can further enhance their longevity, ensuring they meet the demands of even the most challenging applications.
Summary Table:
Key Aspect | Details |
---|---|
Durability | Highly resistant to abrasion, corrosion, and temperature fluctuations. |
Factors Affecting Wear | Environmental conditions, mechanical stress, and substrate quality. |
Applications | Aerospace, automotive, medical devices, electronics, and more. |
Maintenance Tips | Avoid harsh cleaning agents and abrasive tools to preserve coating integrity. |
Comparison to Other Methods | Outperforms electroplating and CVD in durability and environmental resistance. |
Enhance your applications with durable PVD coatings—contact us today to learn more!