PVD (Physical Vapor Deposition) coating is a highly durable and advanced finishing technique used in jewelry to enhance its aesthetic appeal and longevity. Unlike traditional electroplating, PVD coatings are more resistant to corrosion, wear, and oxidation, making them suitable for everyday wear. While PVD coatings are not indestructible, they are designed to last significantly longer than electroplated finishes, often enduring over three years with regular use. The process involves depositing a thin, hard layer of material onto the jewelry surface under vacuum conditions, which ensures excellent adhesion and durability. However, like any coating, PVD can wear off over time, especially with rough handling or exposure to harsh chemicals. Proper care can extend the lifespan of PVD-coated jewelry, making it a popular choice for modern, durable, and stylish pieces.
Key Points Explained:
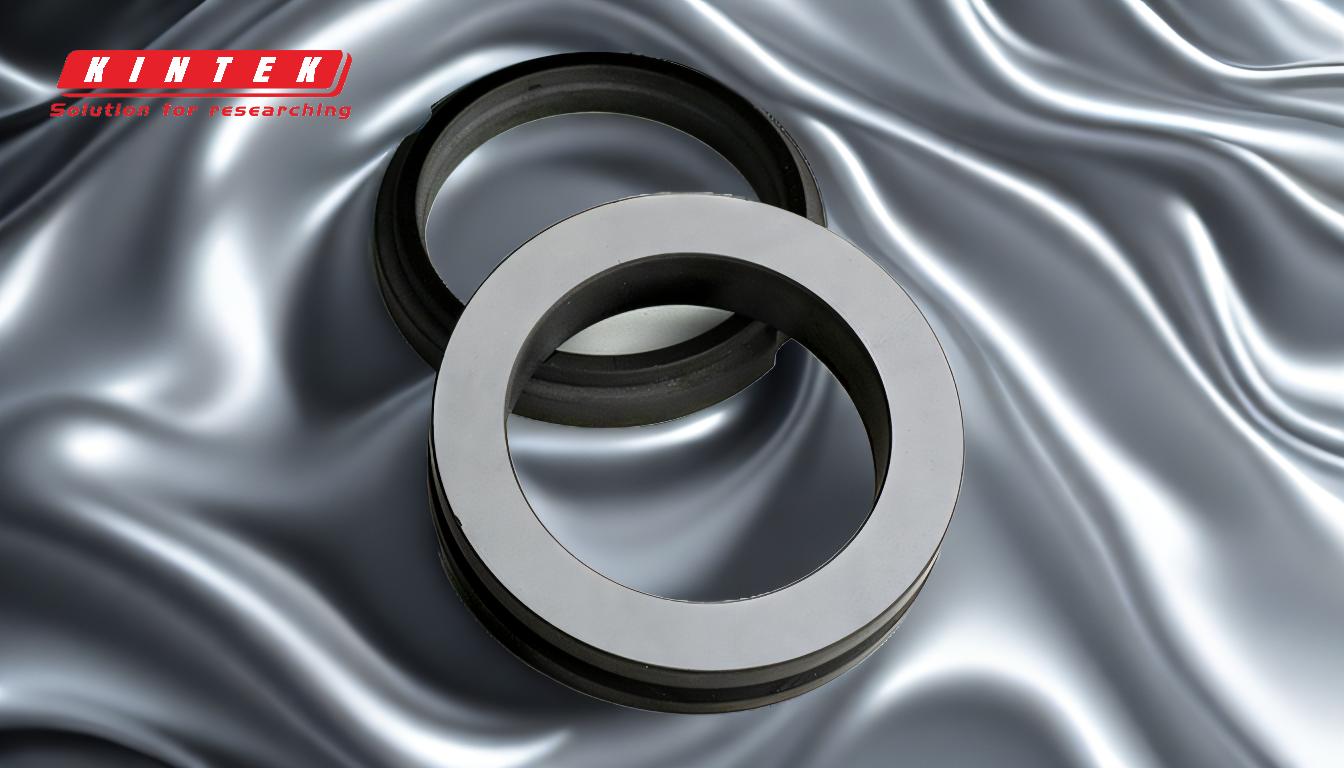
-
Durability of PVD Coatings:
- PVD coatings are known for their high hardness and wear resistance, making them more durable than traditional electroplated finishes. They can withstand everyday wear and tear, often lasting over three years with proper care.
- The coatings are highly resistant to corrosion and oxidation, which helps maintain the jewelry's appearance over time.
-
Thickness and Adhesion:
- PVD coatings are extremely thin, typically ranging from 0.5 to 5 microns. Despite their thinness, they adhere strongly to the substrate due to the vacuum deposition process, which ensures a molecular-level bond.
- This strong adhesion contributes to the coating's longevity and resistance to chipping or peeling.
-
Comparison to Electroplating:
- Unlike electroplated jewelry, which typically lasts about one year, PVD-coated jewelry is designed to last significantly longer. PVD coatings are more resistant to wear, corrosion, and environmental factors.
- The process operates at lower temperatures (around 500 °C), reducing the risk of thermal damage to the substrate and preserving the jewelry's structural integrity.
-
Resistance to Environmental Factors:
- PVD coatings, such as Zirconium Nitride (ZrN), have demonstrated exceptional resistance to neutral salt spray (ASTM B117) and CASS (Copper-Accelerated Acetic Acid-Salt Spray), meeting stringent industry standards.
- This resistance makes PVD-coated jewelry suitable for exposure to moisture, sweat, and other environmental factors without significant degradation.
-
Care and Maintenance:
- While PVD coatings are durable, they are not indestructible. Rough handling, exposure to harsh chemicals, or abrasive cleaning methods can cause the coating to wear off over time.
- To extend the lifespan of PVD-coated jewelry, it is recommended to avoid contact with harsh substances, clean it gently with mild soap and water, and store it properly when not in use.
-
Aesthetic Benefits:
- PVD coatings provide a variety of colors (e.g., gold, rose gold, black, blue) and finishes (e.g., matt, polished), enhancing the visual appeal of jewelry.
- The thin, uniform coating preserves the sharpness and detail of intricate designs, making it ideal for modern and stylish jewelry pieces.
-
Applications Beyond Jewelry:
- The durability and precision of PVD coatings make them suitable for a wide range of applications, including cutting tools, plastic injection molding components, and optical coatings.
- These same properties contribute to the effectiveness of PVD coatings in jewelry, ensuring long-lasting wear and aesthetic appeal.
In conclusion, while PVD coatings on jewelry are highly durable and resistant to wear, they are not entirely immune to damage. With proper care, PVD-coated jewelry can maintain its appearance and functionality for many years, making it a superior choice compared to traditional electroplated finishes.
Summary Table:
Aspect | Details |
---|---|
Durability | Lasts over 3 years with proper care; highly resistant to wear and corrosion. |
Thickness | 0.5 to 5 microns; strong adhesion ensures longevity. |
Comparison to Electroplating | More durable; lasts longer than electroplated finishes. |
Resistance | Resists corrosion, oxidation, and environmental factors like moisture. |
Care Tips | Avoid harsh chemicals; clean gently with mild soap and water. |
Aesthetic Benefits | Available in various colors and finishes; preserves intricate designs. |
Applications | Used in jewelry, cutting tools, and optical coatings for durability. |
Ensure your jewelry stays stunning for years—contact us today for expert advice on PVD coatings!