PVD (Physical Vapor Deposition) coatings are known for their exceptional durability and longevity. While the coating is extremely thin, often only a few atoms thick, it is highly resistant to wear, corrosion, and scratches. Under normal conditions, PVD coatings do not "come off" on their own. However, their lifespan can vary significantly depending on factors such as the substrate material, coating thickness, application conditions, and maintenance. In jewelry, PVD coatings can last up to 10 years or more with proper care, while in industrial applications, they may last for decades or even hundreds of years. The durability of PVD coatings makes them a preferred choice for demanding applications where long-term performance is critical.
Key Points Explained:
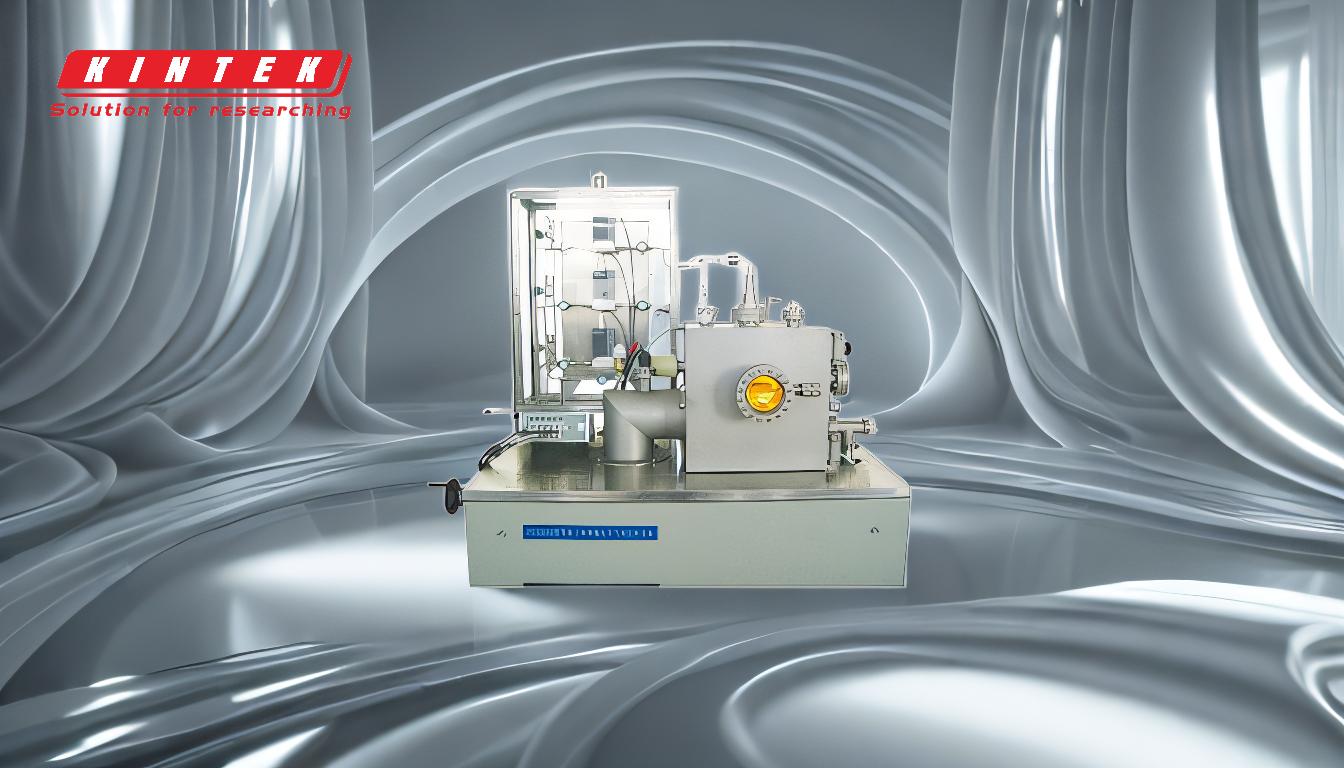
-
Thin but Durable:
- PVD coatings are extremely thin, often only a few atoms thick (up to about a micron). Despite their thinness, they are highly durable due to their hardness and resistance to wear and corrosion.
-
Longevity:
- The lifespan of a PVD coating can range from 10 years to hundreds of years, depending on factors such as:
- Substrate Material: The material being coated plays a significant role in how well the coating adheres and performs.
- Coating Thickness: Thicker coatings generally last longer but may not always be necessary depending on the application.
- Application Conditions: Environmental factors like exposure to chemicals, temperature extremes, and mechanical stress can affect the coating's longevity.
- Maintenance: Proper care and maintenance can significantly extend the life of a PVD coating.
- The lifespan of a PVD coating can range from 10 years to hundreds of years, depending on factors such as:
-
Resistance to Wear and Corrosion:
- PVD coatings are highly resistant to abrasion, corrosion, and scratches. This makes them ideal for use in demanding environments, such as industrial machinery, medical devices, and jewelry.
-
Hardness:
- PVD coatings are extremely hard, almost as hard as diamonds. This hardness makes them difficult to scratch or remove, contributing to their long-lasting nature.
-
Applications:
- Jewelry: In the jewelry industry, PVD coatings can last up to 10 years or more if applied correctly and maintained properly. They enhance the durability of the jewelry and protect it from wear and corrosion.
- Industrial: In industrial applications, PVD coatings are used in tools, machinery, and components that require high durability and resistance to extreme conditions. In these settings, PVD coatings can last for decades or even centuries.
-
Maintenance:
- While PVD coatings are highly durable, their longevity can be extended with proper maintenance. This includes regular cleaning, avoiding harsh chemicals, and protecting the coated surface from excessive mechanical stress.
-
Comparison with Other Coatings:
- PVD coatings are considered superior to traditional finishes in terms of durability and resistance to wear and corrosion. They are often the preferred choice for applications where long-term performance is critical.
-
Conclusion:
- PVD coatings do not "come off" on their own under normal conditions. Their exceptional durability, resistance to wear and corrosion, and long lifespan make them a reliable choice for a wide range of applications. Proper application and maintenance can further enhance their performance and longevity.
Summary Table:
Key Factor | Impact on PVD Coating Longevity |
---|---|
Substrate Material | Determines coating adhesion and performance. |
Coating Thickness | Thicker coatings generally last longer but may not always be necessary. |
Application Conditions | Exposure to chemicals, temperature extremes, and mechanical stress affects longevity. |
Maintenance | Proper care, cleaning, and avoiding harsh chemicals can extend the coating's lifespan. |
Applications | Jewelry: 10+ years; Industrial: Decades to centuries. |
Resistance | Highly resistant to abrasion, corrosion, and scratches. |
Hardness | Nearly as hard as diamonds, making them difficult to scratch or remove. |
Maximize the lifespan of your PVD coatings—contact our experts today for tailored solutions!