Ceramic rods are manufactured through a series of precise steps involving material preparation, shaping, drying, and firing. The process begins with the selection and preparation of raw ceramic materials, such as alumina or zirconia, which are mixed with binders and solvents to form a malleable paste. This paste is then extruded or molded into rod shapes. After shaping, the rods undergo a drying process to remove moisture, followed by high-temperature firing in a kiln to achieve the desired hardness and durability. The final steps may include grinding, polishing, and quality inspection to ensure the rods meet specific dimensional and performance standards.
Key Points Explained:
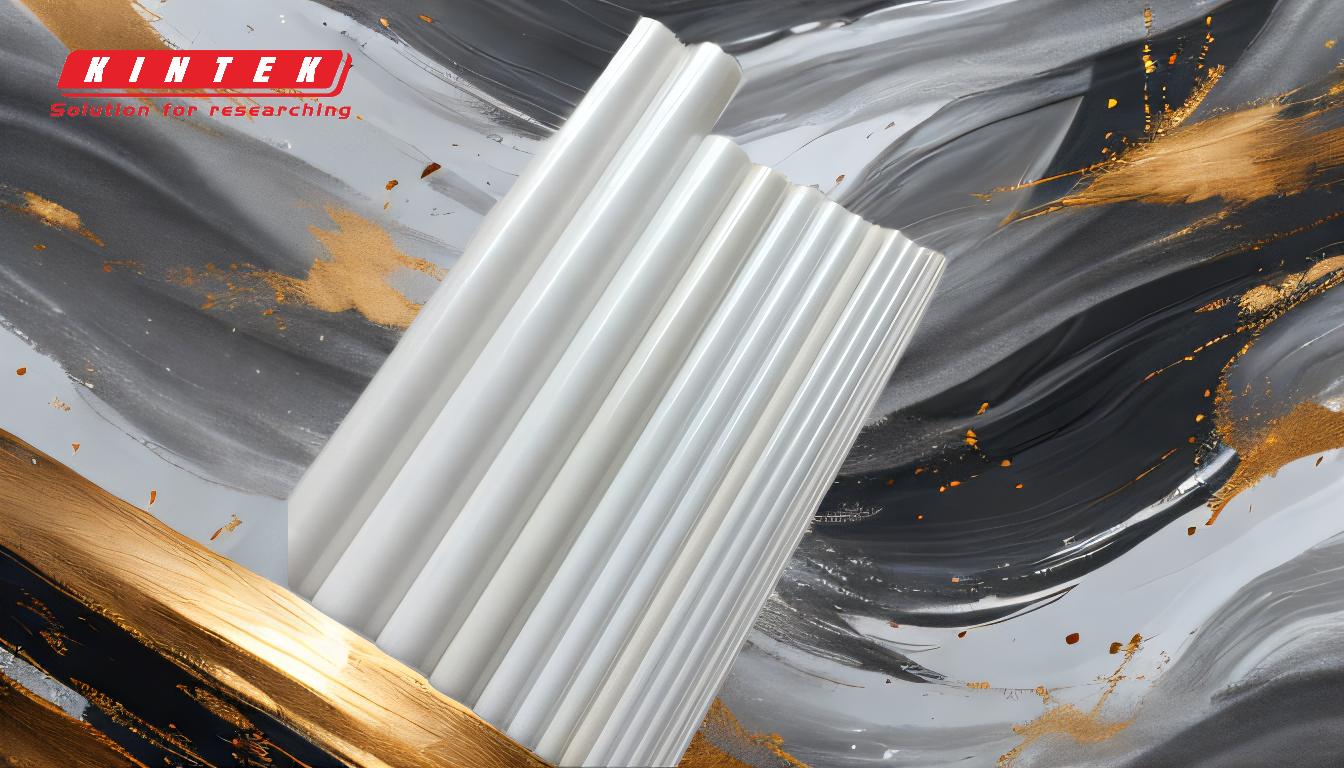
-
Material Selection and Preparation:
- Ceramic rods are typically made from high-performance materials like alumina (Al₂O₃) or zirconia (ZrO₂), chosen for their hardness, thermal stability, and wear resistance.
- Raw materials are ground into fine powders and mixed with binders (e.g., organic polymers) and solvents to create a homogeneous ceramic paste. This paste must have the right consistency for shaping.
-
Shaping the Ceramic Rods:
- The ceramic paste is shaped into rods using extrusion or molding techniques.
- Extrusion: The paste is forced through a die to form long, continuous rods, which are then cut to the desired length.
- Molding: The paste is pressed into pre-designed molds to achieve specific shapes and dimensions.
- Both methods require precise control to ensure uniformity and avoid defects like cracks or air pockets.
- The ceramic paste is shaped into rods using extrusion or molding techniques.
-
Drying Process:
- After shaping, the rods are dried to remove moisture and solvents. This step is critical to prevent cracking or warping during the firing stage.
- Drying is typically done in controlled environments, such as drying ovens, to ensure even moisture removal.
-
Firing (Sintering):
- The dried rods are fired in high-temperature kilns, often reaching temperatures between 1400°C and 1800°C, depending on the material.
- During firing, the ceramic particles bond together through a process called sintering, which increases the density and strength of the rods.
- The firing process also removes any remaining organic binders, leaving behind a pure ceramic structure.
-
Post-Processing:
- After firing, the rods may undergo additional processing steps to achieve the desired surface finish and dimensional accuracy.
- Grinding: The rods are ground to precise diameters and tolerances using diamond or abrasive wheels.
- Polishing: For applications requiring smooth surfaces, the rods are polished to reduce surface roughness.
- These steps ensure the rods meet the required specifications for their intended use.
- After firing, the rods may undergo additional processing steps to achieve the desired surface finish and dimensional accuracy.
-
Quality Inspection:
- The final rods are inspected for defects, dimensional accuracy, and mechanical properties.
- Common inspection methods include visual examination, dimensional measurement, and testing for hardness, density, and thermal properties.
- Only rods that pass these rigorous checks are approved for use in applications such as industrial machinery, medical devices, or electronics.
By following these steps, manufacturers can produce ceramic rods with exceptional mechanical, thermal, and chemical properties, making them suitable for demanding applications across various industries.
Summary Table:
Step | Description |
---|---|
Material Preparation | Raw materials like alumina or zirconia are ground, mixed with binders, and formed into a paste. |
Shaping | Extrusion or molding techniques are used to create rod shapes. |
Drying | Moisture is removed in controlled environments to prevent defects. |
Firing (Sintering) | High-temperature firing bonds particles, increasing strength and density. |
Post-Processing | Grinding and polishing ensure precise dimensions and smooth surfaces. |
Quality Inspection | Rods are tested for defects, dimensions, hardness, and thermal properties. |
Need high-quality ceramic rods for your application? Contact us today to learn more!