Rotary kilns are heated using two primary methods: electric heaters and gas burners. Electric heaters provide precise control over heating rates and temperature distribution, making them versatile for various atmospheres like air, oxygen, nitrogen, and argon. Gas burners, on the other hand, are energy-efficient as they utilize waste heat from the processed material as fuel. Heating can occur either directly (inside the kiln chamber) or indirectly (from outside), depending on the application's requirements. Heat transfer within the kiln happens through conduction, convection, and radiation, with conduction being the most efficient method. The material inside the kiln is heated by radiation from the burner flame, conduction from the refractory lining, and convection from contact with hot gases.
Key Points Explained:
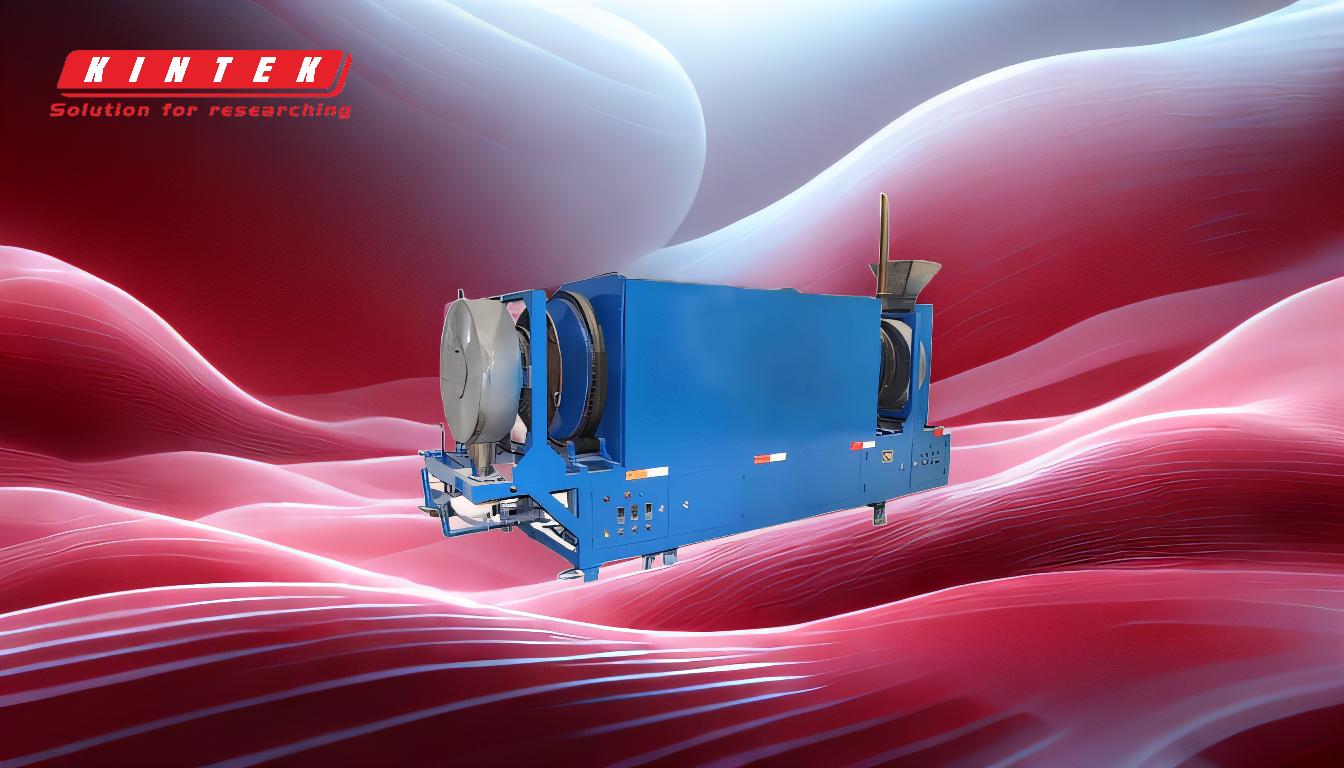
-
Primary Heating Methods:
-
Electric Heaters:
- Provide precise control over heating rates and temperature distribution.
- Suitable for various atmospheres, including air, oxygen, nitrogen, and argon.
- Ideal for applications requiring consistent and controlled heating.
-
Gas Burners:
- Utilize waste heat from the processed material as fuel, enhancing energy efficiency.
- Commonly used in industrial applications where waste heat recovery is feasible.
- Offer a cost-effective solution for large-scale operations.
-
Electric Heaters:
-
Direct vs. Indirect Heating:
-
Direct Heating:
- Heat is applied directly inside the kiln chamber.
- Ensures uniform heating of the material.
- Suitable for processes requiring high temperatures and rapid heating.
-
Indirect Heating:
- Heat is applied from outside the kiln chamber.
- Prevents contamination of the material by combustion gases.
- Ideal for sensitive materials or processes requiring a controlled atmosphere.
-
Direct Heating:
-
Heat Transfer Mechanisms:
-
Conduction:
- Heat transfer through direct contact, such as from the refractory lining to the material.
- Most efficient method of heat transfer in rotary kilns.
-
Convection:
- Heat transfer through the movement of hot gases within the kiln.
- Ensures even distribution of heat throughout the material.
-
Radiation:
- Heat transfer through electromagnetic waves, primarily from the burner flame.
- Effective for surface heating and maintaining high temperatures.
-
Conduction:
-
Material Heating Process:
-
Radiation from Burner Flame:
- Directly heats the material surface, providing rapid temperature increases.
-
Conduction from Refractory Lining:
- Transfers heat from the kiln walls to the material, ensuring consistent internal heating.
-
Convection from Hot Gases:
- Circulates heat throughout the kiln, promoting uniform temperature distribution.
-
Radiation from Burner Flame:
By understanding these key points, purchasers can make informed decisions about the type of rotary kiln heating method that best suits their specific application requirements.
Summary Table:
Aspect | Electric Heaters | Gas Burners |
---|---|---|
Control | Precise control over heating rates and temperature distribution. | Utilizes waste heat for energy efficiency. |
Atmosphere | Suitable for air, oxygen, nitrogen, and argon atmospheres. | Ideal for industrial applications with waste heat recovery. |
Heating Method | Direct or indirect heating based on application needs. | Direct or indirect heating based on application needs. |
Heat Transfer | Conduction (most efficient), convection, and radiation. | Conduction, convection, and radiation. |
Applications | Consistent and controlled heating for sensitive processes. | Cost-effective for large-scale operations with waste heat utilization. |
Need help choosing the right rotary kiln heating method? Contact our experts today for personalized advice!