Semiconductor thin films are created using a variety of deposition techniques, which can be broadly categorized into chemical and physical methods. These techniques allow for precise control over the thickness, composition, and properties of the films, which are crucial for their application in electronic devices such as transistors, sensors, and photovoltaic cells. Key methods include Chemical Vapor Deposition (CVD), Physical Vapor Deposition (PVD), sputtering, and evaporation. Each method has its own advantages and is chosen based on the specific requirements of the semiconductor material and its intended application.
Key Points Explained:
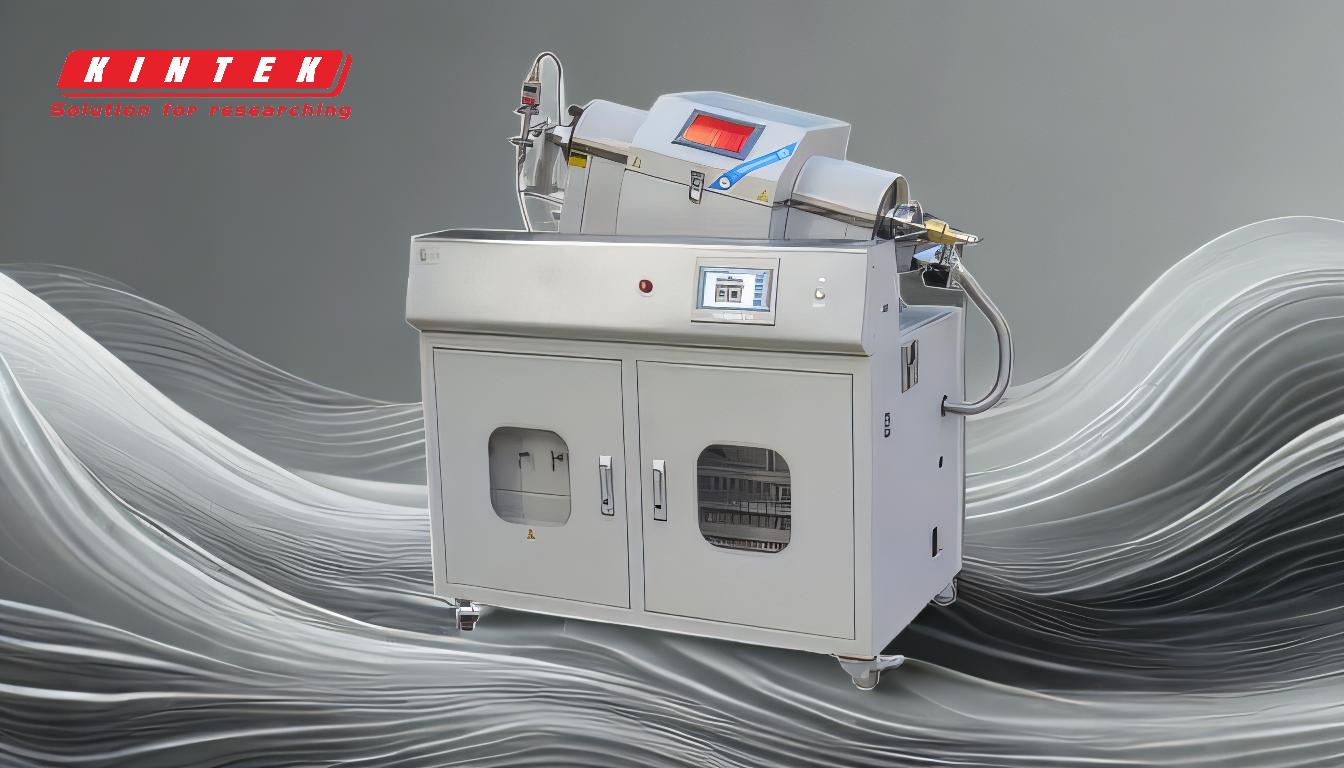
-
Categories of Deposition Methods:
- Chemical Methods: These include techniques like electroplating, sol-gel, dip coating, spin coating, Chemical Vapor Deposition (CVD), Plasma-Enhanced CVD (PECVD), and Atomic Layer Deposition (ALD). These methods involve chemical reactions to form the thin film on the substrate.
- Physical Methods: These include sputtering, thermal evaporation, carbon coating, electron beam evaporation, Molecular Beam Epitaxy (MBE), and Pulsed Laser Deposition (PLD). These methods rely on physical processes to deposit the film.
-
Chemical Vapor Deposition (CVD):
- CVD is a widely used method for creating thin films and nanomaterials, including graphene. It involves the reaction of gaseous precursors to form a solid film on the substrate. This method is particularly useful for fabricating semiconductor thin films used in technologies like solar cells.
- Plasma-Enhanced CVD (PECVD): A variant of CVD that uses plasma to enhance the chemical reactions, allowing for lower temperature deposition, which is beneficial for temperature-sensitive substrates.
-
Physical Vapor Deposition (PVD):
- Sputtering: This method uses plasma or gaseous atoms (like argon) to bombard the target material, causing its atoms to be ejected and deposited onto the substrate. It is widely used for creating uniform thin films with precise control over thickness.
- Evaporation: This involves heating the target material until it evaporates, and the vapor then condenses on the substrate to form a thin film. Techniques include thermal evaporation and electron beam evaporation.
-
Atomic Layer Deposition (ALD):
- ALD is a highly precise method that allows for the deposition of films at the atomic level. It involves sequential exposure of the substrate to different precursors, resulting in extremely uniform and conformal films. This method is ideal for applications requiring very thin and precise layers.
-
Spin Coating and Dip Coating:
- Spin Coating: A liquid precursor is applied to the substrate, which is then spun at high speeds to spread the liquid into a thin, uniform layer. This method is commonly used for creating polymer-based thin films.
- Dip Coating: The substrate is dipped into a liquid precursor and then withdrawn at a controlled speed, allowing the liquid to form a thin film on the substrate.
-
Applications of Semiconductor Thin Films:
- Transistors: Thin films are used in the fabrication of transistors, where precise control over thickness and composition is critical for performance.
- Sensors: Thin films are used in various types of sensors, including gas sensors and biosensors, due to their high sensitivity and selectivity.
- Photovoltaic Devices: Thin films are essential in the production of solar cells, where they help in efficient light absorption and conversion to electrical energy.
-
Importance of Precision and Purity:
- The quality of semiconductor thin films is crucial, as even minor impurities or defects can significantly impact the performance of the device. High-precision deposition techniques and optimal manufacturing conditions are essential to ensure the purity and performance of the films.
By understanding these key points, one can appreciate the complexity and precision involved in the production of semiconductor thin films, which are fundamental to modern electronic and photovoltaic technologies.
Summary Table:
Category | Methods | Key Features |
---|---|---|
Chemical Methods | CVD, PECVD, ALD, electroplating, sol-gel, dip coating, spin coating | Chemical reactions for film formation; precise control over thickness and purity |
Physical Methods | Sputtering, thermal evaporation, electron beam evaporation, MBE, PLD | Physical processes for deposition; uniform and conformal films |
Applications | Transistors, sensors, photovoltaic devices | High sensitivity, efficient light absorption, and critical performance control |
Ready to enhance your semiconductor production? Contact our experts today for tailored solutions!