Sintered parts are manufactured through a multi-step process that transforms powdered materials into solid, durable components. The process typically involves preparing a powder mixture, compacting it into a desired shape, and then sintering it at high temperatures to bond the particles together. This method is widely used for metals, ceramics, and other materials, offering precise control over material properties and complex geometries. The sintering process ensures the final product has structural integrity, reduced porosity, and enhanced mechanical properties. Below, the key steps and their significance are explained in detail.
Key Points Explained:
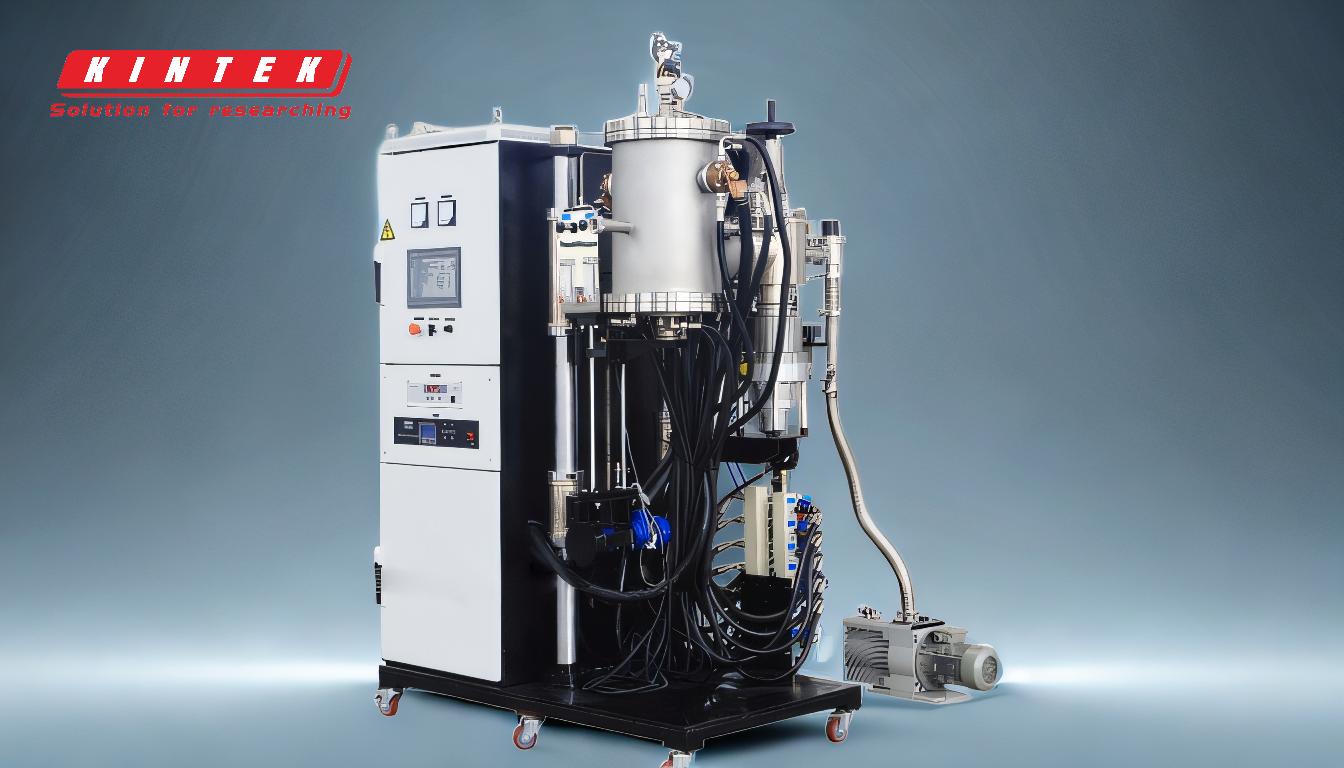
-
Powder Preparation and Mixing
- The process begins with the preparation of raw materials in powdered form. These powders are often mixed with additives like binders, lubricants, or coupling agents to improve flowability, compaction, and sintering behavior.
- For metals, the powder may be alloyed or blended to achieve specific mechanical or thermal properties. In ceramics, the powder is often calibrated to ensure uniformity in particle size and composition.
- This step is critical because the quality of the powder directly affects the final product's density, strength, and dimensional accuracy.
-
Compacting the Powder
- The mixed powder is then compacted into a "green body" using high-pressure tools, such as hydraulic presses or die molds. This step shapes the powder into the desired form, creating a coherent but fragile structure.
- The compaction process can be done at room temperature or with slight heating, depending on the material. The applied pressure ensures the particles are in close contact, which is essential for effective sintering.
- For complex shapes, techniques like cold welding, 3D-printed lasers, or isostatic pressing may be used to achieve precise geometries.
-
Sintering in a Controlled Atmosphere
- The green body is transferred to a sintering furnace, where it is heated to a temperature just below the material's melting point. This step activates diffusion mechanisms, causing the particles to bond and densify.
- In some cases, liquid phase sintering (LPS) is employed, where a small amount of liquid forms at the particle interfaces, accelerating densification and improving material properties.
- The sintering atmosphere (e.g., inert gas, vacuum, or reducing environment) is carefully controlled to prevent oxidation or contamination and to ensure uniform heating.
-
Cooling and Solidification
- After sintering, the material is gradually cooled to room temperature. This step allows the newly formed bonds to stabilize, resulting in a solid, unified mass with reduced porosity and enhanced mechanical strength.
- The cooling rate can influence the material's microstructure and properties, such as hardness and toughness.
-
Post-Sintering Processing
- Depending on the application, sintered parts may undergo additional steps like machining, surface finishing, or assembly. For ceramics, diamond tools or ultrasonic machining are often used to achieve precise dimensions.
- In some cases, sintered parts are metallized or brazed to join with other components, enhancing their functionality in complex assemblies.
-
Quality Control and Testing
- Throughout the process, parameters like temperature, pressure, and sintering time are closely monitored to ensure the final product meets specifications.
- The sintered parts are tested for properties such as density, porosity, strength, and dimensional accuracy to ensure they are suitable for their intended use.
By following these steps, manufacturers can produce sintered parts with tailored properties for a wide range of applications, from automotive components to advanced ceramics in electronics and aerospace. The sintering process offers a cost-effective and versatile method for creating high-performance materials with complex shapes and precise tolerances.
Summary Table:
Step | Key Details |
---|---|
Powder Preparation | Raw materials in powdered form, mixed with additives for improved properties. |
Compacting the Powder | High-pressure tools shape the powder into a 'green body' with precise geometry. |
Sintering | Heated below melting point in controlled atmosphere to bond particles. |
Cooling and Solidification | Gradual cooling stabilizes bonds, reducing porosity and enhancing strength. |
Post-Sintering Processing | Additional steps like machining or surface finishing for final dimensions. |
Quality Control | Testing for density, porosity, strength, and dimensional accuracy. |
Learn how sintered parts can enhance your manufacturing process—contact our experts today!